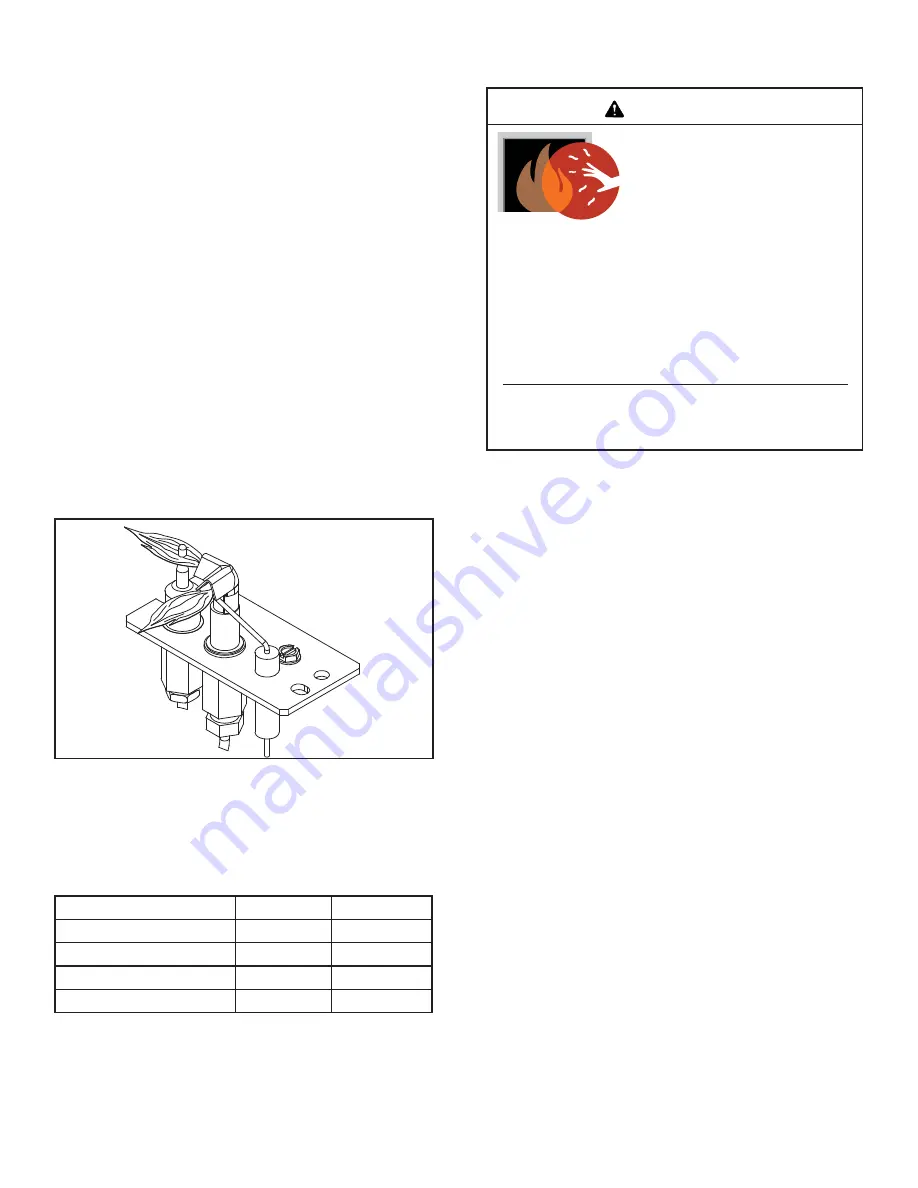
25
Heat & Glo • 6000TRSI-AUC • 2078-900 Rev. Q • 6/10
H. Installer Testing
The space heater must be tested and be operating accord-
ing to manufacturers specifi cations prior to the installer
leaving the site. Note: the tips of the fl ames should never hit
the top of the fi rebox after the unit has warmed up. Please
contact your dealer or a qualifi ed service person to replace
injector or adjust valve.
Upon completing the gas line connection, a small amount
of air will be in the lines. When fi rst lighting the pilot light,
it will take a few minutes for the lines to purge themselves
of this air. Once the purging is complete, the pilot and
burner will light and operate as indicated in the Lighting
Instructions.
Subsequent lightings of the appliance will not require such
purging.
Follow the Safety Information and Lighting Instructions
pages of this manual to light the appliance.
To obtain proper operation, it is imperative that the pilot
and main burner fl ame characteristics are steady, not lift-
ing or fl oating. Typically, the top 3/8 inch (9.5 mm) of the
thermocouple should be engulfed in the pilot fl ame. (See
Figure 1.35). See Table 1 for pressure requirements.
Figure 1.35
Pilot Assembly
This appliance is a balanced fl ue heater and is designed
to operate with all combustion air being siphoned from the
outside of the building and all exhaust gases expelled to
the outside of the building.
WARNING: THIS UNIT IS NOT FOR USE WITH SOLID
FUEL.
The control system for this model employs an electronic
pilot ignition. It consists of a 6V gas control valve/variable
regulator, an electronic module, a thermocouple and a
remote control. The controls are located in the lower com-
partment behind the lower door, and access is gained by
lifting the door up. See Figure 1.
WARNING: DO NOT CONNECT 220-240 VAC TO THE
GAS CONTROL VALVE OR CONTROL WIRING SYSTEM
OF THIS UNIT.
When lit for the fi rst time, the appliance will emit a slight
odor for an hour or two. This is due to paint and lubricants
used in the manufacturing process. Additionally, for the
fi rst few minutes after each lighting, vapor may condense
and fog the glass and the fl ames may be blue. After a
few minutes this moisture will disappear and within 15-30
minutes the fl ames should become yellow.
The heater may produce a noise, caused from metal ex-
pansion and contraction as it heats up and cools down.
This noise is similar to one that a furnace or heat duct may
produce and does not affect the operation or longevity of
the heater.
Table 1.
Follow TROUBLESHOOTING section for adjusting the
appliance to operate properly.
Natural Gas
Propane Gas
Inlet Pressure
1.13 kPa
2.75 kPa
Outlet Pressure
.80 kPa
2.36 kPa
Max. Gas Consumption
36.0 mJ/h
34.0 mJ/h
Burner Injector
2.87 mm
1.70 mm
2.0 OPERATING INSTRUCTIONS
WARNING
This appliance has been supplied with an integral barrier
to prevent direct contact with the fi xed glass panel. DO
NOT operate the appliance with the barrier removed.
HOT SURFACES
!
Glass and other surfaces are hot during
operation AND cool down.
Hot glass will cause burns.
•
DO NOT
touch glass until it is cooled
• NEVER allow children to touch glass
• Keep children away
• CAREFULLY SUPERVISE children in same room as
fi replace.
• Alert children and adults to hazards of high temperatures.
High temperatures may ignite clothing or other
fl ammable materials.
• Keep clothing, furniture, draperies and other fl ammable
materials away.