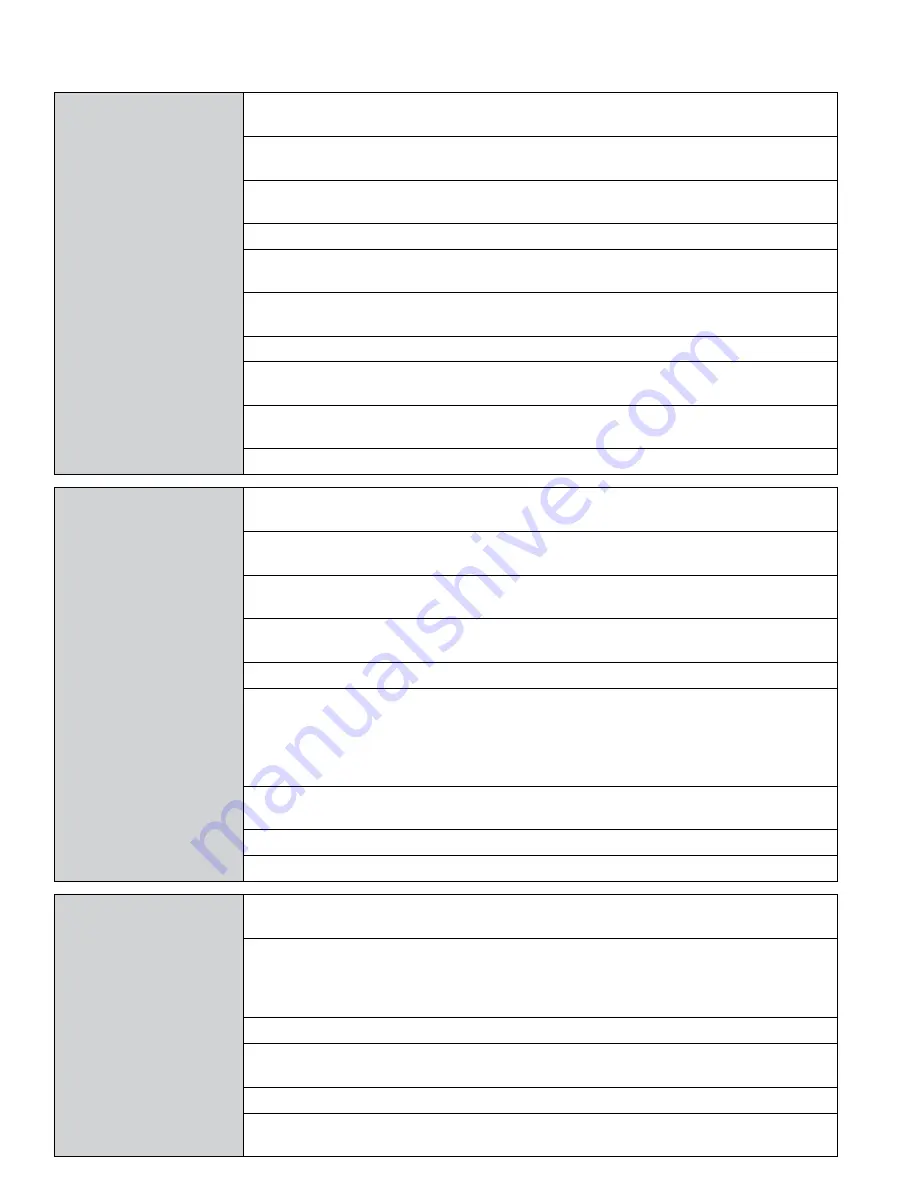
16
TROUBLESHOOTING
Handle will not come
to bottom of stroke
Do not force the handle
(37) . If you meet with
any resistance, shut off
the shot and powder
and slowly return the
handle (37) back to
normal while unlatching
the rotating pawl (94) .
1 . Check to see the loader is mounted near the front of the bench,
allowing the handle (37) to come completely down .
2 . Check to see if the size die body (14) adjustment has changed
or if the size die ring cap (19) has loosened .
3 . Check that the de-prime punch guide (8) is threaded all
the way up on the size die ejector bolt (62) .
4 . Check to see that you are not seating a second primer on top of an already primed case .
5 . Check the primer seater punch (20) to see if it is adjusted too low .
Readjust to seat the primer when the handle (37) is depressed .
6 . Check to see that you aren’t trying to seat a second wad on top
of another and the wad entered the shell correctly .
7 . Check to see that shells are in alignment and the correct shell is in each station .
8 . Check for an obstruction inside the shell which would prevent
you from depriming or repriming the case .
9 . Check to see that you aren’t trying to load a high base wad
shell when you are set up for low base wads .
10 . Check to see if a loaded shell has rolled underneath one of the eccentric arms .
Handle will not turn
to normal position
on backstroke.
DO NOT FORCE
THE HANDLE . Shut
off the powder and
shot and unlatch the
rotating pawl (94) .
1 . Check the clevis link (13) to see if it is bent and hanging up on
the size die eject bolt (62) . Replace if necessary .
2 . Check the primer seater station to see that the primer was fully
seated . If not, lower the primer seater punch (20) .
3 . Check to see that the wad is being fully seated and not
pulling back up into the wad guide bracket (101) .
4 . Check the wad guide bracket (101) to see that the wad guide return spring (106B)
is attached and that the bracket is fastened to the wad guide rod (105) .
5 . Check the charge bar cam (9) adjustment to see that it hasn’t slipped .
6 . Check for an obstruction, spilled shot, etc ., between the shell plate ring (110)
and the platen casting (107) . If there is, you may need to rotate the pawl
(94) clock wise and take the shell plate nut (91) off and lift the shell plate
(45) off the platen (107) and clean out the shot . When the shot is cleaned
out, replace the components in reverse order as you took them off .
7 . Lift each shell up against the shell plate (45) to see if a primer flange
may be catching in a platen casting (107) indention .
8 . Check to see if the shell plate (45) is dragging on the shell retainer spring (63) .
9 . Check to make sure the primer was fully removed at Station One .
Primers do not drop
or drop erratically.
If primers do not drop into
the shell plate (45), or drop
erratically, shut off the shot
and powder and unlatch
the rotating pawl (94) .
1 . Make sure the primer feed body (42) is adjusted low enough to open
the primer stop unit (78) which allows a primer to drop .
2 . Check alignment of primer feed body (42) with the shell plate (45) . The taper of the primer
feed body (42) should enter the chamfer in the shell plate (45), but not touch . When there
are no shells in the crimp die (59), pressure on the size die (14) may tip the platen casting
(107) enough to cause erratic drop . When possible, make adjustments with all stations full .
3 . Check that the auto advance unit (83) is fully advancing and stopping in the correct location .
4 . See that the primer feed body (42) is not burred on the inside, preventing
the primers from dropping freely . If burred, remove with small file .
5 . Check the primer feed body (42) to see that it is not burred on the ends and that it is straight .
6 . Inspect the plastic primer top unit (78) for flash around the fingers
and make sure that the foot moves freely on the body .