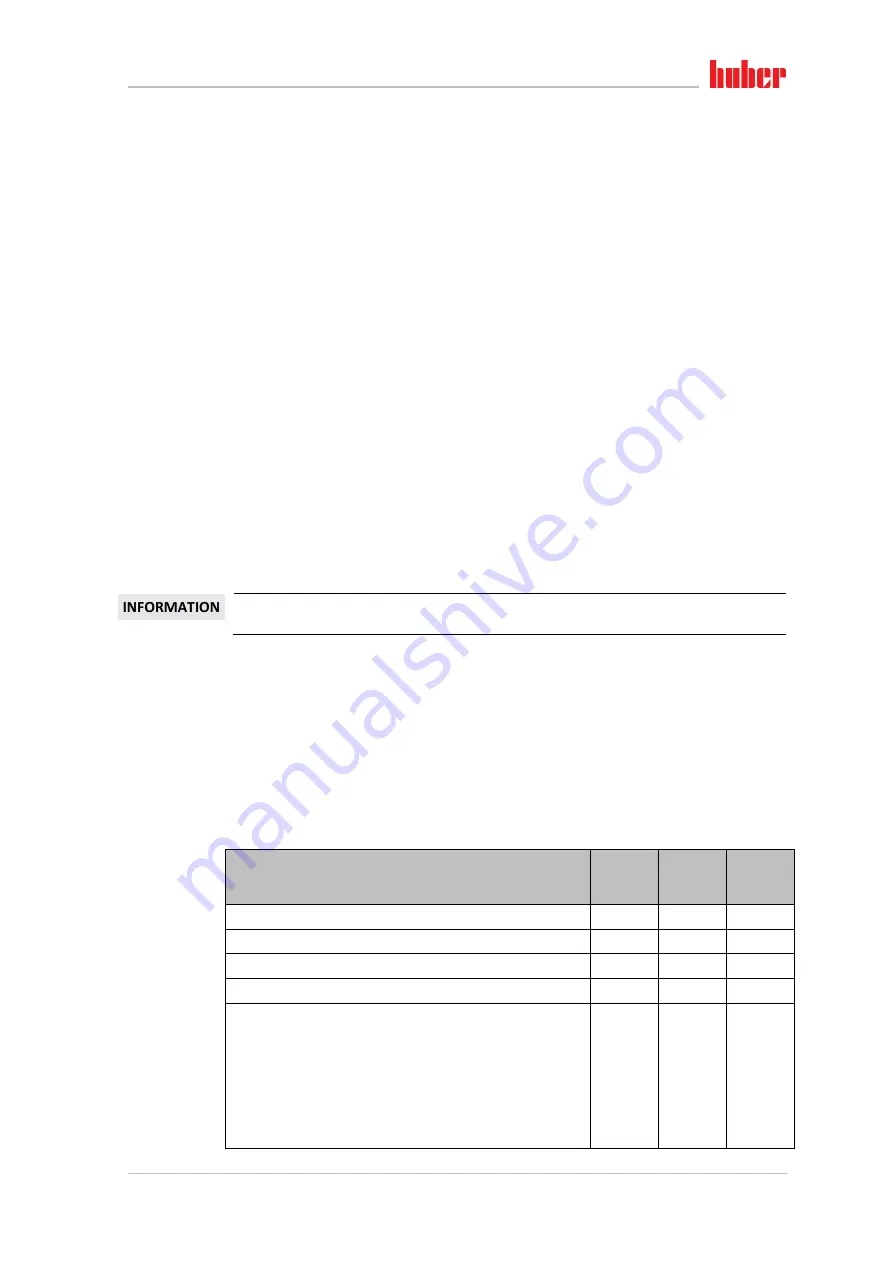
Function description
Chapter 3
OPERATION MANUAL
V2.2.0en/09.08.21//17.12
Unichiller® eo Desktop
35
application (glass apparatus) and cause bursting. Adjust the Delta T value to your application.
▪
Select the thermal fluid to be used in such a way that it not only permits the minimum and maxi-
mum working temperature but is also suitable with regard to fire point, boiling point, and viscosi-
ty. In addition, the thermal fluid must be compatible with all the materials in your system.
▪
Avoid bending the temperature control and cooling water hoses (if required). Use suitable angle
pieces and lay the hose connections with a large radius. Take the minimum bending radius from
the data sheet of the temperature control hoses used.
▪
The selected hose connections must be able to withstand the thermal fluid, the working tempera-
tures and the admissible maximum pressure.
▪
Check the hoses at regular intervals for any material fatigue (e.g. cracks, leaks).
▪
Keep the temperature control hoses as short as possible
-
The inside diameters of the temperature control hoses must correspond at least to the
pump connections. Select bigger inside diameters for longer line lengths to compensate
for pressure loss in the piping.
-
The viscosity of the thermal fluid determines the pressure drop and influences the tem-
perature control result, especially at low working temperatures.
-
Too small connectors and couplers and valves can generate significant flow resistance.
Your application will therefore be slower to reach its design temperature.
▪
Basically, you should only use the thermal fluid recommended by the manufacturer and only
within the usable temperature and pressure range.
▪
The application should be roughly at the same height of or below the temperature control unit if
the temperature control process is close to the boiling temperature of the thermal fluid.
▪
Fill the temperature control unit slowly, carefully and evenly. Wear the necessary personal pro-
tective equipment, such as goggles, heat-proof and chemically resistant gloves, etc.
▪
The temperature control circuit must be vented after filling and setting all required parameters. This is
required to ensure trouble-free operation of the temperature control unit and hence your application.
For water-cooled temperature control units, please take the cooling water temperature necessary for perfect
operation and the required differential pressure from the data sheet.
→
3.4
“Pilot ONE®” controller
Please note the figure
“Pilot ONE”
.
→
Page 6.
The basic version of “Pilot ONE” (Basic) can be upgraded in three stages (from “Basic” to “Exclusive”,
from “Exclusive” to “Professional”, and from “Professional” to “Explore”).
3.4.1
Functional overview of “Pilot ONE®”
You can verify, and optionally upgrade, the delivery version of your temperature control unit using
Pilot ONE, category “E-grade”.
Temperature control units / E-grade
E-grade
Basic
E-grade
Exclusive
E-grade
Profes-
sional
Brewing thermostats
–
X
O
Unistat temperature control units
–
–
X
UniCAL
–
–
X
Other temperature control units
X
O
O
E-grade “Explore”
(only for “Unistat”-series temperature control units)
The E-grade includes E-grade “Professional” functionalities.
In addition it includes:
– Sensor calibration for return sensor
– Return temperature display
– Display of performance (estimated or calculated from volume flow)
– Display mode “Explore” instead of “numerically large”
– PB commands correspond to DV-E-grade, except: Temperatures only
in 0.01
°C and volume flows only in 0.1
l/min.
–
–
O
Overview of the
E-grade variants