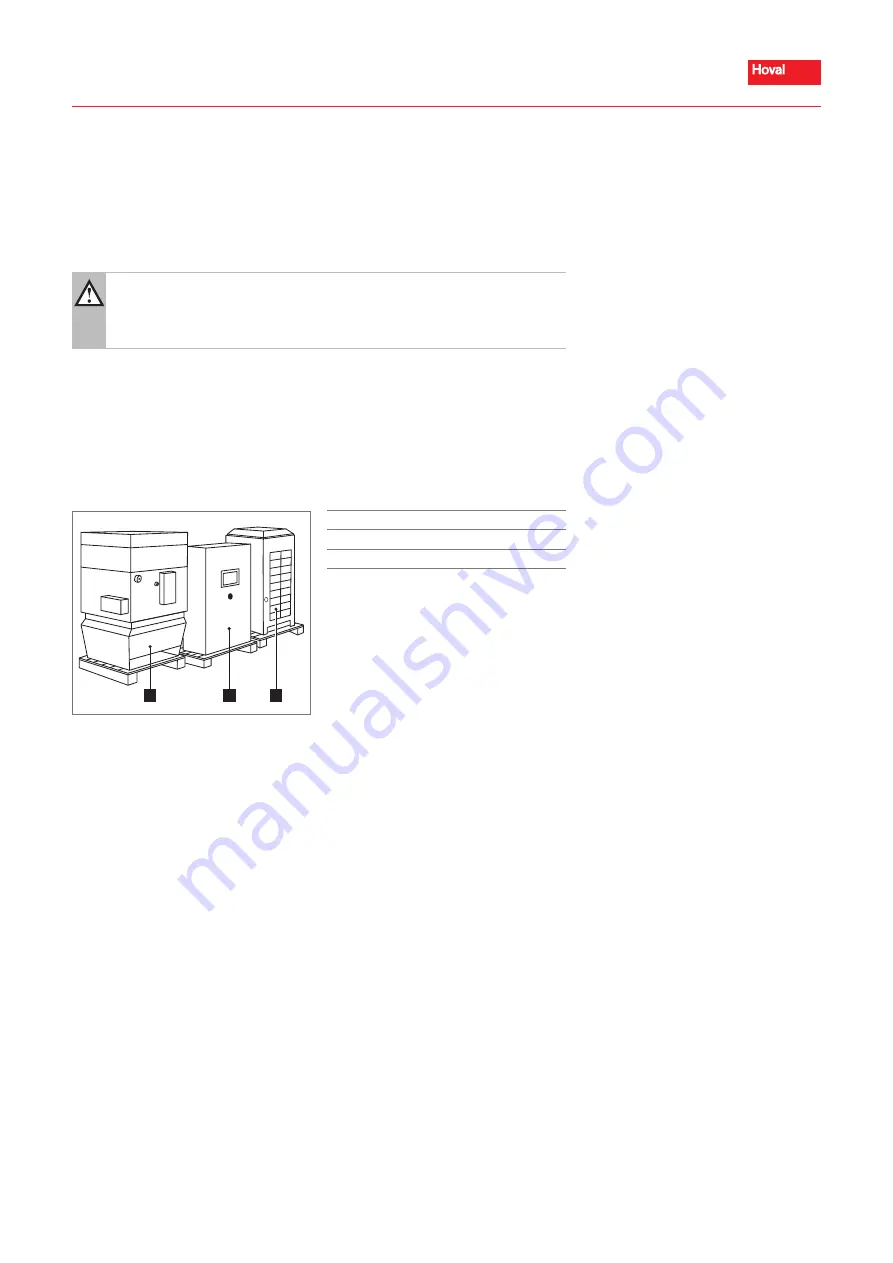
7 Transport and installation
Caution
Risk of injury from incorrect handling. Transport, assembly and installation
work may only be performed by specialists. Observe safety and accident
prevention regulations.
7.1 Scope of delivery
The scope of delivery includes:
■
TopVent
®
TP unit
■
Condensing unit
■
Accessories (installation material, temperature sensors)
■
Optional components
1
2
3
■
1
TopVent
®
TP
■
2
Zone control panel
■
3
Condensing unit
Fig. 10: Delivery of the components on pallets
Accessories
The following accessories are supplied separately:
■
Fresh air temperature sensor and room air temperature sensor (in the zone
control panel)
■
Gas temperature sensor, connection pipe between coil and expansion valve,
self-adhesive insulating mat (in separate cardboard box)
Options
The following optional components are supplied separately:
■
Trap (in separate cardboard box)
■
Condensate pump (in separate cardboard box)
■
Mixing valve (in separate cardboard box)
■
Return temperature sensor (in separate cardboard box)
■
Hydraulic assembly (on separate pallet)
■
Additional room temperature sensors, combination sensor room air quality,
temperature and humidity (in zone control panel)
■
Condensing unit options:
– Condensate drain pan (in separate cardboard box)
– Heating for condensate drain pan (in separate cardboard box)
– Protection hoods (on separate pallet)
Preparation
■
Use a forklift with a sufficiently long fork to unload (at least 1.8 m).
■
Check the consignment against the delivery documents and the order
confirmation to ensure that it is complete. Report missing parts and any
damage immediately in writing.
26
TopVent
®
TP
Transport and installation
4 218 024-en-04
Summary of Contents for TopVent TP
Page 46: ...46 4218024 en 04...
Page 47: ...47 4218024 en 04...