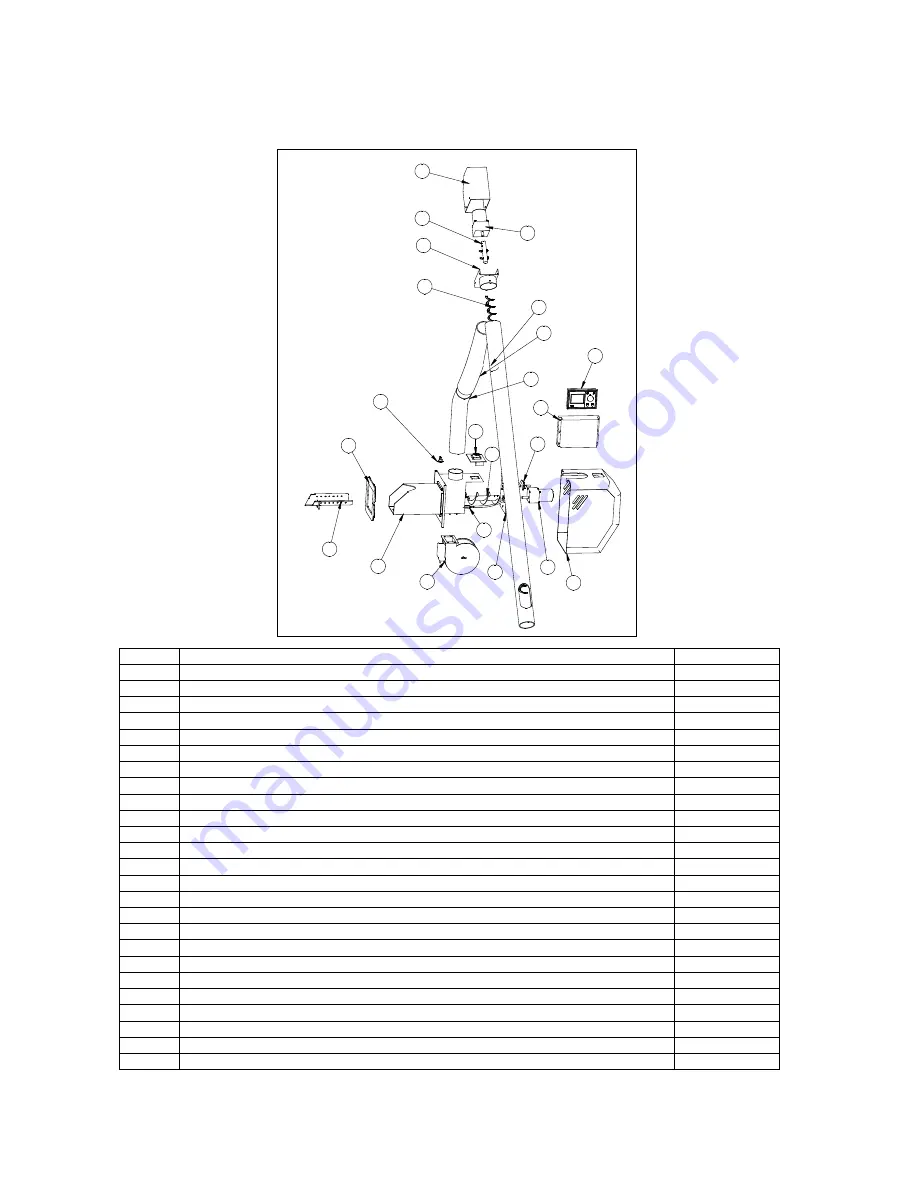
31
7. Product data
7.1 Spare parts Scandpell
Item
Description
Part no.
1
Burner housing
016024
2
Burner cartridge
016002
3
Fan (black model)
016003
5
Fan (blank model)
016030
4
Back plate for burner
016004
5
Ignition element
016005
6
Electrical connection plate
016006
7
Fibre gasket
016007
8
Burner auger motor
016008
9
Burner auger
016009
10
Flame sensor
016010
11
Feeder motor
016017
12
Feeder auger
016016
13
Auger pipe
016015
14
Feeder motor cover
016021
15
Anchor
016019
16
Anchor plate
016018
17
Burner cabinet
016011
18
Control unit
016040
19
Downpipe, metal
016013
20
Flexible downpipe
016012
21
Bi-metal sensor
016022
22
Control box
016025
-
Boiler temperature sensor
016026
-
Extra temperature sensor (5 meter)
016027
4
3
2
5
6
7
8
9
11
12
13
10
016000
14
15
16
19
20
21
17
Pos
Vare nr.
Tekst
1
016024
Brænderhoved
2
016002
Brænderzone
3
016003
Ventilator
4
016004
Bagplade for brænder
5
016005
Tændelement
6
016006
Elforbindelse
7
016007
Fiberpakning
8
016008
Sneglemotor brænder
9
016009
Snegl brænder
10
016010
Flammesensor
11
016017
Sneglemotor
12
016016
Snegl
13
016015
Snegle rør
14
016021
Kappe for snegl
15
016019
Aksel for snegl
16
016018
Holder for snegl
17
016011
Kappe for brænder
18
016014
Styring
19
016013
Rør for brænder
20
016012
Flexrørfor brænder
21
016022
Bimetalsensor
22
016025
Styringsboks
1
18
22
Summary of Contents for TPK
Page 1: ...1 with or without Scandpell ...
Page 38: ...38 8 EEC declaration of conformity ...
Page 39: ...39 9 Test certificate ...
Page 40: ...40 Rev 11 100913 ...