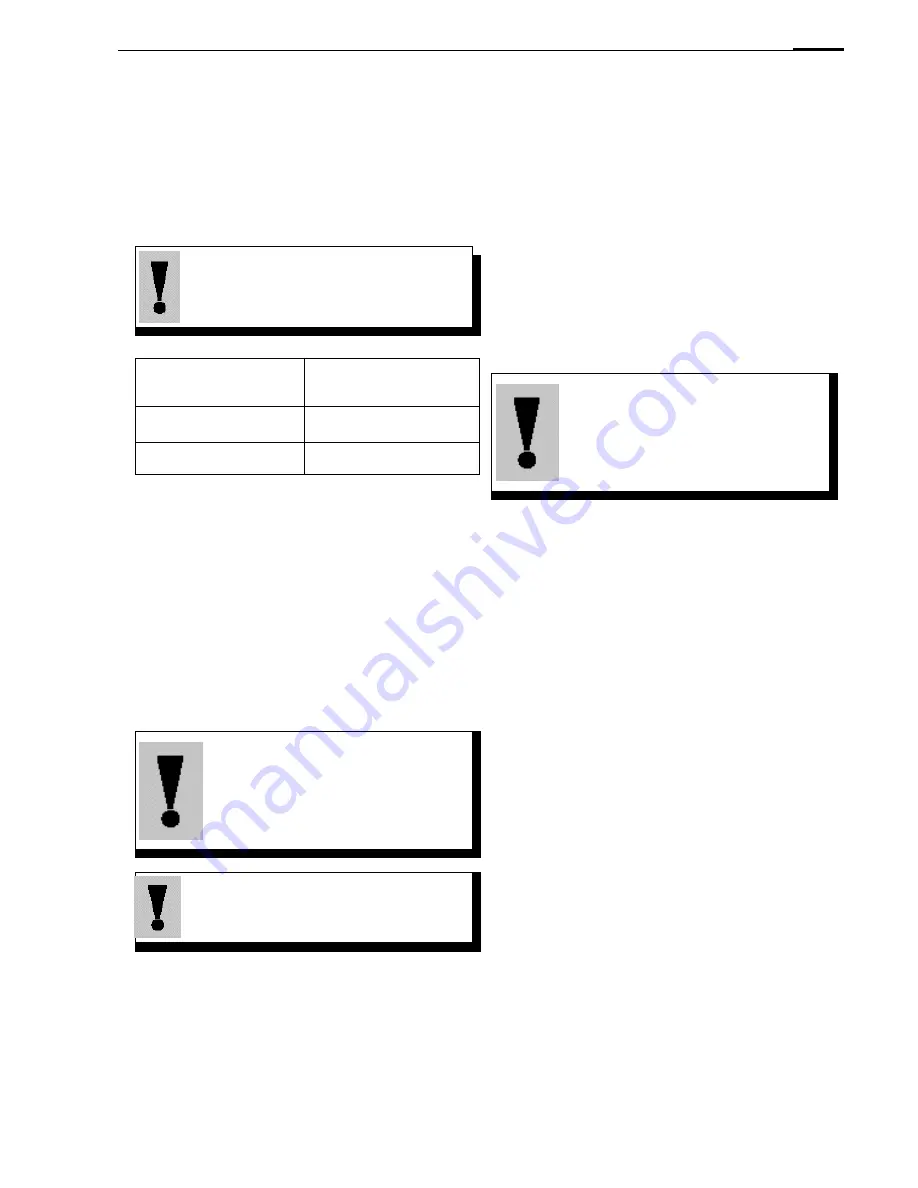
15
Periodic Inspection
Note: Before opening the inspection
cover always ensure you have a
spare inspection cover joint.
Cleaning
The period between cleaning will depend on op-
erating temperature and hardness of water. Lo-
cal conditions will serve as a guide. Normally de-
scaling will be required less often than with con-
ventional calorifiers.
The following procedure should be adopted:
(1) Remove calorifier top casing panel.
(2) Remove cleanout cover for calorifier internals.
(3) Scrape the inside surface with a non ferrous
scaper.
Note: Chemical cleaning can be carried out if re-
quired, but such work should be undertaken in
accordance with the instructions of the de-scal-
ing compound manufacturer.
We recommend chemical treatment specialist
such as Aquazur. After chemically cleaning the
DHW calorifier internal, ensure that the unit is
thorougly flushed out with clean water.
Following cleaning, replace cleanout cover us-
ing a new gasket to prevent leaks.
Inspection and Maintenance
Draining Down
(1) Ensure that both primary and secondary
pumps are switched off.
(2) Isolate the primary inlet and outlet.
(3) Fit hose to primary drain which should be in-
stalled in primary outlet and run the hose to
a gulley.
Note: The primary side of the
calorifier MUST always be
drained before the secondary.
The secondary MUST always be
filled before the primary.
Draining the calorifier down
should be done by following the
procedure below:-
When filling the calorifier
follow the above procedure
but in reverse.
The user is advised to carry out periodic inspec-
tion between main servicing periods and it is rec-
ommended that the specialist servicing company
also carries them out.
•
Inspect the calorifier casing for obvious signs
of damage, corrosion or deterioration.
•
Inspect the calorifier siting for signs of crack-
ing or settling.
•
Inspect all pipes and connections for obvious
damage or deterioration.
•
Remove calorifier top panel and examine in-
terior for corrosion and deterioration.
Inspection and Maintenance
(4) Open primary vent valve.
(5) Open primary drain.
(6) Isolate all secondary connections.
(7) Fit hose to the secondary drain which is lo-
cated underneath the calorifier and run the hose
to a gulley.
(8) (On sealed systems) Open manual second-
ary vent valve (this should be fitted in secondary
flow between calorifier and isolating valve).
(9) Open secondary drain valve.
Model
Joint Cat No.
CT plus 180
414035
CT plus 280-520
414007