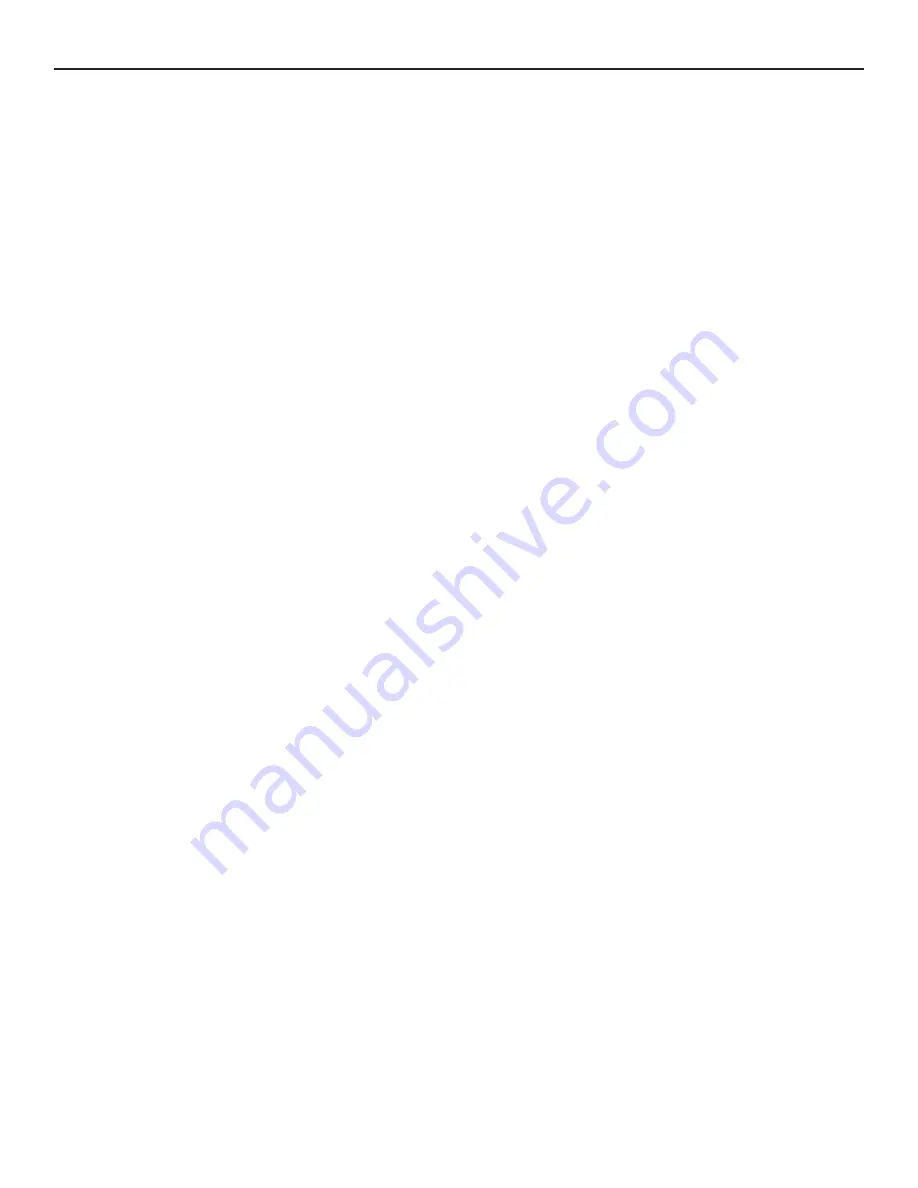
12
APP-001b
APR 2007
SECTION 5 COMPONENT DESCRIPTIONS
WATER BUBBLER
Noncondensible gas from the AUTO-PURGER Plus flows
through the water bubbler where residual ammonia is
absorbed into the water. The water, with absorbed ammonia,
flows to a drain. The water bubbler fill line solenoid valve
(D) opens to automatically replenish water to the bubbler
each time the purge gas solenoid valve (C) energizes. The
water bubbler fill line solenoid valve (D) remains energized
for 30 seconds after the purge gas solenoid valve (C)
de-energizes (float switch magnet pulls in). Large, 1”
(25 mm) diameter bubbles in the water bubbler indicate
proper operation.
The water bubbler flush system consists of the water
bubbler, water bubbler fill line solenoid valve (D), water
check valve, and shut-off valve. Water is automatically
fed to the water bubbler through the water bubbler fill line
solenoid valve (D). Noncondensible gas and water mix,
absorbing residual amounts of ammonia into the water.
The ammonia-laden water is flushed to the water bubbler
drain through the over flow tube. The water bubbler fill
line solenoid valve (D) remains energized an additional
30 seconds after the float switch magnet pulls in. This
fills the water bubbler with fresh water for the next purge
cycle.
LIQUID DRAINER
The liquid drainer separates any liquid condensed in the
purge point piping. This liquid is fed to the low-pressure
liquid return line. Therefore, only foul gas—no liquid—
enters the condensing section of the purger. However,
if too much liquid comes down the foul gas line due to
improper piping, corrective action must be taken.
VAPOR TRAP
The vapor trap separates any vapor that flashes in the
low-pressure pumped liquid line piping. This vapor is fed
to the suction line. Therefore, only liquid—no vapor—flows
through the liquid make-up solenoid valve (B) to the
evaporator chamber of the purger.
CHECK VALVES
There are five check valves on the purger. A 1 psid (.07
bar) check valve with a 1/32” (.8 mm) diameter metering
orifice is installed on the purge gas line to prevent reverse
flow of water into the purger from the water bubbler. A 225
psid (15.5 bar) relief check valve from the float chamber to
suction line. A 1 psid (.07 bar) relief check valve from the
suction line to the float chamber. A 1 psid (.07 bar) check
valve in the water purge line to prevent reverse flow of
water into the purger from the customer supplied container.
The water bubbler fill line has a ½” check valve.
OPERATION OF PURGE GAS ORIFICE
A metering orifice disc is installed inside the 1 psid (0.07
bar) check valve in the purge gas line to the water bubbler.
See Figure 7. This 1/32” (0.8 mm) diameter orifice meters
the noncondensible gas into the water bubbler to prevent
over or under feeding. The ¼” NPT gauge valve should
be fully open during operation and closed for pump out
or maintenance.
OPERATION OF THE METERING VALVE
The metering valve meters condensed liquid refrigerant
from the high-pressure side of the purger into low-pressure
liquid-return line. The refrigerant is filtered through a
small flanged strainer prior to the metering valve, which
removes any par ticles that might block the orifice.
An indication of proper operation of the metering valve is
a frosted liquid feed line from the float switch chamber
through the solenoid valve, strainer and metering valve
to the low-pressure liquid-return line. If the line is not
frosted when the purger is in COLLECTING AIR AND
WATER mode, then the flow of refrigerant through the line
may be blocked due to dirt in the metering valve, strainer,
or solenoid valve.
The metering valve is set and held in place by a locking
knob. Unlock this knob using the .035” hex key wrench
provided inside the purger control cabinet. To clean the
orifice of the metering valve, fully open the metering
valve to flush out any particles. Then, close the valve and
reopen two turns.
If the line still does not frost, then pump out the purger
and inspect the strainer and metering valve.
PURGE POINT SOLENOID VALVES
For the customer-supplied purge point solenoid valves,
Hansen recommends our HS8A with close-coupled strainer.
This is a 1/2” por t, heavy-duty, pilot-operated solenoid
valve with stainless steel piston. The purge point solenoid
valve must be a minimum of 1/2” port size to avoid excess
pressure drop across the valve.
The standard molded coil is for 115V, (208/230V or 24V are
available). Flange connections available are 1/2”, 3/4”, and
3/8” FPT, socket weld, and weld neck. To order, specify
catalog number HS8AST, required connection style and
size, and volts. Specify DIN plug solenoid connection if
needed.
Models APP08, APP16, and APP24 supply 115VAC to the
purge points regardless of whether 115VAC or 220VAC is
supplied to the control cabinet.