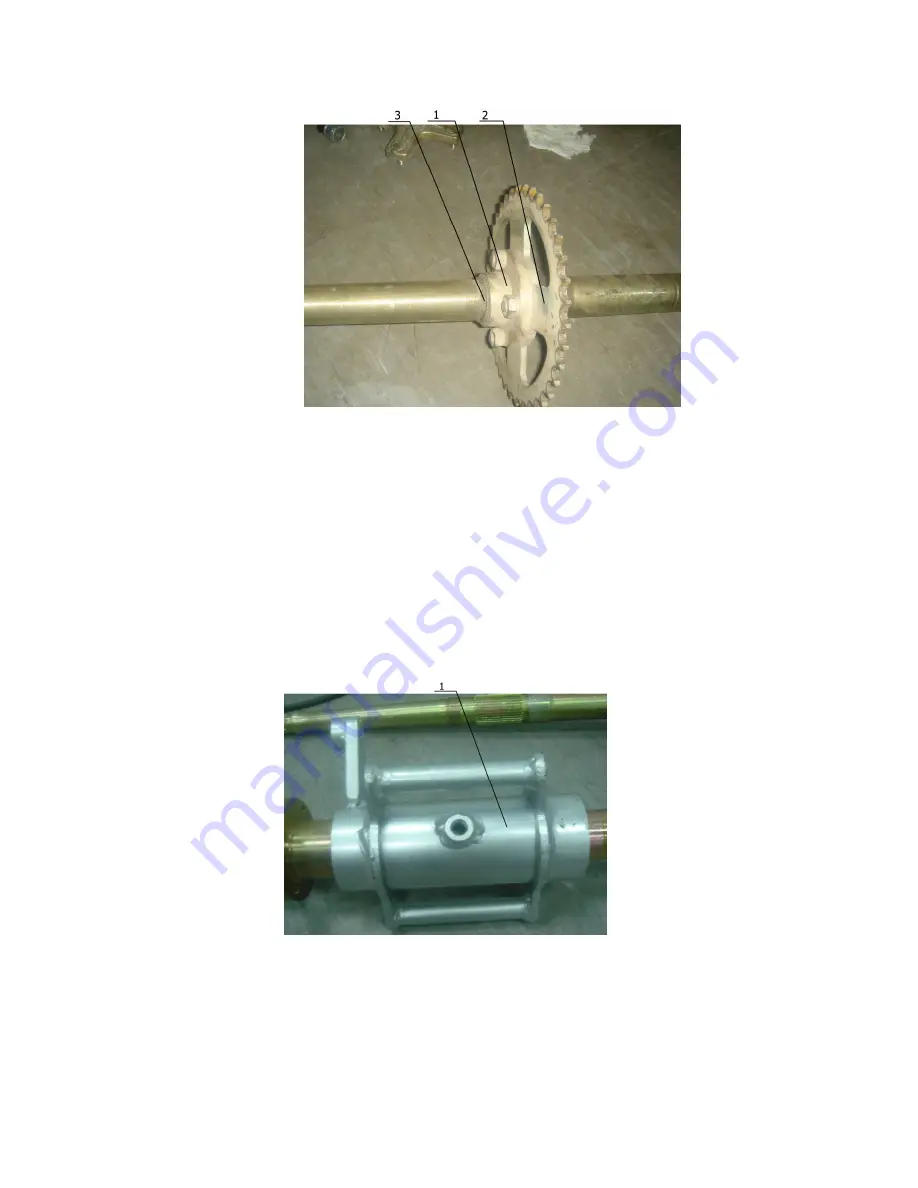
71
Figure 4-4-9
1.
Bottom Seat of Rear Sprocket
2.
Sprocket 3、Circlip
5、Mount Connecting Seat of Rear Bridge onto Rear Wheel
Shaft from the right side and strengthen it by hitting
with plastic hammer. (Figure 4-4-10)
Figure 4-4-10
1. Connecting Seat of Rear Bridge
6、Mount Bottom Seat of Rear Disk Brake Plate onto the Rear
Summary of Contents for 450ATV-2
Page 1: ...450ATV 2 Maintenance Manual ...
Page 3: ......
Page 10: ...10 4 1 Steering system Structure of Steering Vertical Column Components of Steering Bar ...
Page 11: ...11 4 1 1 Disassembly inspection and assembly of Steering System ...
Page 59: ...59 1 Height no less than 3mm 2 profile depth Figure 4 3 4 4 4 Transmission System Rear Bridge ...
Page 76: ...76 Pan Fork ...
Page 77: ...77 4 6 1 Disassembly Maintenace and Assembly of Front Suspension ...