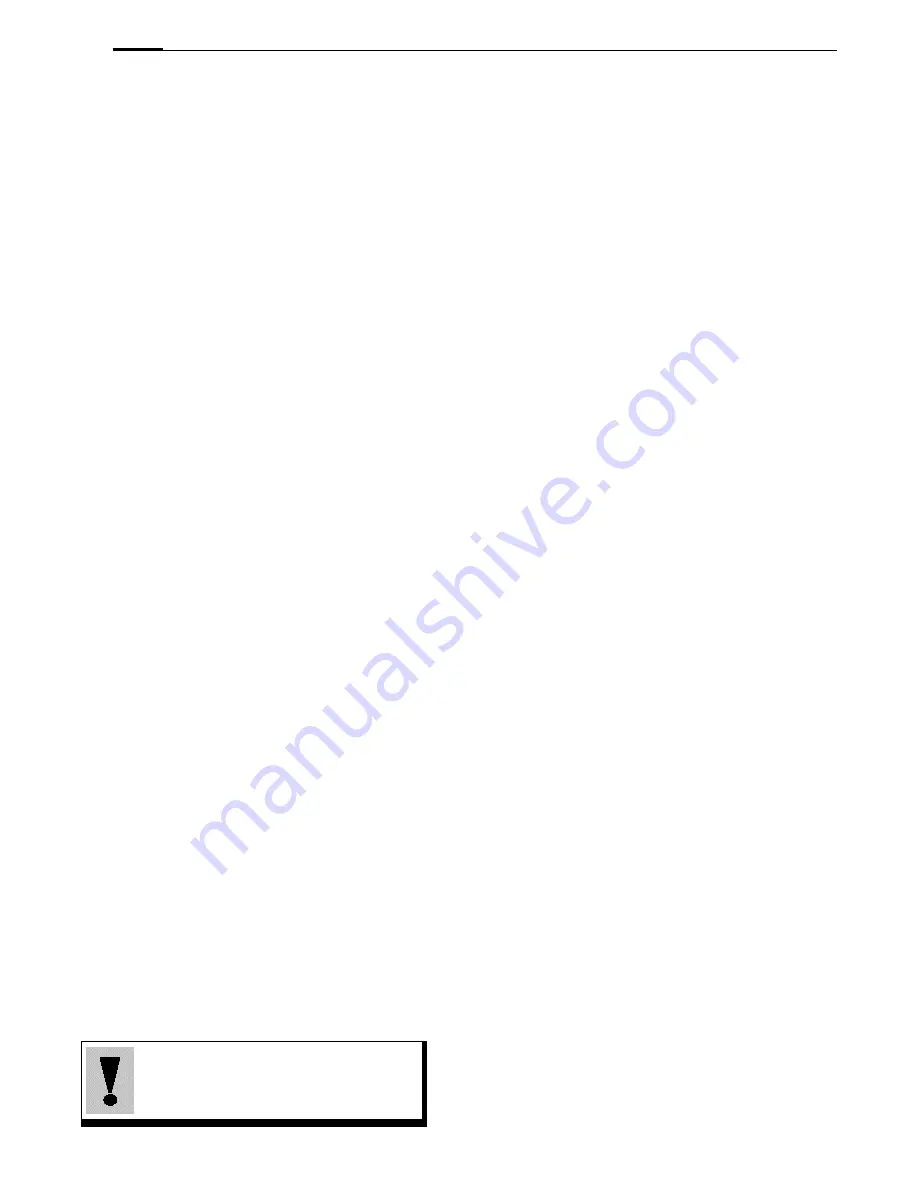
16
Immersion Heaters
Immersion heaters
General
•
All work should be carried out by suitably qualified
personnel.
•
Heaters must be handled with care and stored in
dry conditions.
•
Adequate withdrawal space must be provided to
allow the removal of the heater assembly.
•
Carefully remove all protective packaging and
visually inspect unit for any transit damage.
•
All prevailing rules, regulations and bylaws in force
at the time and place of installation must be
observed.
•
Heaters must only be immersed in the fluid they
are designed to heat.
•
The introduction of alternative fluids even in small
concentrations for purposes such as sterilising
may cause serious damage to the heater and will
invalidate the warranty.
•
Any modification not carried out by Heatex Limited
or its approved agent will invalidate certification
and warranty.
•
Precautions must be taken to prevent damage to
enclosure seals.
Installation
•
The heater should be securely fixed in position and
all terminal connections checked for tightness
before energising.
•
The installed orientation of horizontally mounted
heaters must be such that any thermostats or
other temperature sensors are uppermost.
•
Sealing gaskets must be undamaged.
•
The terminal box must not be used for tightening
heater into tank or vessel.
Electrical Supply Connection
•
Refer to wiring diagram on page 17.
•
The cable entry or gland plate is positioned on the
side of the terminal box.
•
Before connection ensure that the supply
corresponds with that specified on the rating label.
•
Ensure that the sizes and types of cables to be
used are suitably rated for the load and temperature
of the unit.
•
Each heater must be protected by a suitably rated
over current device.
•
The cables must enter the heater terminal box via
a suitable cable gland to maintain the IP rating and
be fitted by a qualified person.
Earth Connection
Operation
•
Ensure that the active sections of all the heating
elements are fully immersed in the fluid to be
heated at all times whilst energized.
•
Heat is transferred by means of electric heating
elements.
•
Control of the heater is facilitated by
thermostats, thermocouples or RTDs and
reference should be made to the wiring diagram
inside cover to ensure that these are correctly
connected and set prior to energising the heater.
•
Where a manual reset thermostat or cut-out is
installed, the terminal box cover will have to be
removed after isolating the heater to enable a
reset to be carried out.
THESE HEATERS MUST BE EARTHED
An earth connection is provid-
ed inside the terminal box.
Routine Maintenance
Maintenance
•
All prevailing site safety regulations shall be
adhered to at all times.
•
Equipment is to be fully isolated from the
electrical supply and locked off before and whilst
any work is being carried out.
3 Monthly
•
Generally inspect the equipment for external
damage or leaks.
6 Monthly
•
Isolate the electrical supply and remove the
cover.
•
Ensure the terminal box is clean and dry
internally.
•
Ensure the electrical terminals are intact and
secure.
•
Check that the heating element insulation
resistance is at least 2 mega ohms.
•
Check the continuity of all elements.
•
Refit cover with new gasket if required.
•
Ensure that earth continuity is maintained
between all exposed conductive material and
main site structure.
Annually
•
Carry out all 3 monthly and 6 monthly checks
as above.
•
Check for element failure or low insulation
resistance.
•
If heaters are being left unused for a period
greater than 3 months, carry out 6 monthly
maintenance before energizing.