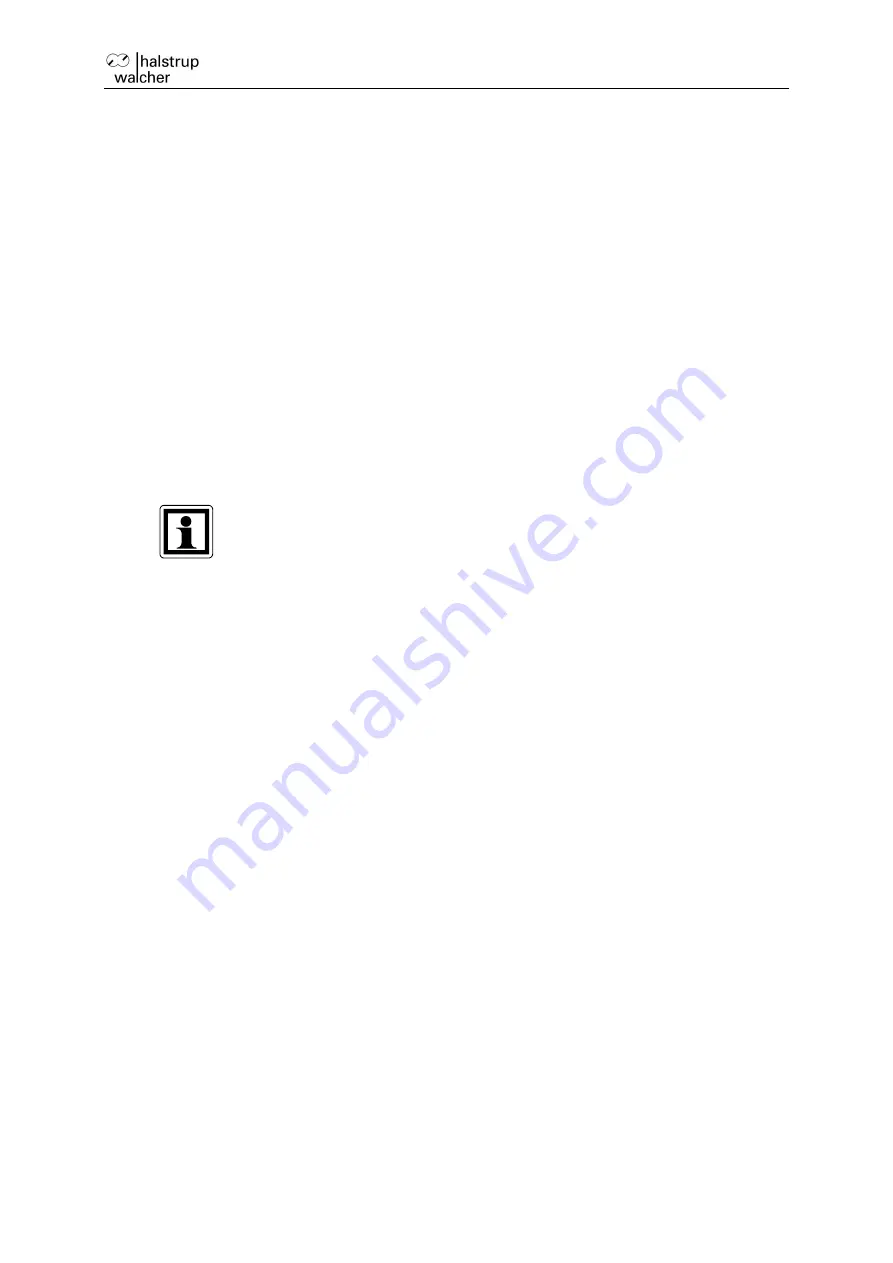
Instruction Manual PSE2xxMod
23
b) Response of drive in case of block or manual displacement
If during a run due to load the speed falls below the threshold parameter of 30% (HR
70) of the selected maximum speed for longer than 200 msec (HR 83), the device
detects blockin
g, aborts the run and sets the ‘positioning error’ bit (here the default
values are given).
New run commands can then be transmitted with no further steps to take. An
exception is, if the run should go to the same target than before. In this case,
deassert the release (bit 4 of the control word) and assert it again, then transfer the
target position one more time.
If the PSE2xxMod is displaced by external force during standstill opposite to the loop
direction and the release bit (bit 4) as well as the release readjustment bit (bit 10) in
the control word are being set, the device will attempt to reach the previously
transmitted target value once again (readjustment). The device does not attempt to
readjust if rotated in the loop
direction; it merely sets the ‘manual rotation’ bit. If bit 6
(“run without loop”) is being set, the drive readjusts the position in both directions.
Deasserting the release and/or the release readjustment bit can completely stop the
readjustment process.
If at standstill the drive continuously looses its position, the attempt to
readjust starts exactly when the actual position is leaving the positioning
window (assumed that all the conditions above are being fulfilled). If the
motor power is missing at the time when this transition happens, the
readjustment fails and bits10 (‘positioning error’) and 13 (‘motor power was
missing
’) will become active. If later the motor power comes back again,
there will be
no
further attempt to readjust. This is to prevent a situation
that suddenly a drive begins to run if motor power is being switched on.
c) Internal measuring system
(applys for “singleturn” variants)
The singleturn variants of the PSE2xxMod actuator include a partial absolute
measuring system. This means that the position within one turn is measured absolute
and the turns are counted.
These ‘counted turns’ are stored in internal flash every time a run has been finished
or if the actual position value changes during standstill. The value is available after
power up without further commands.
There are two cases that cause the counted turns to be invalid:
1) The output shaft is externally displaced during control power off for more than 36°.
2) Control power is turned off while the PSE2xxMod is turning.
In these cases HR 9 has value 0
(“actual position is not consistent”).
Now there are three possible ways to continue depending on the amount of
displacement during control power off:
1) No special actions have to be taken if the displacement has been less than 180°
(½ turn): The actual position value is still correct.
2) If the displacement has been more than 180° (½ turn), the correct actual position
value has to be sent to the PSE2xxMod (by writing to HR 2/3).
3) First move to a reference position, then write the actual position value with HR 2/3
(if the displacement has been more than ½ turn and the actual position is not
available otherwise).