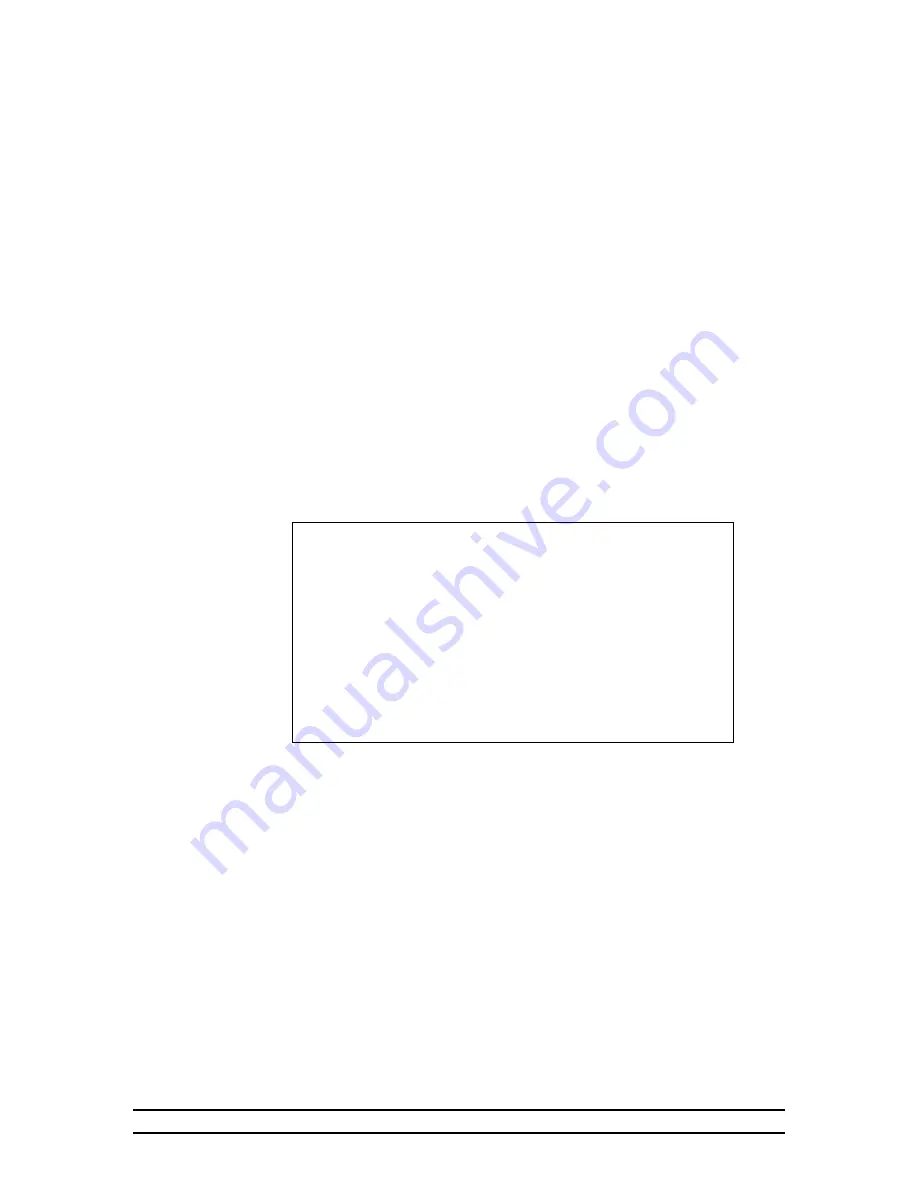
Integrated Control System 500
18
7. Operation
7.1. Curtain Operation
7.1.1. Standard
If the controller sees that temperature inside the house is above target temperature it will
signal the curtains to open. When the cycle time has elapsed the controller will begin
opening the curtain. (The curtain will move for the time set by the Runtime Adjust
setting.) If temperature cannot be maintained by the curtains alone, the controller will
stage in fans as directed by the stage program.
7.1.2. Tunnel (Enhanced Version Only)
When outside temperature has risen above the Outside Sensor Control High Limit
setting, the controller will go into “tunnel mode”. When this event occurs, the controller
will begin shutting the primary curtain while opening the tunnel inlet curtain.
During the time the curtains are re-aligning, the controller is waiting to see the signal
that the tunnel inlet curtain has opened, and that the primary curtain has closed. This
waiting period is counted down in the display. If the controller has waited for 300
seconds (5 minutes) and the inlet curtain has not moved, the controller will “abort” the
attempt to enter tunnel mode. The next paragraph explains this “tunnel mode abort.”
"Tunnel mode abort"
is designed to prevent having a closed house
with no cool stages active. The primary curtain is immediately lowered
to completely open, and the inlet curtain is actuated open. All cool
stages are activated except for stage 8 (which depending on the
program could be a fogger).
You will be alerted to this condition by the continual flashing of the
TARGET and OSC HIGH LIMIT lights.
The machine will not return to normal operation until you reset it by
turning the OSC HIGH LIMIT dial all the way to the left, and then all
the way back to the right within 1 second. At this point the inlet
curtain is closed once again, emergency stages are cut off, and normal
operation is resumed.
Once the primary curtain is closed, (the inlet should be fully open) the controller will
turn on the appropriate tunnel stages. While in tunnel mode, the controller will always
have at least one tunnel stage on.
When outside temperature drops back down to a safe temperature for conventional
ventilation (factory set at 7 degrees below the OSC high limit temperature you set) the
controller will re-align the curtains for natural ventilation. Since it is safe to believe that
this temperature will still be above target temperature, the controller will always open
the primary curtain completely upon exiting tunnel mode. If the curtains need to close,
they will do so when their cycle time begins again.
If the controller begins to enter tunnel mode by adjusting the controls on the facepad,
(By turning the OSC limit dial) the “OSC” light will flash repeatedly for several
seconds, to alert you to this condition. If this was done by accident, you will be able to
stop tunnel mode by re-adjusting the OSC high limit dial.
The inlet curtain will either be completely open or completely closed at all times--no
cycling or running.
Summary of Contents for ICS-500
Page 13: ...Integrated Control System 500 11...
Page 14: ...Integrated Control System 500 12...
Page 15: ...Integrated Control System 500 13...
Page 18: ...Integrated Control System 500 16...
Page 23: ...Integrated Control System 500 21...
Page 24: ...Integrated Control System 500 22...
Page 25: ...Integrated Control System 500 23...
Page 31: ...Integrated Control System 500 29...