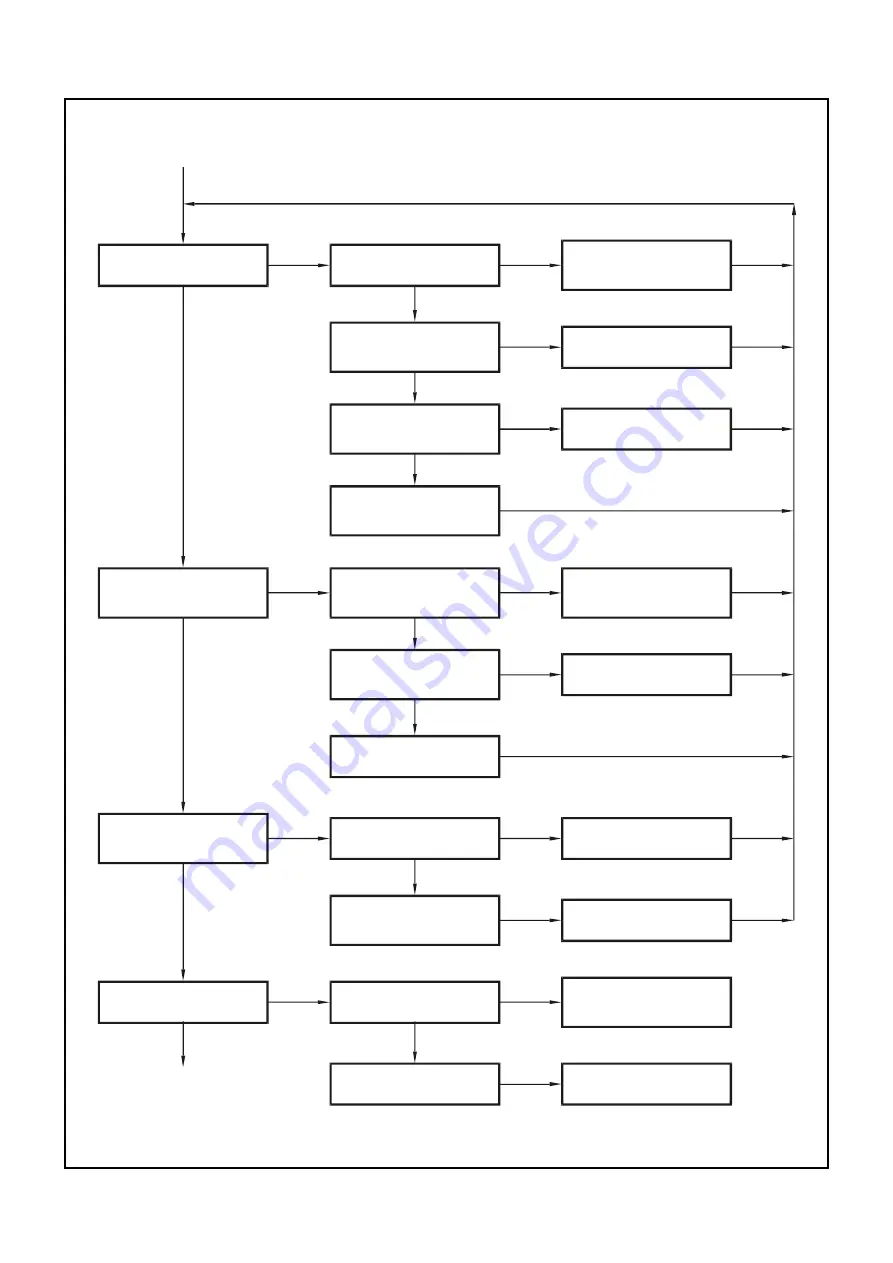
HAMWORTHY HEATING LTD
SHERBORNE
500001103/E
Figure 12.3. Fault Finding Procedures.
Continued from
Fig 12.2
Single boiler modulates
down as temperature rises?
Check temperature sensor
wiring connections, replace
boiler main PCB
Resistance of temperature
sensor approx.1000
at room temperature?
Ù
Rotary switch ‘SW1’ on
boiler main PCB set to
correct position?
Rotary switch ‘SW1’ on
boiler main PCB set to
correct position?
Rotary switch ‘SW1’ on
boiler main PCB set to
correct position?
Temperature control set to
correct temperature?
Refer also to Milton
installation manual
Is the remote high/low
link (R3-R4) closed?
Boiler under remote
high/low sequence control
switches to high fire?
Continued
Ref. Fig 12.4
Insufficient water circulation
Temperature control
circuit faulty
Temperature control set
above Milton control
temperature?
Boiler under Milton sequence
control modulates down as
temperature rises?
Replace temperature
sensor
Check and set rotary switch
to correct position
Check and set rotary switch
to correct position
Check and set rotary switch
to correct position
Check temperature control
knob setting, check control
knob wiring connections
Check and close
remote circuit
Check/replace temperature
sensor and/or boiler
main PCB
Check/replace pump, bleed
trapped air from the system
Boiler cycles on/off
rapidly?
Check temperature control
knob setting, increase
setting if required
No
No
No
No
No
No
No
No
No
No
Yes
Yes
Yes
Yes
Yes
Yes
Yes
Yes
Yes
No
No
Yes
Yes
Yes
32
Summary of Contents for Sherborne S65
Page 8: ...HAMWORTHY HEATING LTD SHERBORNE 500001103 E Figure 1 1 Boiler Installation Typical 2 ...
Page 29: ...HAMWORTHY HEATING LTD SHERBORNE 500001103 E Figure 10 6 Gas Pipe Fitting 23 ...
Page 45: ...HAMWORTHY HEATING LTD SHERBORNE 500001103 E NOTES 39 ...
Page 46: ...HAMWORTHY HEATING LTD SHERBORNE 500001103 E NOTES 40 ...
Page 47: ...Notes ...