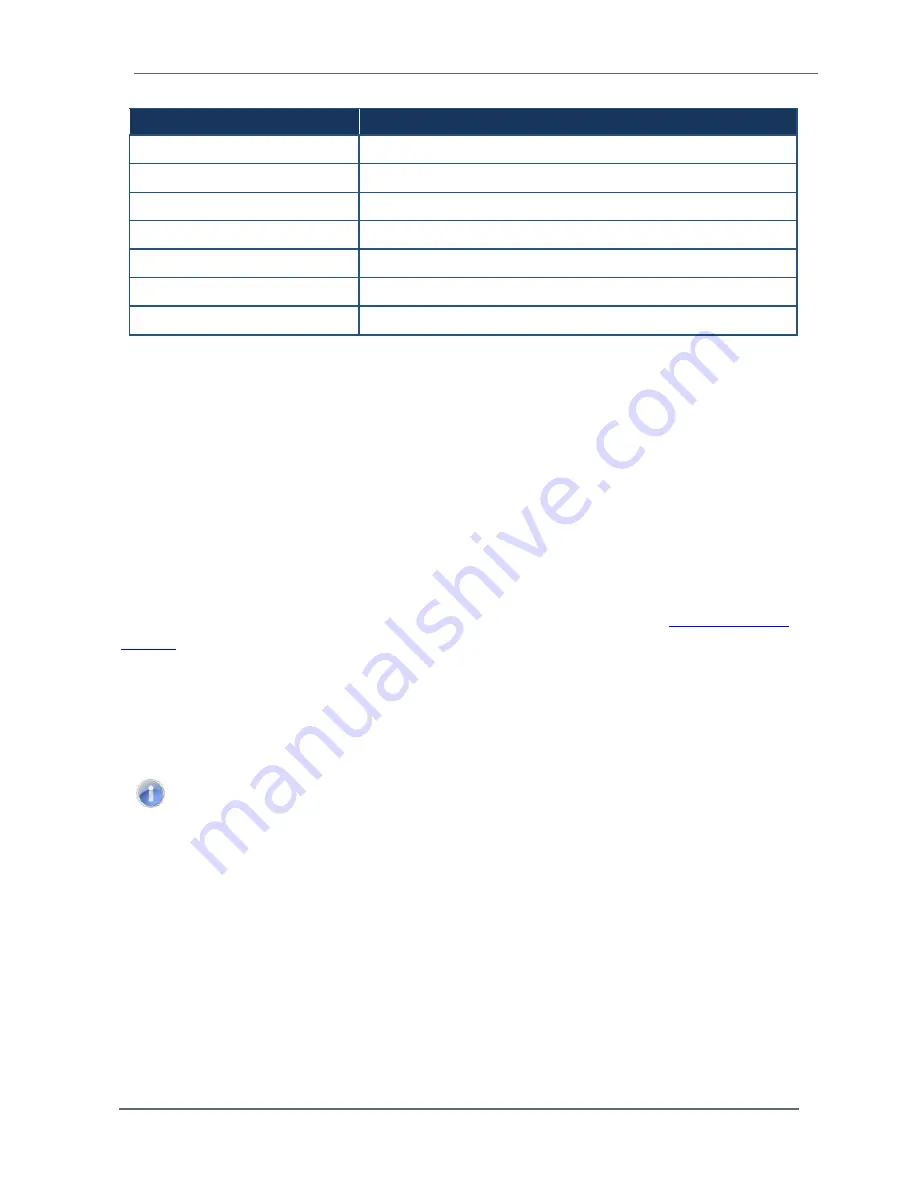
Chapter 4 –
Ways to Set
Scale Parameters
Hardy Process Solutions HI 6200 Weigh Processor User Guide
45
Return Value
Description
6
Fail - C2 capacities not equal
7
Fail - non-Hardy C2 load sensor
8
Fail - not enough counts between Cal low and Cal high weights
11
Fail – param value too high
12
Fail – param value too low
13
Fail – not allowed
128
Fail – Parameter ID not found
4.3.6 Modbus
Modbus is an application-layer messaging protocol that supports client/server
communications between devices connected on different types of buses or networks. All
HI 6200 series units have Modbus TCP built-in. To have the instrument communicate
through Modbus-TCP, use the touch screen or web browser to configure the HI 6200 for
Modbus TCP.
If you do not have a Modbus PLC available to test the Modbus communications, download
the Hardy Modbus-Link client software from the Hardy website to test communications with
the HI 6200 instrument. The package communicates with the HI 6200 only and is not a full
communications package. If you encounter problems with this test, contact
Hardy Customer
Service
.
Modbus services are specified by function codes that are elements of MODBUS
request/reply PDUs. MODBUS is implemented for the HI 6200 using TCP/IP over Ethernet.
In this client/server configuration, the client is the module requesting data and the server is
the module providing the data.
Note:
MODBUS is located at level 7 of the OSI model and accessed at a reserved
system port 502 on the TCP/IP stack. It supports communication with up to 10
different hosts (sockets).
4.3.6.1 Configuring MODBUS
1. Download the Hardy Modbus-Link client software: