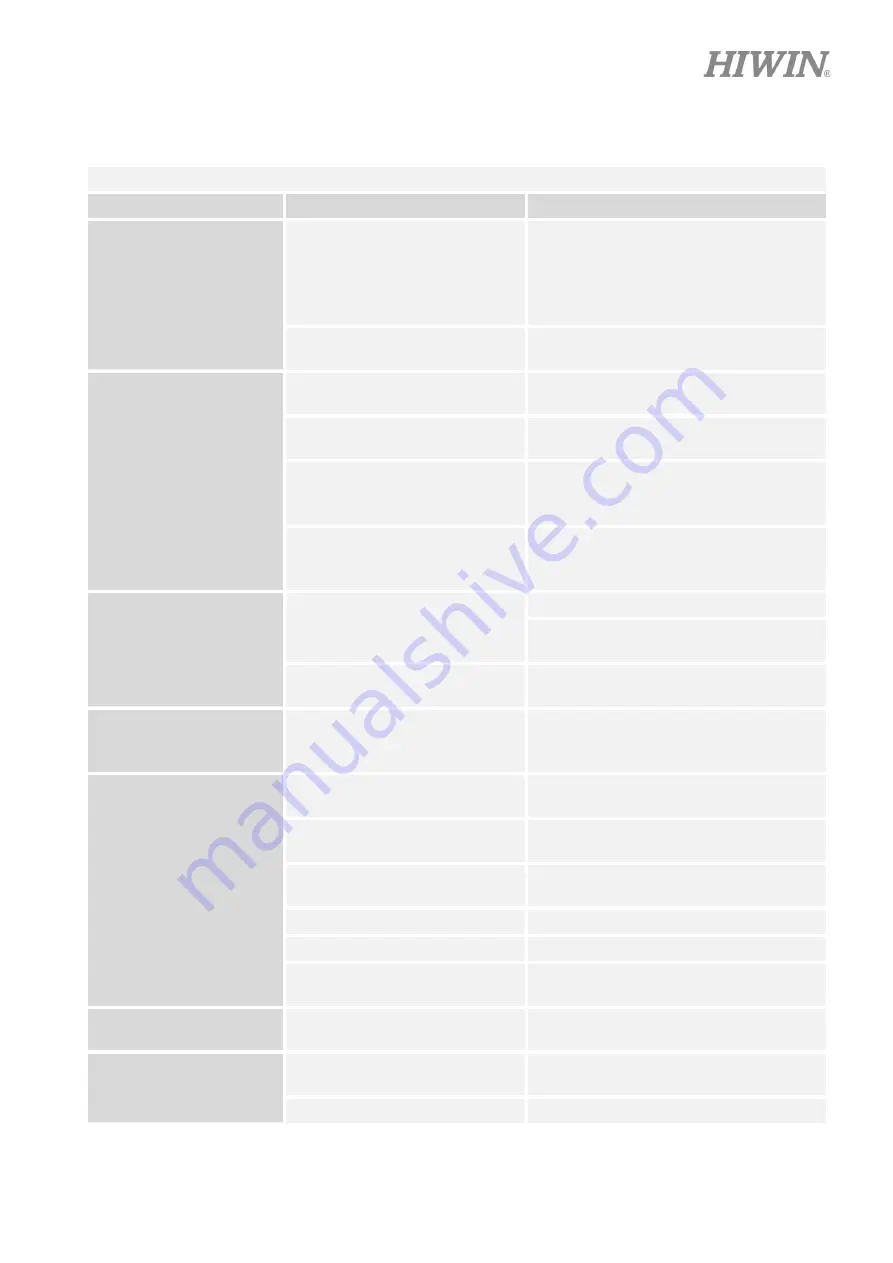
25
MM06UE01-2002
8. Troubleshooting
Table 8.1
Fault table
Fault
Possible cause
Remedy
Motor does not start
Supply lines disconnected
Check connections, plug contacts may be
compressed, repair if necessary.
The connectors have seals, which means
that a certain screw connection resistance
must be overcome.
Fuse has tripped via motor
protection
Check motor protection for the right settings,
remedy defects if necessary
Upon restart, the drive
reports a fault during
commutation
Motor phases connected
incorrectly
Check rotational direction
Encoder counting direction
incorrect
Change the sin and cos pair of wires in the
encoder plug
forcer housing is too close to the
limit switch/limit stop
Disconnect power supply to axis and move
forcer housing manually into the center of
the axis.
Additional drive resistance e.g.
sealing lip, without parameter
adjustment
Change parameters in the drive amplifier
Axis overspeeds upon
restart
Commutation incorrect
See fault during commutation
Check commutation parameters in the drive,
activate speed monitoring!
EMC interference with the encoder
signal
Check the shielding of the connectors and
cables
Axis overspeeds in
positioning mode
Programming error in the position
transfer, invalid acceleration
ordered
Activate security settings in the drive
amplifier, such as speed monitoring,
permissible position errors etc.
Motor heats up too much
(measure temperature)
Rated power exceeded as duty
cycle is too long
Adapt load cycle to the rated power of the
motor
Cooling insufficient
Rectify cooling air supply or open cooling air
passages, retrofit external fan if necessary
forcer housing is difficult to move
Check lubrication of the guideways, foreign
bodies in the traversing range?
Ambient temperature too high
Observe permissible temperature range
Load cycle has been modified
Calculate load cycle and adapt accordingly
Drive amplifier motor commutation
does not function properly
Adapt commutation parameters of the drive
amplifier
Operating noise from the
forcer
Relubrication required otherwise
risk of bearing damage
Lubrication or consultation with HIWIN
MIKROSYSTEM
The axis generates cracking
noises when it is subject to
control
EMC interference in the encoder
signal
Encoder cables must be used separately
with shielded sin and cos signal pairs
Commutation incorrect
Optimize commutation parameters.