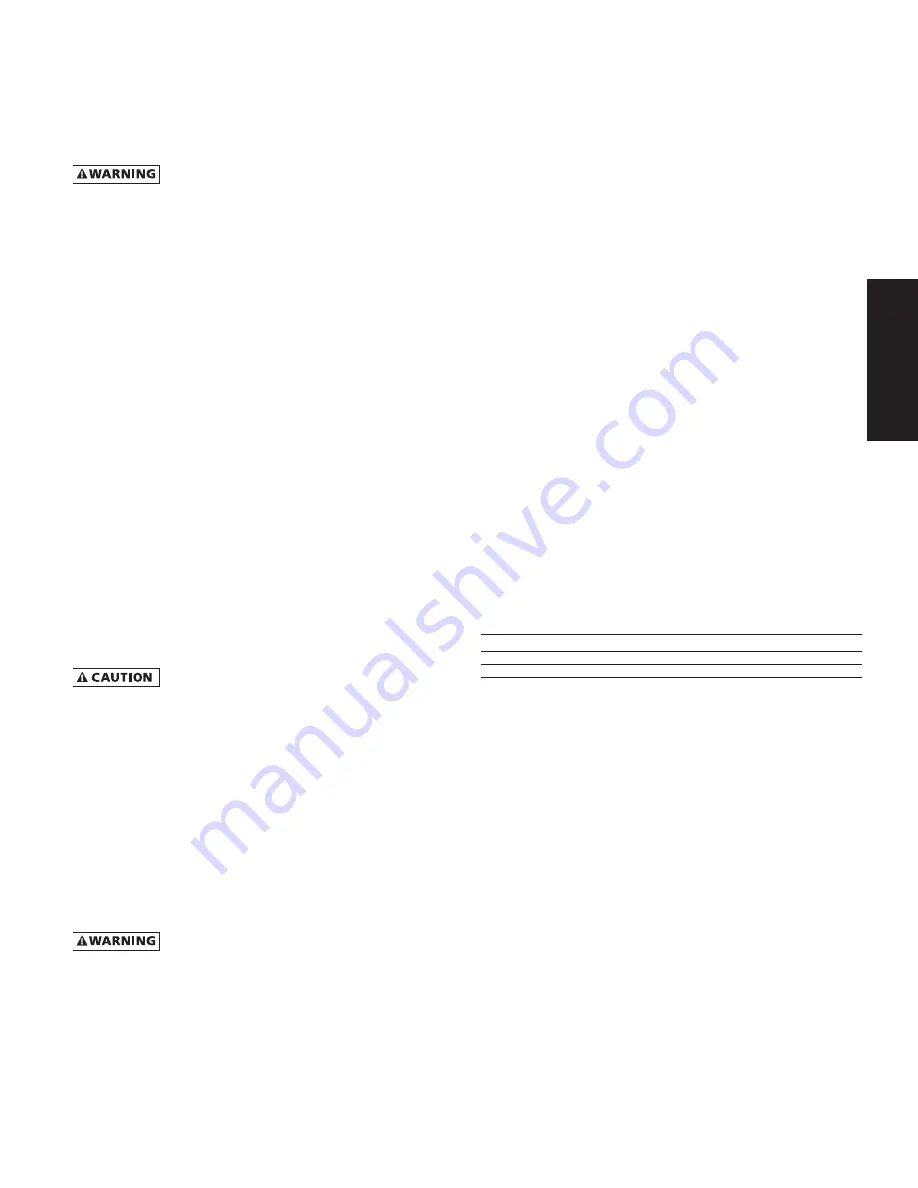
5
MAINTENANCE
The dryers require little maintenance for satisfactory
operation. Good dryer performance can be expected if the
following routine maintenance steps are taken.
Disconnect power supply and depressurize
dryer before performing any maintenance.
General
For continued good performance of your refrigerated dryer,
all refrigeration system maintenance should be performed
by a competent refrigeration mechanic.
NOTE: Before corrective maintenance is done during the
warranty period, call your local distributor and proceed
according to instructions. Refer to the warranty for limits of
your coverage.
Daily Maintenance
Check the separator for condensate discharge. If no
discharge is evident, depressurize, dismantle and perform
the following:
1.
Automatic Float Drain - Clean separator housing with
mild soap and water. Discard drain and replace.
2.
Electric Drain - Clean strainer and/or clean/replace
solenoid valve.
Monthly Maintenance
Inspect the condenser coils. Remove accumulated dust and
dirt with a soft brush or with air from an OSHA approved
compressed air nozzle that limits the discharge pressure to
30 psig.
Electronic Drain Valve Disassembly and Servicing
Do not disassemble drain valve timer or
attempt to repair electrical parts. Replace timer if defective.
The drain valve discharges condensate through a
full-port drain opening. The valve body may need to be
cleaned under conditions of gross particulate contamination.
To disassemble the drain valve body for cleaning and other
maintenance:
1.
Turn power switch off.
2.
Disconnect main power supply to dryer.
3.
Depressurize unit
4.
Lock out and tag power supply in accordance
with OSHA requirements.
If power supply is not disconnected and unit
is not depressurized before disassembly, serious personal
injury and valve damage may result.
5. Remove screw and washer from front of the drain valve.
6. Remove the power supply connector and gasket (with
the timer assembly if attached) from the solenoid coil
housing. Do not damage or lose the gasket.
7. Remove coil fixing nut and spring washer from top
ofsolenoid coil housing.
8. Lift solenoid coil housing off solenoid core in valve body.
9. Unscrew solenoid core from valve body.
Once the drain valve is disassembled, the following
maintenance can be performed.
1.
Inspect internal parts of valve body; clean or replace as
required.
NOTE: Replace solenoid valve if component damage is observed
2.
Remove debris from valve body.
3.
Wipe solenoid core components with a clean cloth or
blow out debris with compressed air from an OSHA-
approved air nozzle that limits its discharge pressure to
30 psig.
4.
Check that the plunger assembly is clean and moves
freely in housing.
5.
If timer is attached to valve body, check electrical
continuity across timer assembly.
To reassemble the drain valve, reverse the sequence of the
preceding steps. After the drain valve is reassembled,
connect the main power supply to the dryer. When the
dryer is returned to service, check the drain valve for air or
condensate leaks; tighten connections as required to correct
leaks. Check the drain cycle; adjust the timer according to
the procedure in the drain valve adjustment section.
Returns to Manufacturer
If the dryer or a component of the dryer must be returned
to the manufacturer, first call your local distributor for a
return authorization number and shipping address. Your
distributor will inform you whether the dryer or only a
component must be returned. Mark the package with the
return authorization number and ship freight prepaid as
directed by your local distributor.
E
N
G
L
I
S
H
Parts List
Item
5-10
15
On/Off Switch
3041494
3041494
Float Drain Kit
3090900
N/A
Timer Drain
N/A
3149293