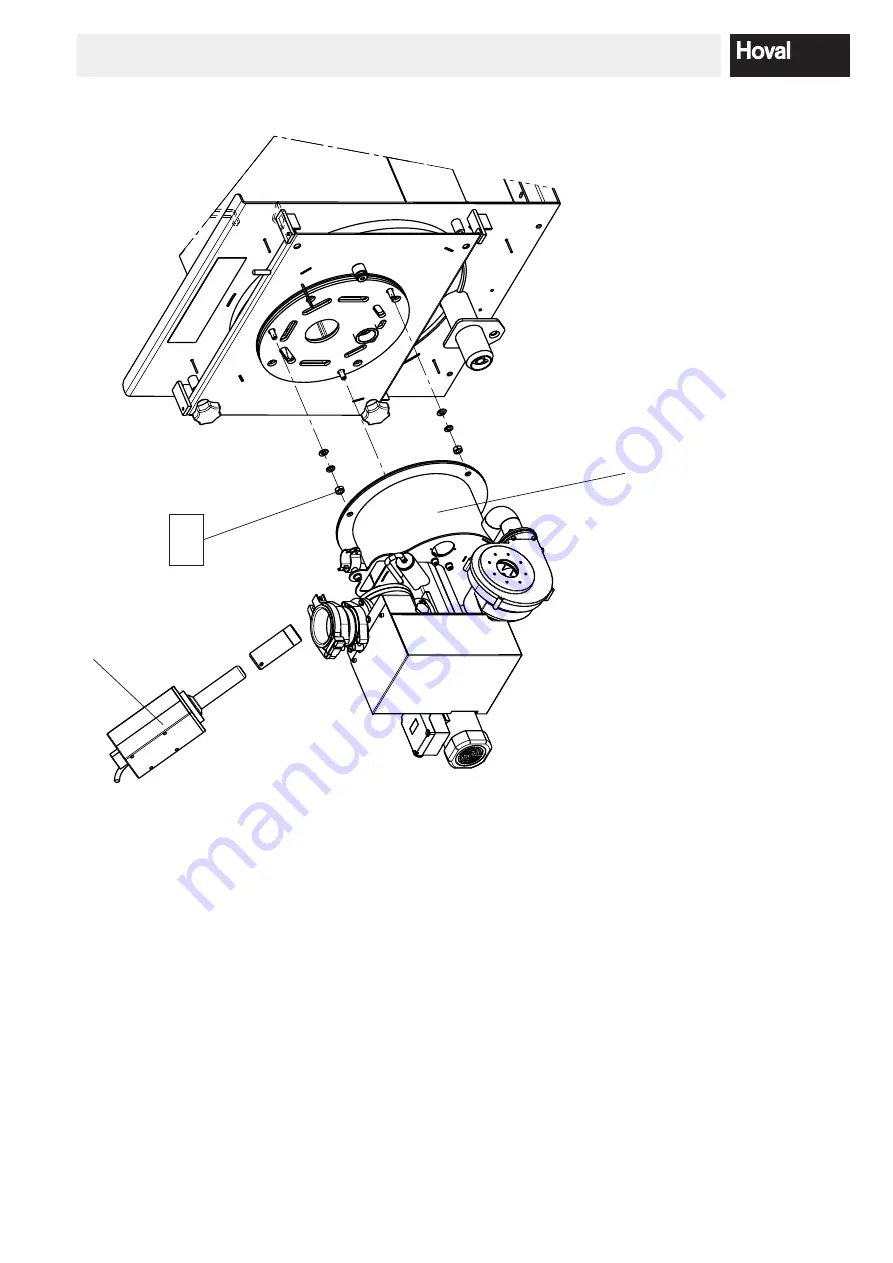
3.5
Fitting the thermal insulation
BioL
yt
(50-75)
Attachment set D
8.
Attach the insulation
mat (1) on the pins
provided
on
the
burner
flange
and
secure
with
iso-clips
9.
Attach
the
insulation mat
(2,
2a)
on the
pins welded
to
the rear wall
of
the boiler and secure with the iso-
clips (Fig. 09) provided.
10.
Place
the
insul
ation mat
(3)
around the
base of
the
water jacket (black sides
outwards) and
secure
with
tension springs (3a).
11.
Place the insulation mat (4) around
the top of the
water jacket (black sides outwards and starting at Pos. 5) and secure with tension springs (3a), two plastic straps (4a) and strap fasteners (4b, Fig.
Do not overtighten the straps (reduced in
-
sulating value)
The
remaining
insulation
mats
are
fitted
prior
to installation of the casing
Fig. 09
Fig. 10
3.6
Fitting the burner BioL
yt
(50-75)
Attachment set B
12.
Close the combustion chamber door (tighten the palm grips).
13.
Install burner mechanism (7).
Do not forget the
gasket
.
14.
Insert the fan heater (8) into the ignition tube.
Fig. 12
4212946
32-BioLyt (50-75) / grma / 05.06.2014 M 1 : 10
8
7
B
13
4 214 852 / 01
ASSEMBLy BIOLyT (50-75)
Summary of Contents for BioLyt 100
Page 7: ...7 4 214 852 01 NOTES...
Page 21: ...21 4 214 852 01 NOTES...
Page 51: ...51 4 214 852 01...