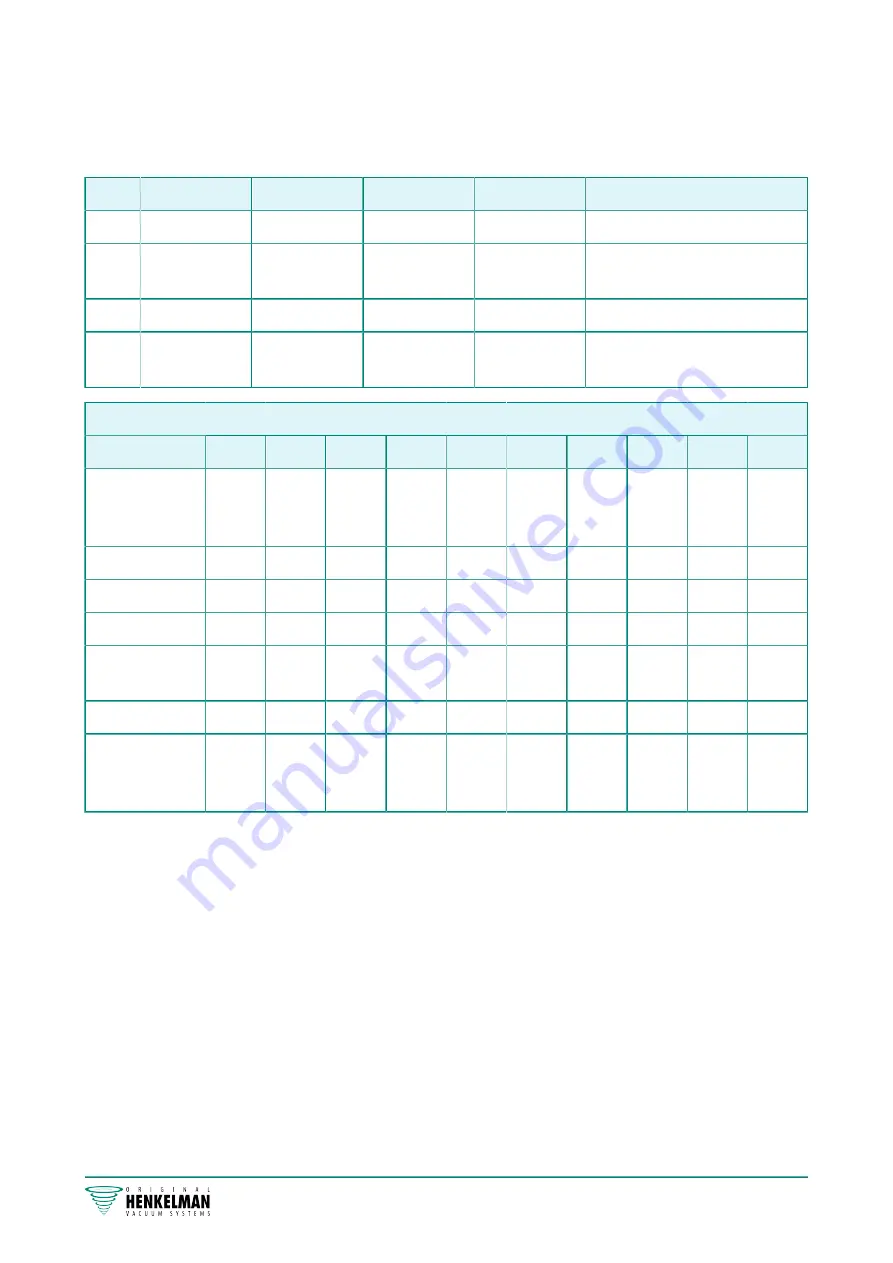
6.2.8 Example programmes
The vacuum packaging machine is equipped with sample programmes with pre-set parameters. It
is possible to optimise a program for your products by modifying the parameters.
Prog
Vacuum
Seal
Soft-air
Type of product
1.
99.8%
OFF
2.2 s
3 s
Solid products
2.
97%
N/A
2.2 s
OFF
Liquids/liquid-con-
taining products
3.
99.8%
OFF
2.2 s
8 s
Fragile/sharp products
4.
99.8%
4 s
2.2 s
3 s
Product that may con-
tain entrapped air
Set as sensor-controlled controlled by Liquid Control sensor (optional)
Prog no.
1
2
3
4
5
6
7
8
9
10
Vacuum
99.8% 99.8%
93% /
99.8%*
90% /
99.8%
**
99.8% 99.8% 99.8% 99.8%
95%
99,8%
OFF
OFF
OFF
OFF
OFF
OFF
OFF
5 s
OFF
Gas (optional)
OFF
OFF
40%
OFF
OFF
OFF
OFF
OFF
OFF
OFF
Seal
2.2 s
2.2 s
2.2 s
2.2 s
2.2 s
2.2 s
2.2 s
2.2 s
2.5 s
OFF
Seal 2 (option-
al)
2.2 s
2.2 s
2.2 s
2.2 s
2.5 s
2.5 s
4.0 s
3.5 s
2.5 s
OFF
Soft-air
OFF
5 s
OFF
OFF
OFF
OFF
OFF
OFF
5 s
OFF
Option on
Red
meat
Mari-
nade
Se-
quen-
tial
Jars
* Vacuum percentage when the gas option is enabled.
** Vacuum percentage when the liquid control sensor is enabled.
Operation 50