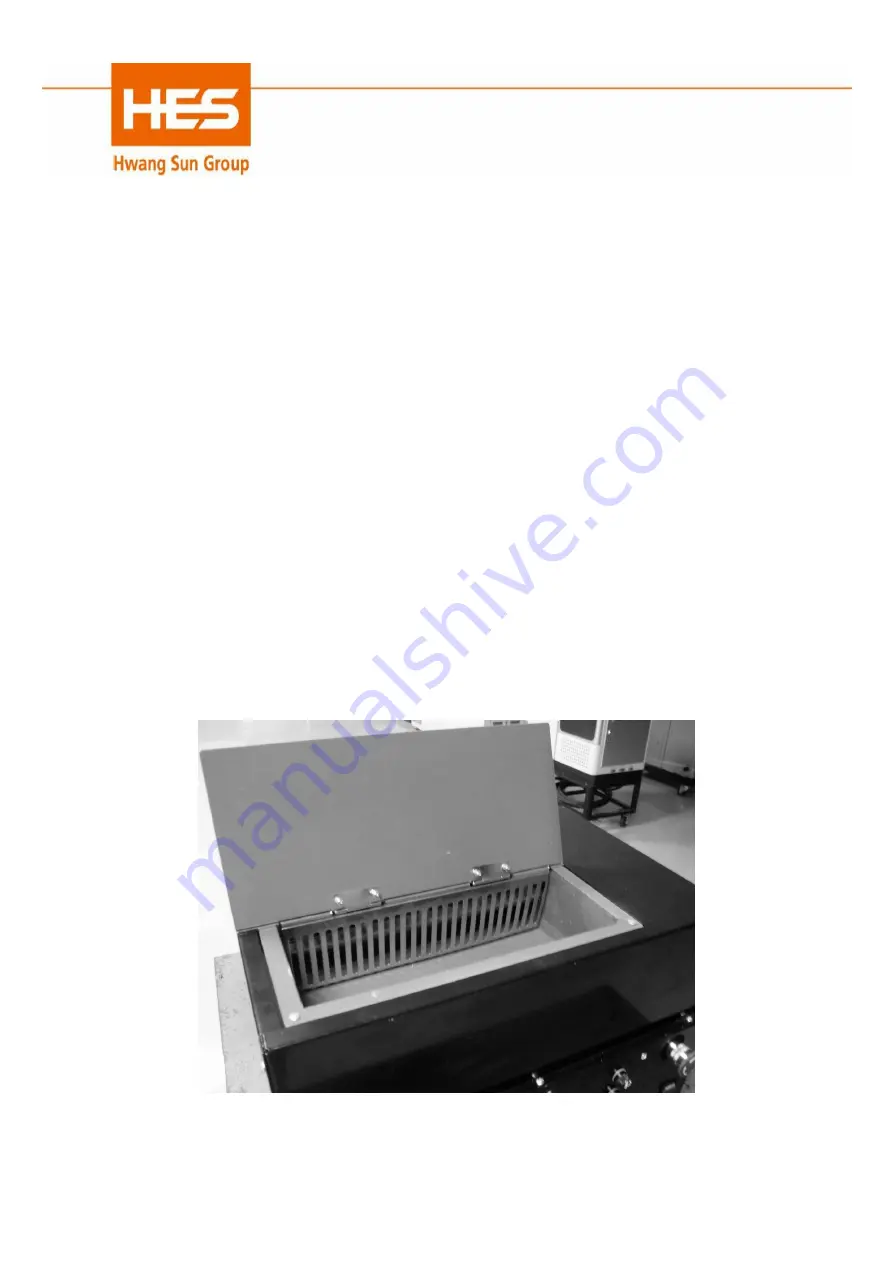
viscosity HMA. The voltage of voltmeter can be adjusted by turning
the resistance that inside side plate.
6) EMERGENCY STOP
Press the
RED BUTTON
would instantly stop motor.
7) FUSE
The fuse would avoid electronic components being burnt.
8) INVERTER
Turn the knob on control panel of inverter to adjust speed of motor.
4-4 PREPARATIONS BEFORE OPERATION
1) Load clean and dry HMA into melting tank. And close tank lid to
avoid some impurities falling into melting tank.
FIGURE 4.2 MELTING TANK
Summary of Contents for HS7003B
Page 1: ......
Page 21: ...CHAPTER 7 DIAGRAMS 7 1 ASSEMBLY DRAWING OF HS7003 B BA ...
Page 24: ...7 2 PLATE ASSEMBLY DRAWING OF HS7003B BA ...
Page 26: ...7 3 DRVING ASSEMBLY DRAWING OF 7003B BA ...
Page 28: ...The fan is blowing from inside to outside 7 4 CIRCUIT OF HS7003B BA ...
Page 29: ...The front of TI3 face to left side 7 5 ELECTRONIC COMPONENTS DRAWING OF HS7003B BA ...