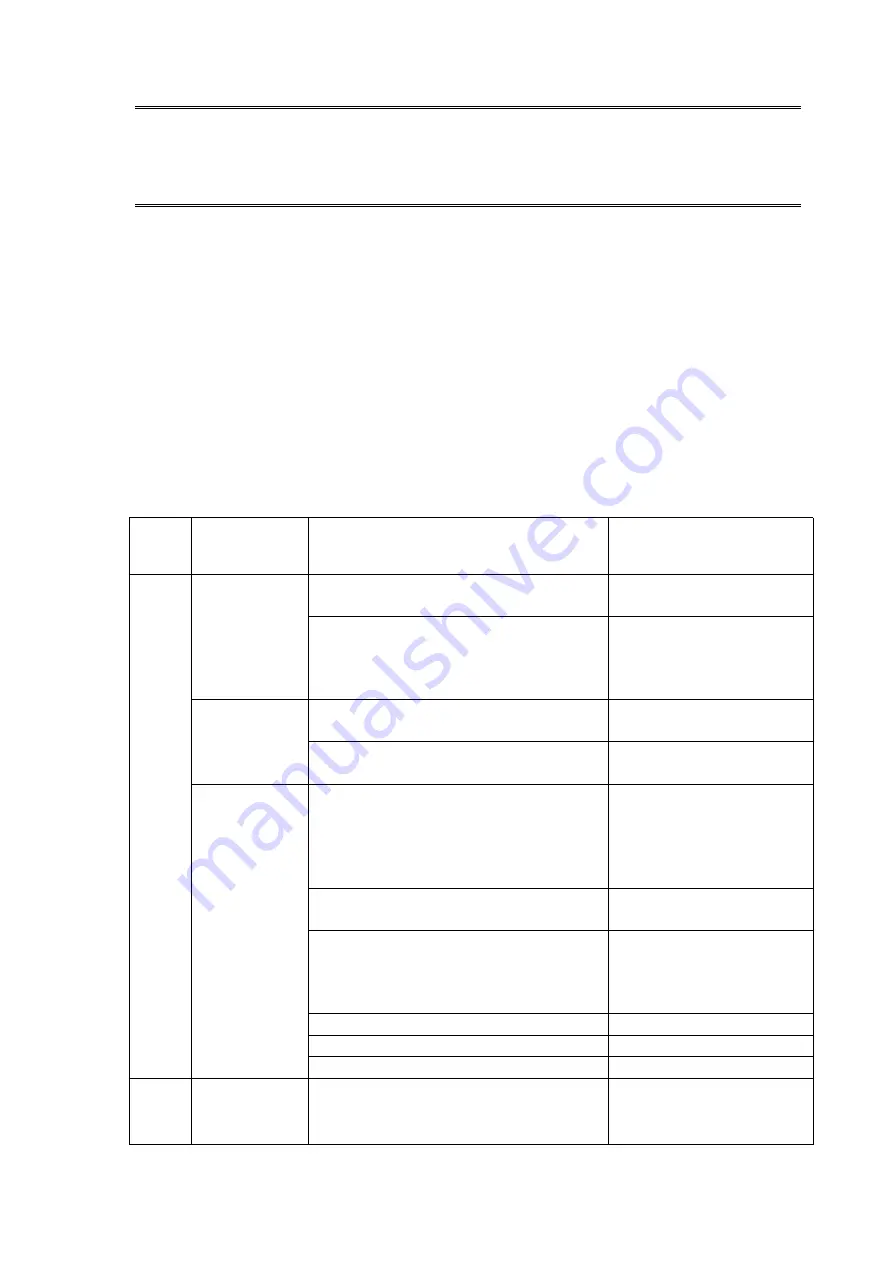
39
●
Please only allow a professional electrician to open the case
●
When carrying out maintenance, please remove the cable from inside the power
distribution box
8.1 welding torch, wire feeding machine maintenance and check
In order to maximize the machine performance and guarantee the safe and normal
operation, daily maintenance and maintenance is very important.
Daily maintenance: Please check welding torch and wire feeder‘s various parts for
any signs of abrasion, deformation, current diverter blockage. If necessary please clean or
replace any parts. To check parts and key points refer to table 15:
Table 15
Parts
For check
The contents for check
reason
torch
nozzle
Whether the installation is firm or
front-end deformation
The causes of gas hole
Whether the splash is adhering
The cause of the welding
torch burning
(effective way is to use a
splash agent)
Contact tip
Whether is installed firmly
The cause of the welding
torch thread damage
End damage, hole wear, congestion
To break the arc or arc
instability
Wire feeding
hose
Wire feeding tube size
Short wire feed tube can
lead to wire feeding
instability (change the
length of the right wire
feeding tube)
if fits the wire diameter and wire
feeding hose diameter
Do not coincide is the
cause unstable arc
Wire feeding tube fouling, wire
coating residue jams
May lead to bad wire
feeding and unstable
arc(renew new wire
feeding hose)
Part bending
Replace new hose
Wire feeding hose breakage
Replace it
O-ring wear
Replace it
Adjust
pressure
handle
overpressure (damage welding wire)
Wire feeding and electric
arc unstable