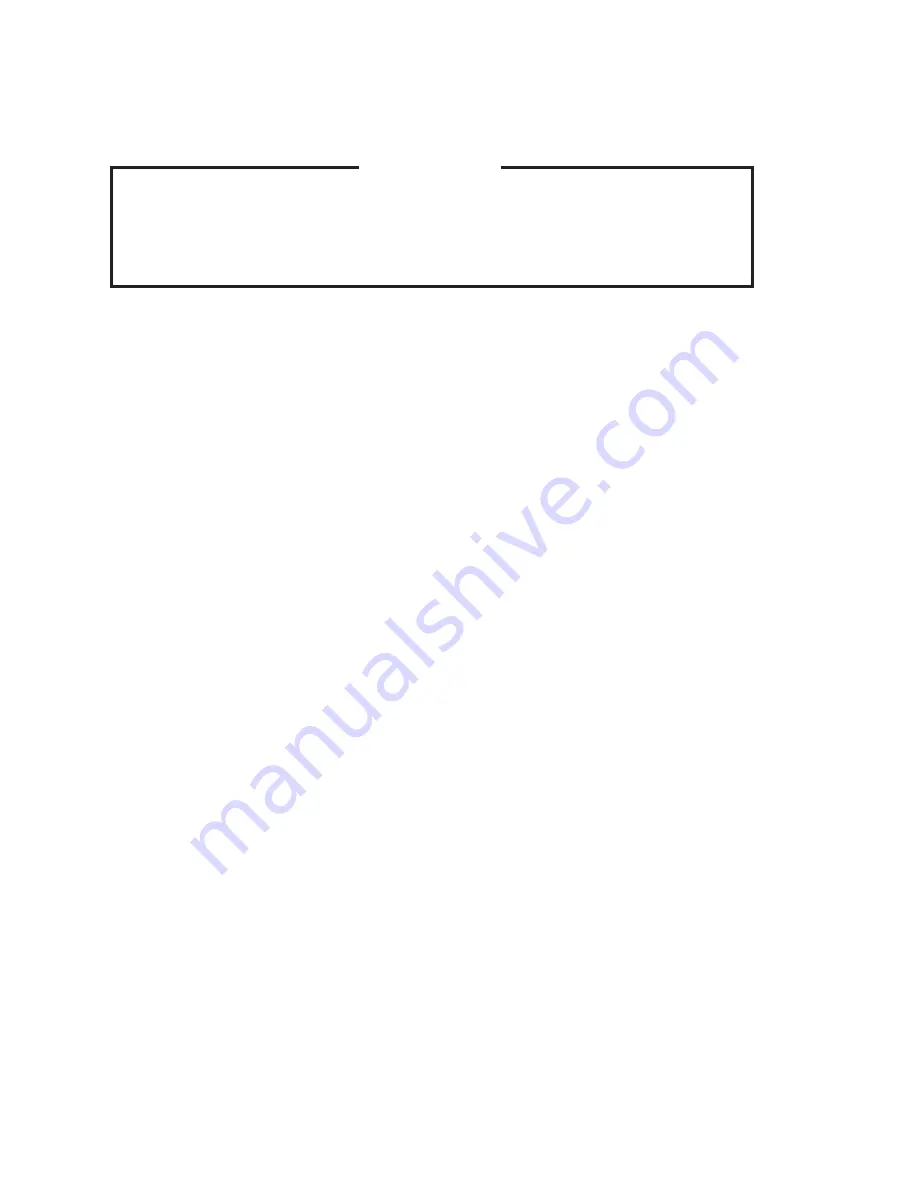
44
6. REMOVAL AND REPLACEMENT OF WATER REGULATING VALVE -
WATER-COOLED MODEL ONLY
IMPORTANT
Always install a new Drier every time the sealed refrigeration system is
opened. Do not replace the Drier until after all other repairs or replacement
have been made.
1) Turn off the power supply, remove the panels and close the Water Supply Line Shut-
off Valve.
2) Recover the refrigerant and store it in an approved container.
3) Disconnect the Capillary Tube using brazing equipment.
4) Disconnect the Flare-connections of the valve.
5) Remove the screws and the valve from the Bracket.
6) Install the new valve, and braze the Capillary Tube.
7) Install the new Drier.
8) Check for leaks using nitrogen gas (140 PSIG) and soap bubbles.
9) Connect the Flare-connections.
10) Evacuate the system, and charge it with refrigerant. See the Nameplate for the required
refrigerant charge and type.
11) Open the Water Supply Line Shut-off Valve, and turn on the power supply.
12) Check for water leaks.
13) See “IV. 1. ADJUSTMENT OF WATER REGULATING VALVE.” If necessary, adjust
the valve.
14) Replace the panels in their correct position.
Summary of Contents for F-800MAH
Page 13: ...13 III TECHNICAL INFORMATION 1 WATER CIRCUIT AND REFRIGERATION CIRCUIT F 800MAH C...
Page 14: ...14 F 800MWH C...
Page 15: ...15 2 WIRING DIAGRAM F 800MAH C F 800MWH C...
Page 17: ...17 b When Reservoir has been filled Gear Motor starts immediately...
Page 18: ...18 c Compressor starts about 60 sec after Gear Motor starts...
Page 19: ...19 d Bin Control operates and about 6 sec later Compressor and Gear Motor stop simultaneously...
Page 20: ...20 e Low Water Except Water cooled Model...
Page 23: ...23 h When Flush Timer operates for 15 min every 12 hours...
Page 26: ...26 4 TIMING CHART...
Page 27: ...27...
Page 28: ...28...