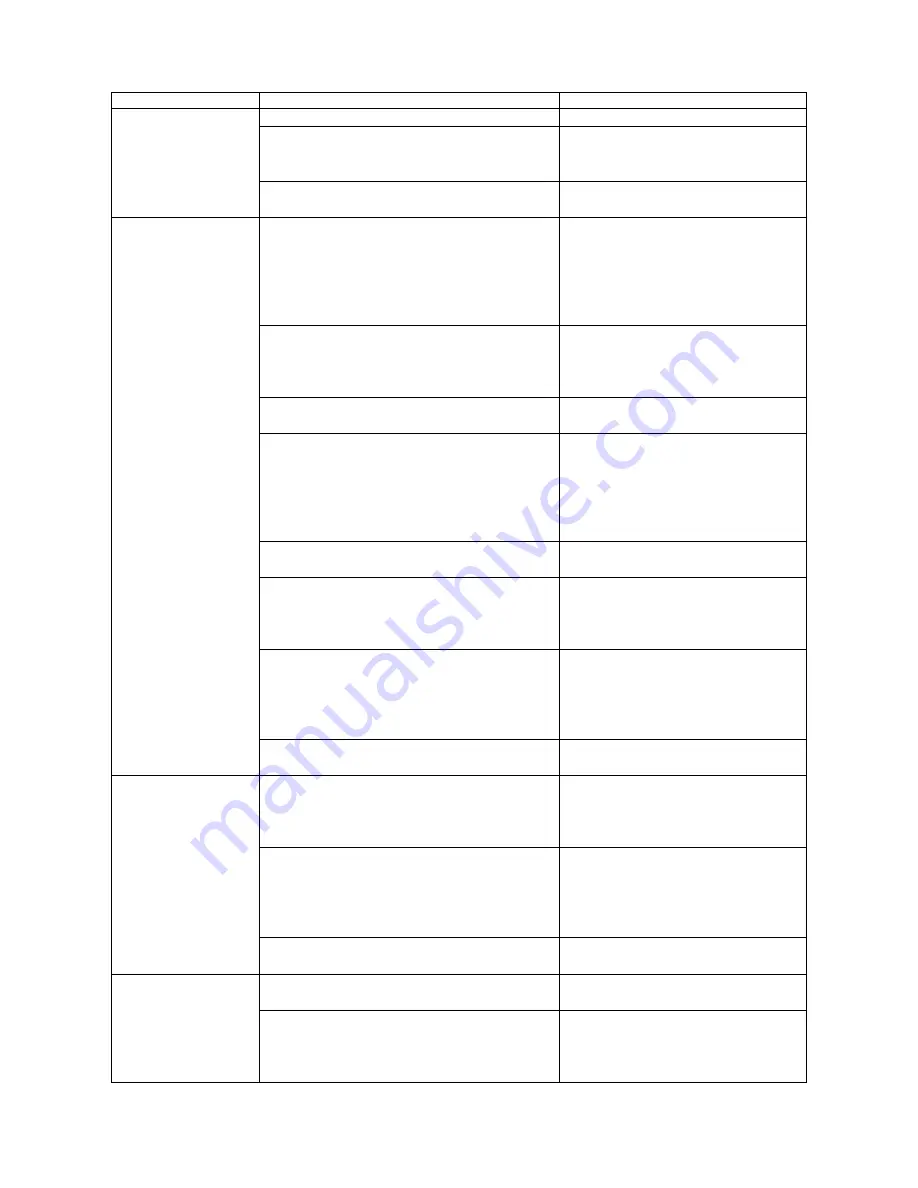
28
Alerts in alert window:
Alert
Error causes
Rectification
Auger circuit
The main plug on the burner is not correctly placed.
The plug is tight to place – press it to fit.
Condensator to the auger motor is either defective or
there is a loose connection.
If the condensator is defective operation can
only be established with a new condensator;
check the connections (terminals).
Loose connection: Cables from motor to print on
burner
Check all connections (terminals)
No fuel
The plug on the feeder motor is not correctly placed.
Remove the plug and check the plug in the
motor cabinet; try to place the plug again;
use the test function for outputs in ”Service
Menu” in order to test the function of the
motor: measure whether there is voltage in
the terminals.
There is a loose connection in the plug to the feeder
motor.
Check the plug; it might be necessary to
disassemble it in order to check the
connections in the screw terminals; test the
motor with the test function.
There is a loose connection in the plug on the feeder
motor.
See above.
The feeder auger is stuck
Test the function of the motor with the
output test in ”Service Menu”; if the motor
cannot rotate the feeder auger it might be
necessary to dismount the motor and test
without the load from the auger; firstly
check whether there is any voltage.
The feeder auger is full of sawdust
Test the quantity of fuel that the feeder
auger can give – see 4.2
The light sensor is defective
Remove the light sensor; go into the menu
”Light sensor” in ”User’s menu”; select
”Current light strength”; at daylight the light
sensor must show a value > 200
The light sensor is dirty
Remove the light sensor and check its
surface; clean the sensor and test its light
strength with the help from the menu
“Current light strength” in “Light sensor” in
“User’s menu”
The light sensor connection is loose
Check the light sensor’s connection in the
terminal on the print in the burner.
Burner overheated
The burner surface is too hot – the bi-metal sensor is
released
The boiler needs to be cleaned – the
resistance through the boiler is too big;
negative draught in the chimney: try to let
the chimney cleanout door be open.
Bi-metal sensor is defective
The burner can be brought into temporarily
operation by short circuiting the terminals;
the burner must not operate without
supervision without operating bi-metal
sensor; to be replaced asap.
Connection to bi-metal sensor is cut off
Check the connections at the terminals on
the burner print.
Boiler sensor
If the extra sensor is not used or if could be
left out, then exchange the 2 sensors.
Connection to boiler sensor is cut off
Check the connections to the terminal in the
junction box; measure the resistance via the
sensor. It should be around 108 Ohm at 20
°C.
Summary of Contents for TPK
Page 1: ...1 with or without Scandpell ...
Page 38: ...38 8 EEC declaration of conformity ...
Page 39: ...39 9 Test certificate ...
Page 40: ...40 Rev 11 100913 ...