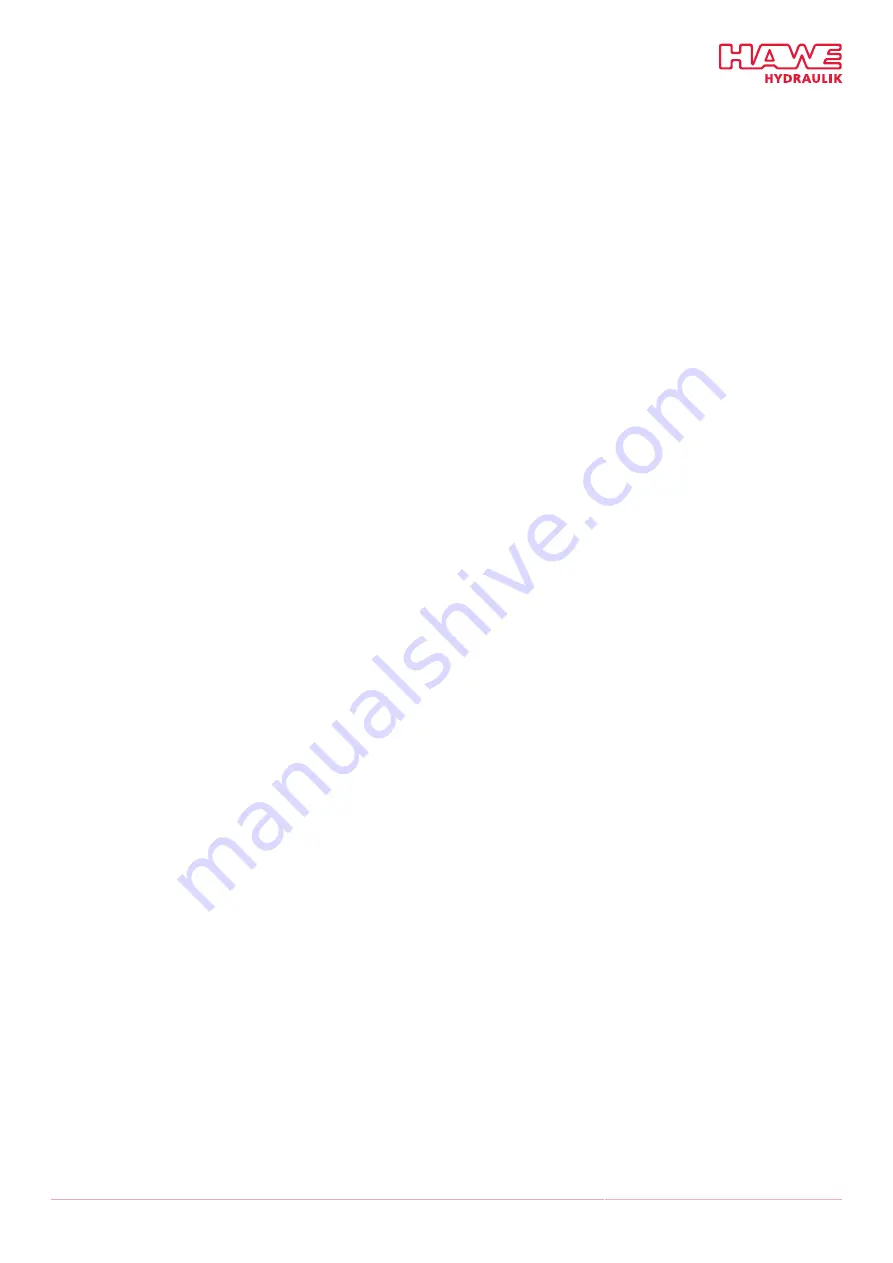
Typical causes for I
DC
■
Consumers that are already attempting to supply power during precharging, e.g. DC/DC converters. In
this case, DS/DC converter power-up needs to be delayed so that it does not supply power until after
precharging has nished (e.g. via ‘enable pin’).
■
Consumers with significant input capacities feature bleeder resistors (discharge resistors) that ensure
input capacities are discharged when switched off. Their resistances are typically within the low kΩ
range. Parallel circuits with multiple consumers will often result in significantly higher I
DC
.
Voltage monitoring
The integral Battery Management System (BMS) monitors the voltage of the battery pack. If this
detects hazardous over-voltage or under-voltage it switches the pack off and outputs a corresponding
error report. It also switches the pack off if pre-dened or customer-specied charging or discharging
conditions are detected. This is part of normal operation and no error report is output. To avoid undue
wear of the relay contacts, the user must however congure his control system so that switching off
under load does not occur in the regular course of events.
Relay monitoring
The status of the HV switch-off (relay) is monitored. This enables detection of any statuses incorrectly
closed (such as relay contacts welded) and statuses incorrectly open (such as a cable break in the relay
supply cable, lack of a vehicle-side safety bridge).
Current monitoring
The integral current sensor (Hall sensor) measures the charging currents and discharging currents within
the system. The values are evaluated in the Battery Management System (BMS).
Temperature monitoring
There are a total of 4 temperature sensors (NTC 10K) within the housing of the battery pack, these
are distributed uniformly within the installation area. The sensors are evaluated by the BMS. If the
temperatures measured lie outside the permitted limit values, the BMS triggers the opening of the main
contactor, thereby preventing the ow of current into the battery or from it.
Integral heater
The battery incorporates an electric heater. When the battery pack is at a low temperature (below 5°C)
this serves to bring the temperature up to a level at which the data sheet species that the cells can be
charged or discharged.
The heater is active in the following modes:
■
Drive
■
Charge
■
Heater request via CAN
As soon as the battery is active (ignition/CAN) the heater is automatically activated by the BMS.
As soon as the lowest temperature that is measured is found to be below 7°C, the heater is switched on.
It remains on until the lowest temperature that is measured reaches 9°C. The heater is also deactivated
if the difference between temperature readings received from the sensors is greater than 9°C.
The heating request via the CAN bus takes no account of the switch-off temperature, so it is the user
who must comply with the above limits. A switch-off is also performed at high differences in tempera-
ture or excess temperature of the overall battery pack. In addition there is a passive switch-off system
fully independent of the electronics. This is triggered if the heater is switched on at a temperature that
is too high. This system is self-resetting, but after its initial activation it changes its characteristics and
becomes "too sensitive".
To restore normal functionality of the heater, there is no other option than servicing the battery pack.
The use of the associated chargers in an under-temperature situation merely compensates the current
consumption of the heater. This allows the battery pack to be "pre-heated” until normal charging can be
performed.
Cell balancing
The Battery Management System (BMS) performs passive cell balancing.
SOC calculation
The Battery Management System (BMS) has an integral SOC calculation. This allows the charge status of
the battery to be read via the CAN bus.
HAWE Hydraulik SE
B 6130 - 02-2022 - 1.0en
13/39