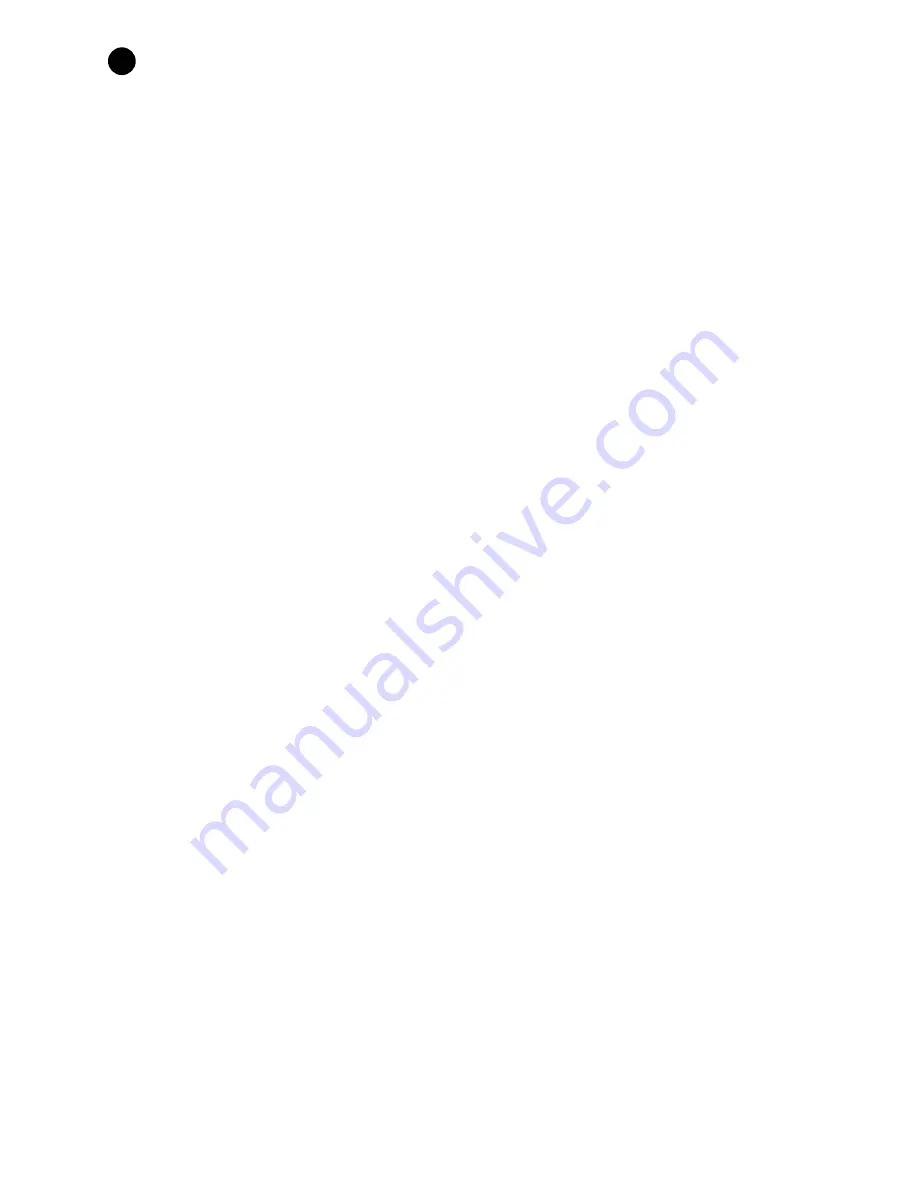
– 15 –
Options
Reduce Static
(on some models).
When selected, the dryer will spray a mist of water onto the load, at the end of the drying
cycle, to reduce static. This option is not available with BULKY, SANITIZE or STEAM cycles.
Damp Alert (Damp Alert/WiFi Pad)
: This option causes the dryer to beep when clothes
have dried to a damp level. Remove items that are wished to hang dry. The Damp Alert
will only beep when this option is selected (but the dry cycle will keep running). Removing
clothes and hanging them when they are damp can reduce the need to iron some items.
Delay Dry
Press the Delay Dry pad to set the delay start time in 1 hour increments up to 24 hours, and
then back to clear (0 hours). After selecting the delay start time, press Start, and the delay
time will count down the time remaining until the cycle starts.
NOTE
: To set the amount of
delay time faster, press and hold the Delay Dry pad.
Delay Dry for Wi-Fi Connected Dryers
There are two options to set Delay Dry using a smartphone.
• Option 1
: Follow Delay Dry instructions. Use the GE Appliances Laundry App to adjust
the amount of time via smartphone.
• Option 2
: Remote Start: Set dryer to “AP” using the Delay Dry pad. This allows use of
the GE Appliances Laundry App via smartphone to start the dryer remotely at the time of
choosing. If the dryer is set to AP with no activity, it will start the dryer 24 hours later.
Air Fluff
(on some models)
Provides 10 minutes of tumbling time with no heat. NOTE: On models without AIR FLUFF
cycle, select TIMED DRY and set Temp to No Heat.
Sound
Use the Sound pad to change the volume of the pad presses and the end of cycle signal.
Press the pad until the desired volume is reached (High, Med, Low) or is turned off. The
clothes should be removed when the end of cycle signal goes off, so wrinkles do not set in.
NOTE
:
• Remove garments promptly at the sound of signal. Place clothes on hangers so wrinkles
will not set in.
• Use the Sound especially when drying fabrics like polyester, knits and permanent press.
These fabrics should be removed so wrinkles will not set in.
(Continued next page)
F