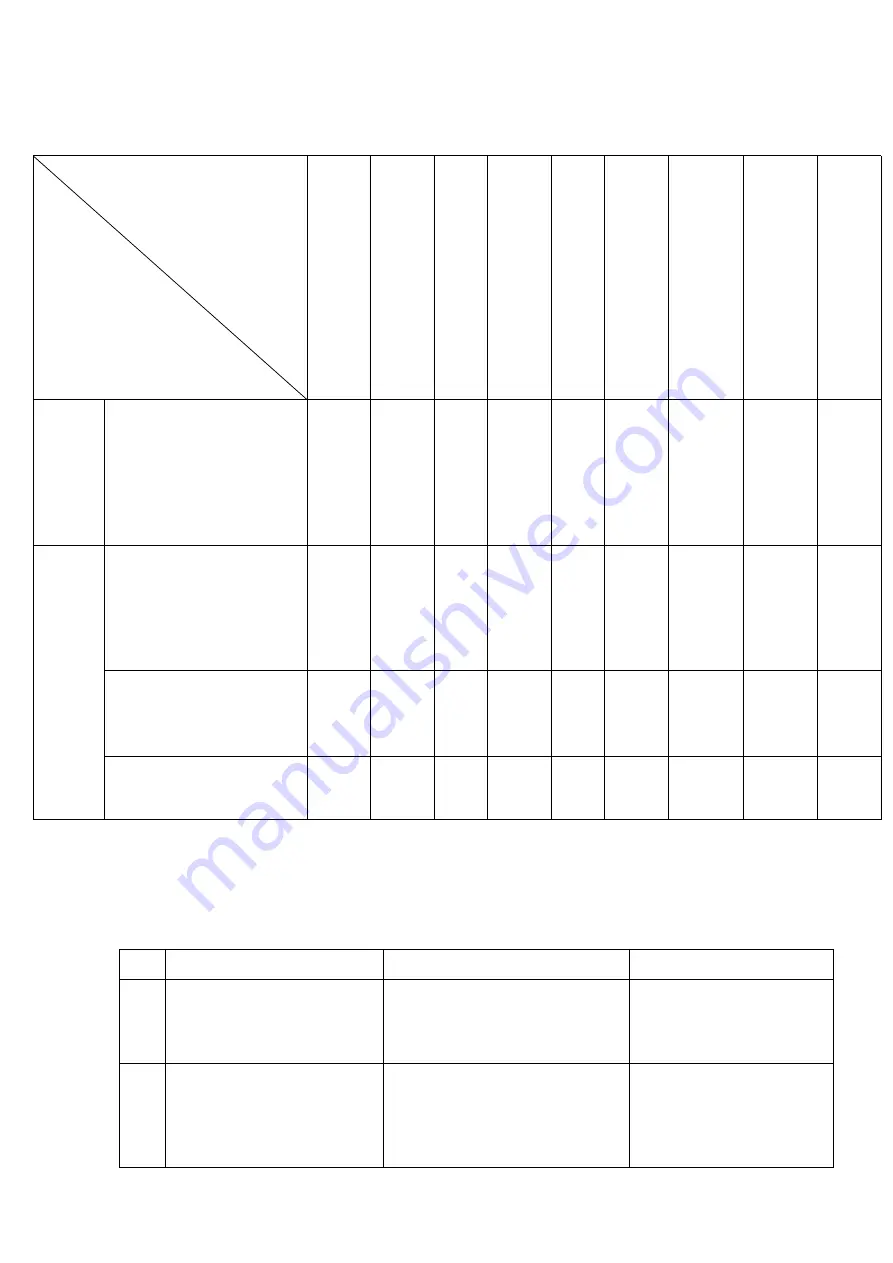
41
Table16
8.3 Common troubleshooting
Table 17
:
NO
Phenomenon
Reason
Method
1
After startup. Light is not
illuminated
1) on the back panel of the
automatic air switch is
damaged
2) power source fuse break
1
)
change it
2
)
change it
2
After connected to power,
Automatic air switch off
the power
1) automatic air switch failure
2) the damage of IGBT module
3) three-phase rectifier bridge
damage
4) welding machine control
replace
Abnormal
Overhaul parts
and repair items
Can not
ignite
the arc
Shield
gas can
not
flow
out
Does
not
send
wire
Igniting
the arc
hardly
Arc is
not
stable
Weld
edge
unclear
Adhesive
base
metal
and
welding
wire
Adhesive
welding
wire and
contact
tip
Appear
gas
hole
Wire
feeder
1) pressure regulating
handle too tight or too
loose
2 nozzle with powder
accumulated
3) the wire feed wheel
abrasion, jam
●
●
●
●
●
torch
1)welding torch cable
bending much
2) contact tip, wire feed
tube adaptability
3) wear, jams,
deformation, etc
●
●
●
●
contact tip, nozzle, the
nozzle joint loose
,
connector joint is not
good
●
●
Welding torch cable,
torch switch control cable
broken
●
●
●
●
●