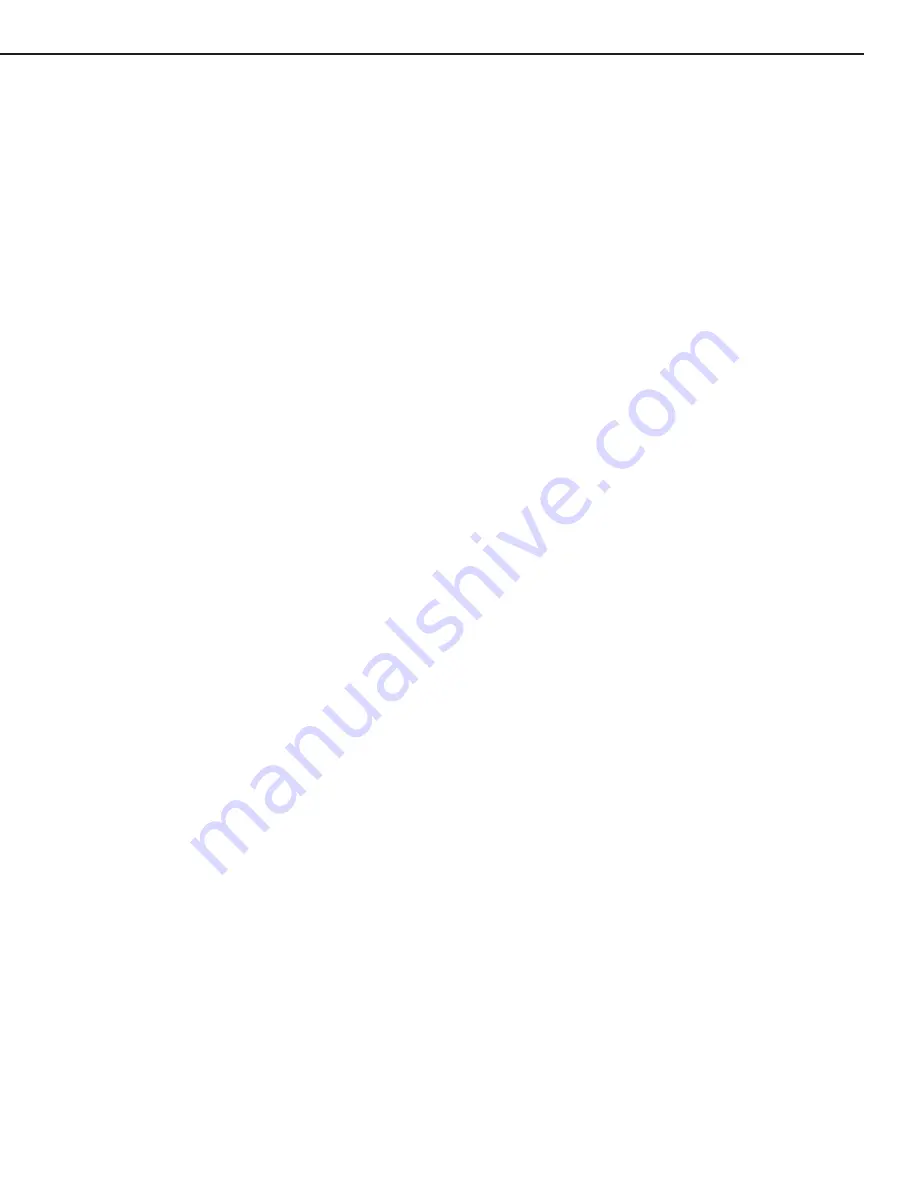
52
AdaptaPAK® Maintenance and Troubleshooting
Air-Cooled Condensing Units
A number of checks should be performed at the intervals listed below.
Quarterly
On a quarterly basis visually inspect the unit to:
1. Look for signs of oil stains on interconnection piping and condenser coil. Pay close attention to areas around
solder joints, building penetrations and pipe clamps. Check any suspect areas with an electronic leak detector.
Repair any leaks found and add refrigerant as needed.
2. Check condition of moisture indicator/sightglass in the sight glass, if so equipped. Replace liquid line drier if there
is indication of slight presence of moisture.
3. Check moisture indicator/sightglass for flash gas. If found, check entire system for refrigerant leaks and add
refrigerant as needed after repairing any leaks.
4. Check compressor sightglass (if equipped) for proper oil level.
5. Check condition of condenser. Look for accumulation of dirt and debris (clean as required).
6. Check for unusual noise or vibration. Take corrective action as required.
7. Inspect wiring for signs of wear or discoloration and repair, if needed.
8. Check and tighten flare connections, if necessary.
Semi-Annually
On a semi-annual basis, the following checks should be performed:
1. Repeat all quarterly inspection items.
2. Clean condenser coil and blades
a. Periodic cleaning can be accomplished by using pressurized water and a commercially available foam
coil cleaner. If foam cleaner is used, it should not be an acid based cleaner. Follow label directions for
appropriate use.
b. Rinse until no residue remains.
3. Check operation of condenser fans.
a. Check that each fan rotates freely and quietly. Replace any fan motor that
does not rotate smoothly or
makes excessive noise.
b. Check all fan blade set screws and tighten, as required. Check
all fan
blades for signs of cracks, wear or
stress. Pay close attention to the hub and spider. Replace blades, as required.
Summary of Contents for Adaptapak ADP-M0000-L0032
Page 4: ...4 AdaptaPAK Parallel Refrigeration System ...
Page 20: ...20 AdaptaPAK Parallel Refrigeration System ...
Page 28: ...28 multiMAX Controller for AdaptaPAK ...
Page 66: ......