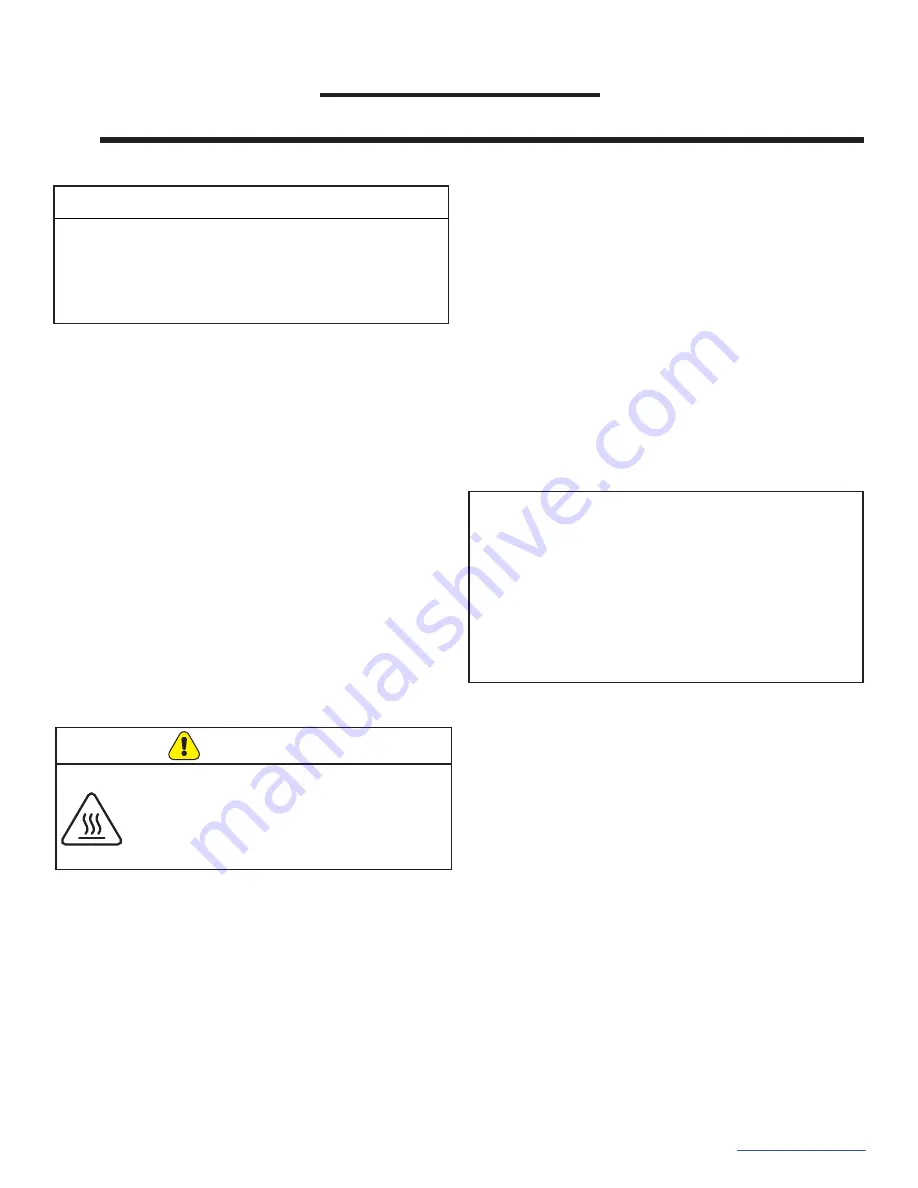
7065-144D • 20 August, 2018
26
Heatilator EcoChoice WINS18
www.heatilator.com
Installer’s Guide
6
Getting Started
A. Design and Installation Considerations
Check building codes prior to installation.
•
Installation MUST comply with local, regional, state
and national codes and regulations.
•
Consult insurance carrier, local building, fire officials
or authorities having jurisdiction about restrictions,
installation inspection, and permits.
CAUTION
Notice:
Hearth & Home Technologies assumes no
responsibility for the improper performance of
the appliance system caused by:
•
Inadequate draft due to environmental conditions
• Down drafts
• Tight sealing construction of the structure
• Mechanical exhausting devices
•
Over drafting caused by excessive chimney heights
•
Ideal performance is with height of chimney between
14-16 feet (4.26-4.88m) measured from the base of
the appliance.
WARNING
Asphyxiation Risk.
•
Do NOT connect this appliance to a
chimney flue servicing another appliance.
•
Do NOT connect to any air distribution duct
or system.
May allow flue gases to enter the house.
Heatilator wood inserts are designed for factory-built
non-combustible fireplaces that have been installed in
accordance with the National, Provincial, State and local
building codes.
1. Prior to installing the wood insert:
• Have the chimney and adjacent structure inspected
and cleaned by qualified professionals. Heart & Home
Technologies recommends that NFI or CSIA certified
professionals, or technicians under the direction of
certified professionals, conduct a minimum of a NFPA
211 Level 2 inspection of the chimney.
•
Replace component parts of the chimney and fireplace
as specified by the professionals.
• Ensure all joints are properly engaged and the chimney
is properly secured.
2. Prior to installing, determine the following:
• Type of chimney connector to be used
- single wall, 6 inch (152mm) diameter, stainless
steel, or
- double wall, 6 inch (152mm) diameter, stainless
steel
• Consult pages 31 and 32 for clearances to
combustibles
• Power outlet located close by for optional blower
Draft is the pressure difference needed to vent appliances
successfully. When a appliance is drafting successfully, all
combustion byproducts are exiting the home through the
chimney.
Considerations for successful draft include:
• Preventing negative pressure
•
Location of appliance and chimney
To be sure that your appliance burns properly:
• During a low burn, the chimney draft (static pressure)
should be approximately -.04 inch water column (W.C.)
• During a high burn the chimney draft should be
approximately -.10 inch (W.C.)
• Measure the W.C at 6 inches (152mm) above the top
of the appliance after one hour of operation at each
burn setting.
B. Draft
C. Fire Safety
To provide reasonable fire safety, the following should be
given serious consideration:
1.
Install at least one smoke detector on each floor of
your home to ensure your safety. They should be
located away from the heating appliance and close
to the sleeping areas. Follow the smoke detector
manufacturer’s placement and installation instructions,
and be sure to maintain regularly.
2.
A conveniently located Class A fire extinguisher to
contend with small fires resulting from burning embers.
3.
A CO detector should be installed in the room with the
appliance.
4. A practiced evacuation plan, consisting of at least two
escape routes.
5.
A plan to deal with a chimney fire as follows:
In the event of a chimney fire:
a. Evacuate the house immediately
b.
Notify fire department.