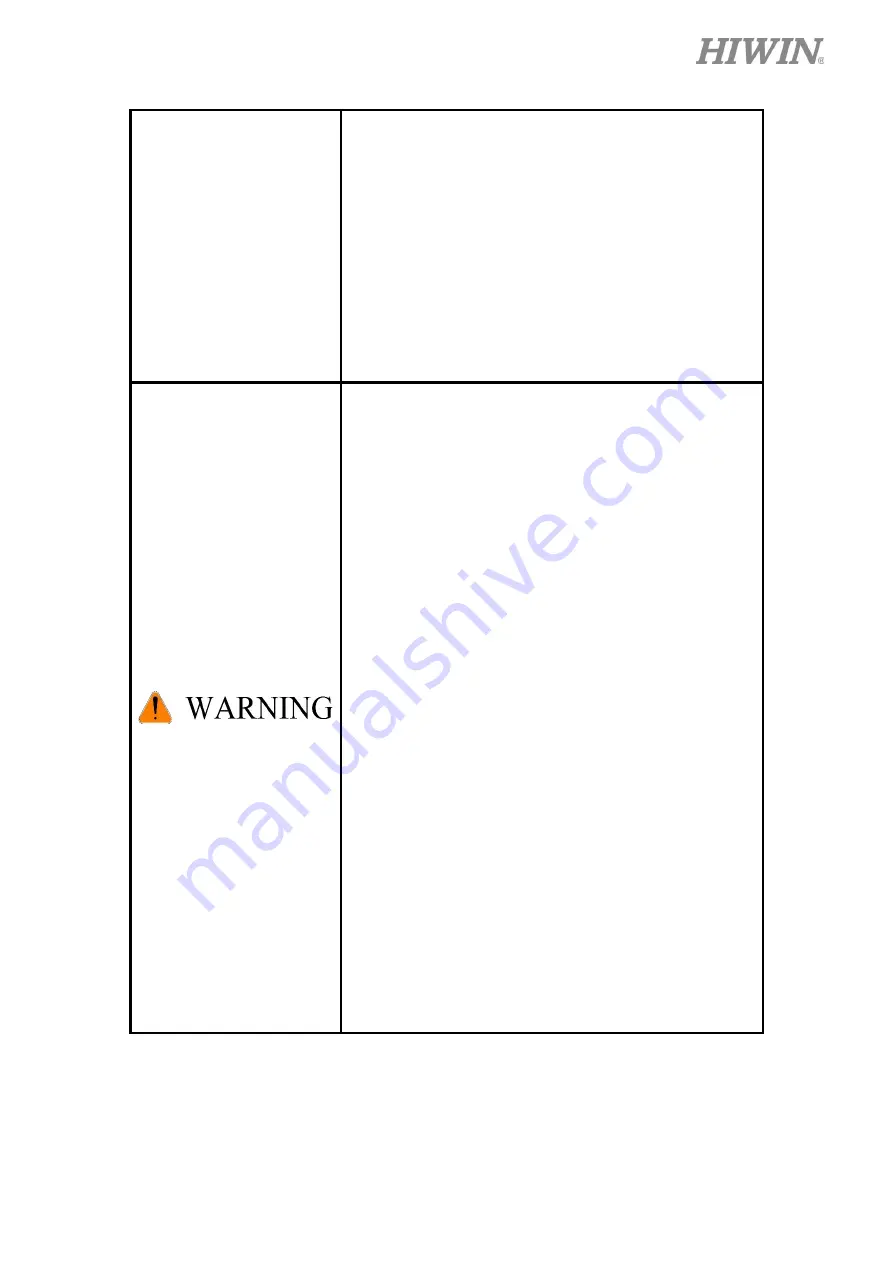
13
C23UE004-2109
The emergency stop button must be installed in an
easily accessible location for quick stop.
While executing an emergency stop, power to the
servo motor will be cut, and all movements will be
stopped. And the control system will be shut down.
Emergency stop should be reset if the restoration
of operating procedure is wanted.
Avoid using emergency stop to replace a normal
stop procedure. This could lead to unnecessary loss
to robot.
The drive power and the control system will be
disconnected to stop all actions during the
emergency stop.
If you want to restart the procedures, you should
reset the emergency stop switch.
Emergency stop established an immediate stop:
Immediately stop the robot system, and
disconnect the driver power.
The emergency stop switch is used for emergency
stop only.
The HIWIN robot is equipped with two emergency
stop switches, where one is installed on the teach
pendant and the other is directly connected to the
controller via a cable. If additional emergency stop
switches are required, other connecting method
can be applied for the same purpose.
Based on the relevant industrial safety regulations,
the emergency stop switch is directly connected to
the controller of the robot via the physical wires.
If the version of the braking is not applied to the
whole axis, once the emergency stop is executed
and the heavy objects are loaded on the robot end,
the axis without brake will move due to gravity.
This attention must be paid for safety issue.
Summary of Contents for RA610-GC
Page 1: ...www hiwin tw User Manual Articulated Robot RA610 GC Original Instruction ...
Page 42: ...40 C23UE004 2109 Figure 2 3 b RA610 1355 GC Outer dimension and motion range ...
Page 43: ...41 C23UE004 2109 Figure 2 3 c RA610 1476 GC Outer dimension and motion range ...
Page 44: ...42 C23UE004 2109 Figure 2 3 d RA610 1672 GC Outer dimension and motion range ...
Page 45: ...43 C23UE004 2109 Figure 2 3 e RA610 1869 GC Outer dimension and motion range ...
Page 47: ...45 C23UE004 2109 Figure 2 4 b RA610 1476 GC Wrist moment diagram ...
Page 48: ...46 C23UE004 2109 Figure 2 4 c RA610 1672 GC Wrist moment diagram ...
Page 49: ...47 C23UE004 2109 Figure 2 4 d RA610 1869 GC Wrist moment diagram ...
Page 50: ...48 C23UE004 2109 Figure 2 4 e RA610 1151 GC Wrist moment diagram mm mm ...
Page 65: ...63 C23UE004 2109 Figure 4 8 Clear encoder by HRSS ...
Page 73: ...71 C23UE004 2109 Table 6 3 Inspection schedule ...