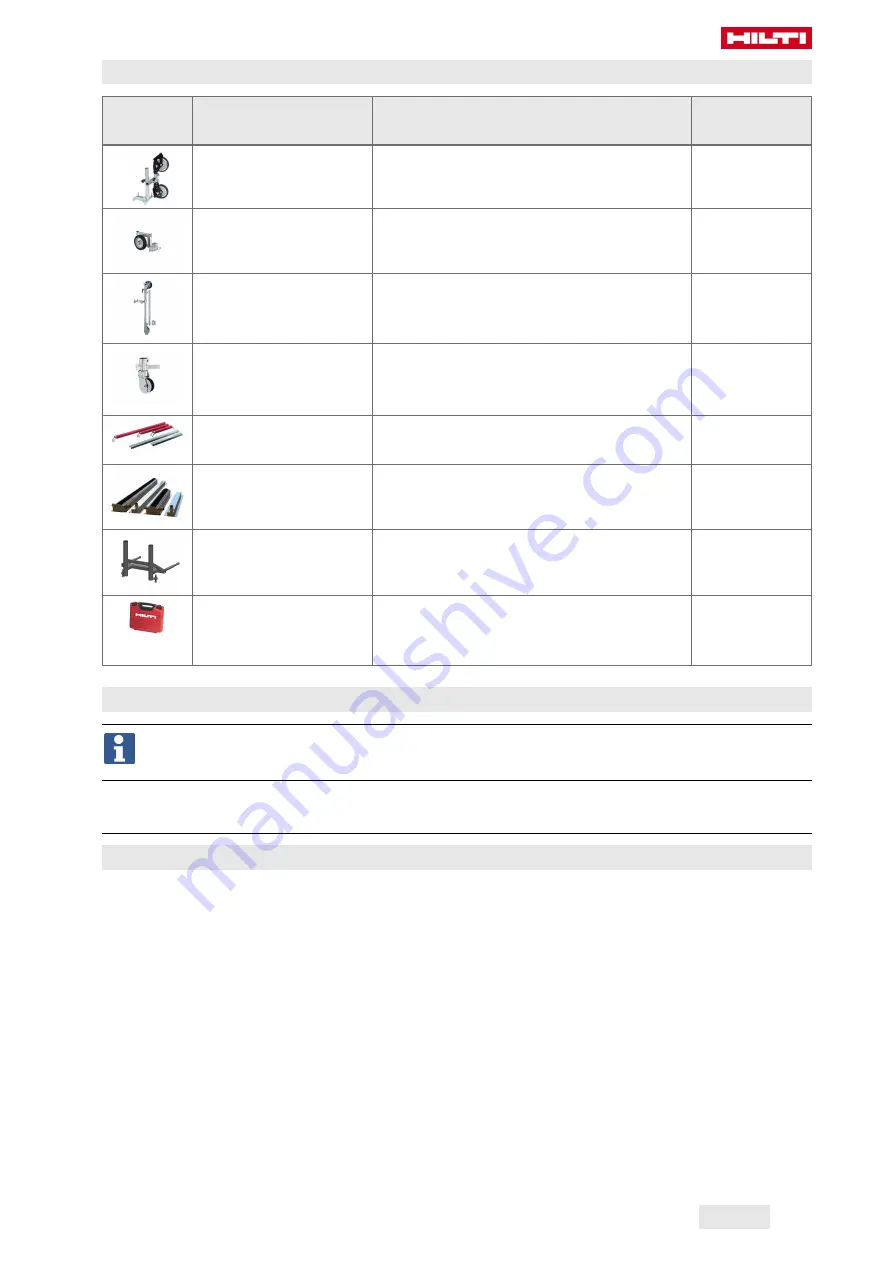
*2238935*
2238935
English
17
5.2 Accessories for diamond wire saws
Acces-
sories
Designation
Description
Material
number
Single-pulley stand
DSW-SPP
Guides the diamond wire from the
drive unit to the structure to be cut.
2205152
Release pulley
DS-WSRW
At the start of a new cut, reduces
friction at the edges.
315834
Plunge wheel
DSW-PW
Permits a plunging initial cut (plunge
cut) whenever there is no access to
the rear of the structure.
365428
Plunge wheel
(pivoting)
DSW-PW
Permits cutting of the bottom, final
section after cutting with the plunge
wheel.
247620
Guards
DSW-WG 250
Reduces the risk of injury at exposed
runs of the diamond wire.
2205155
Dust cover
DSW-DH 1.1-2.0
Reduces the quantity of dust pro-
duced, for example when dry cutting.
2012573
Vertical-cut rig
DSW-PW1510-CA
Permits cutting of columns and
beams.
2301713
Hilti
tools set
Contains anchor-setting tools and
accessories.
2048470
2048471
(US)
5.3 Accessories and wear parts for the wire saw system
Hilti
approved wear parts and other accessories for your product can be found in
your local
Hilti Store
or at:
www.hilti.group
6
Preparations at the workplace
6.1 Planning and safety
6.1.1 Planning the cuts to be made
Ask the site engineer or architect for confirmation of the exact position of the cuts to be
made and make sure that any pipes, conduits or tensioning cables etc. that are to be cut
through do not present any risks or hazards.
Bear in mind that the parts cut away might have to be divided into smaller, more easily
manageable sections for removal and transport (i.e. on account of permissible floor
loads, loading capacity of lifting equipment, size of door openings, etc.).
6.1.2 Planning wire guidance and sequence of cuts
Thorough training and experience are the most important prerequisites for optimum
planning of the sequence of cuts and wire guidance system.
Do not exceed the system’s performance rating when planning the length of the cut. Avoid
cutting in a very flat arc (slow rate of progress) and in over-tightly radiused arcs and do not
try to turn the diamond wire at a sharp angle (possibility of damaging the diamond wire).
Summary of Contents for DSW 1510-CA
Page 1: ...DSW 1510 CA English...
Page 2: ......
Page 3: ...DSW 1510 CA Original operating instructions...
Page 4: ......
Page 45: ......
Page 46: ......
Page 47: ......
Page 48: ...Hilti registered trademark of Hilti Corp Schaan 20210317 2238935 2238935...