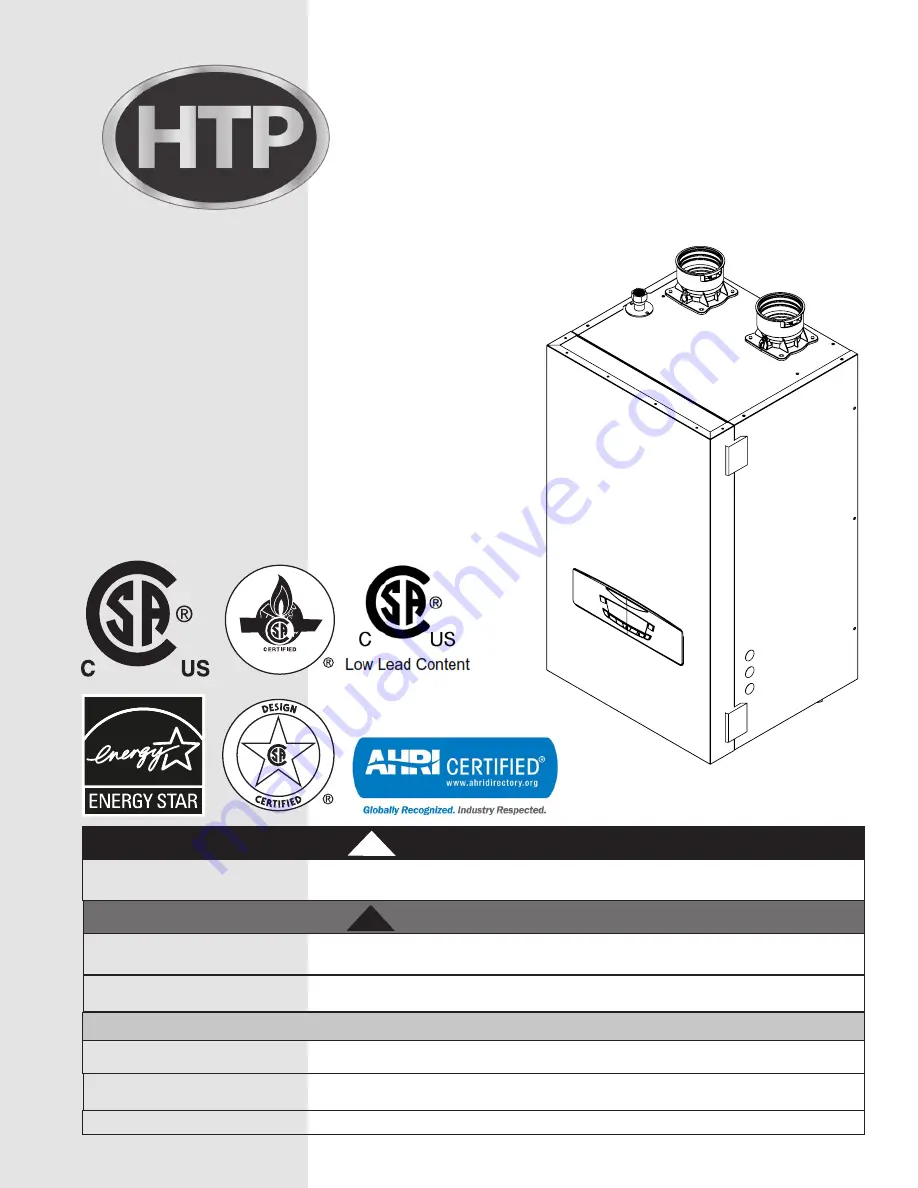
Elite Ultra
TM
High Efficiency Condensing
Wall-Hung Gas Boilers
Installation
Start-Up
Maintenance
Parts
Warranty
ELU-150WBN / ELU-199WBN / ELU-199WCN Models
DANGER
!
This manual must only be used by a qualified installer / service technician. Read all instructions in this manual before installing. Perform steps in the
given order. Failure to do so could result in substantial property damage, severe personal injury, or death.
NOTICE
The manufacturer reserves the right to make product changes or updates without notice and will not be held liable for typographical errors
in literature.
NOTE TO CONSUMER: PLEASE KEEP ALL INSTRUCTIONS FOR FUTURE REFERENCE.
272 Duchaine Blvd.
New Bedford, MA 02745
www.htproducts.com
LP-719 Rev. 000 Rel. 000 Date 6.25.20
WARNING
!
Improper installation, adjustment, alteration, service, or maintenance could void product warranty and cause property damage, severe
personal injury, or death.
California Proposition 65 Warning: This product contains chemicals known to the State of California to cause cancer, birth defects, or other
reproductive harm.
The surfaces of these products contacted by potable (consumable) water contain less than 0.25% lead by weight as required by the Safe
Drinking Water Act, Section 1417.
Heat Exchanger Bears the ASME “H” Stamp