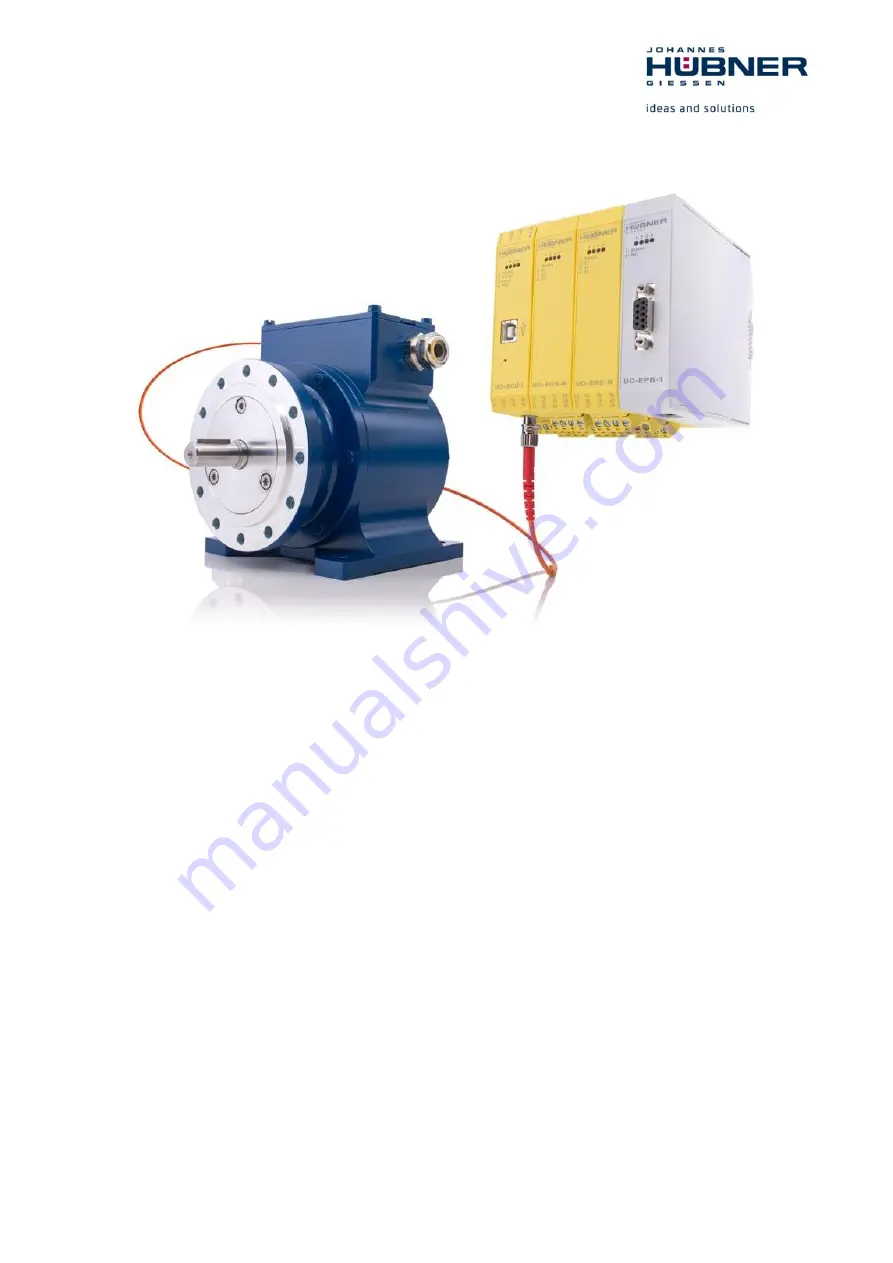
English
Translation of the original configuration instructions
Edition: 01 2021
ID 76633
Configuration instructions
U-ONE
®
-SAFETY-LWL
Universal encoder system
–
Generation II
Read the operating and assembly manual before carrying out assembly, starting
installation, or completing other work.
Store the manual for future use.