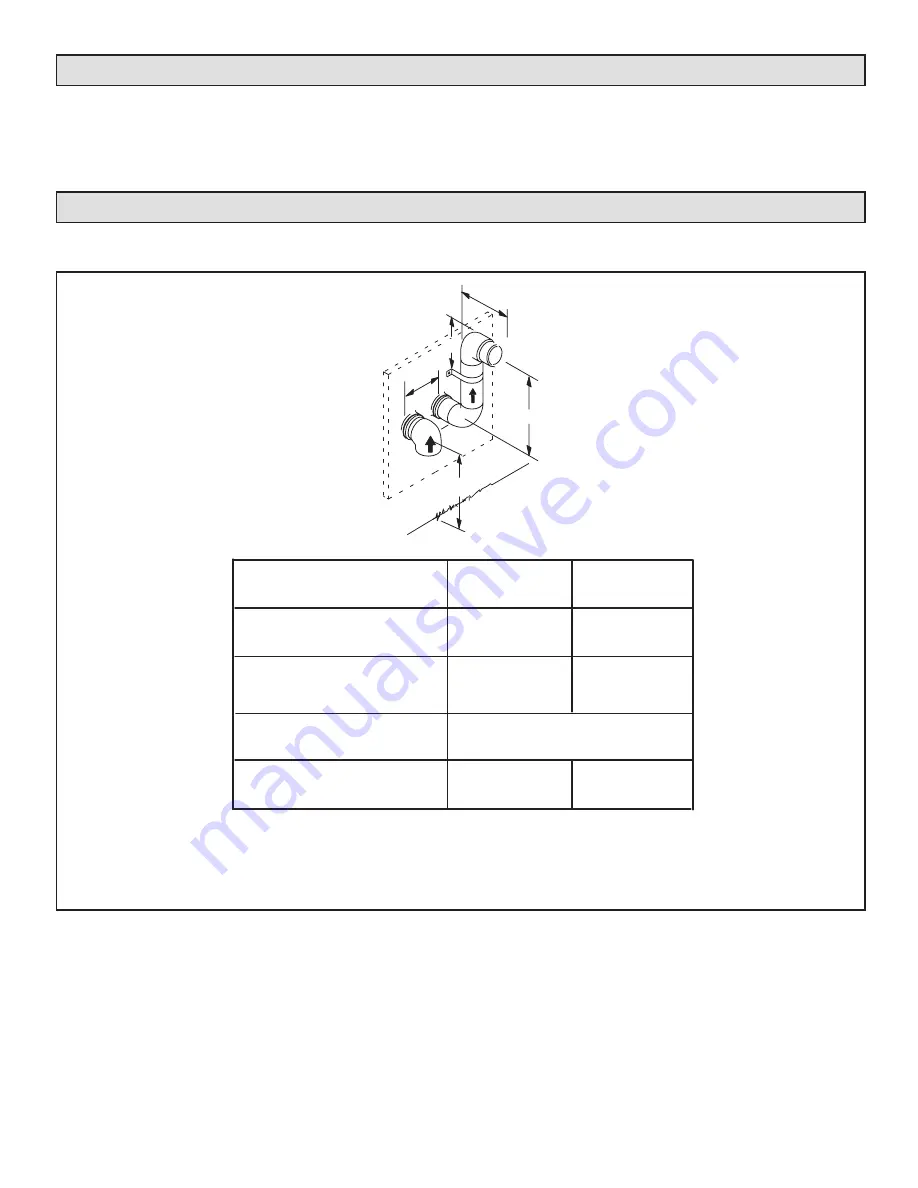
Page 37
31-5000729 Rev. 0
For the Province of Ontario, Horizontal Sidewall Vent Applications Only
For exterior horizontal venting applications, the 2” X 1.5” reducer for 2” venting at the point where the exhaust pipe exits the
structure is not required in direct or nondirect vent applications in the Province of Ontario. In these applications, the vent
should be oriented such that the exhaust plume is unobjectionable. If the installation requires more separation between the
flue gases and the building structure, a reducer may be installed on the exhaust pipe to increase the flue gas velocity.
Addendum for All Provinces of Canada
See below for venting for all provinces of Canada. GEA approves the following termination for use in all provinces of Canada.
.
C
12”
D
B
A
2” (51MM)
Vent Pipe
3” (76MM)
Vent Pipe
12” (305 mm) Min. 12” (305 mm) Min.
6” (152 mm) Min.
24” (610 mm) Max.
6” (152 mm) Max.
6” (152 mm) Min.
24” (610 mm) Max.
6” (152 mm) Max.
A
−
Clearance above grade or
average snow accumulation
B
−
Horizontal separation between
intake and exhaust
C
−
Exhaust pipe length
D
−
Wall support distance from top
of each pipe (intake/exhaust)
NOTE
−
Flue gas may be acidic and may adversely affect some building materials. If flue gases impinge
on the building materials, a corrosion
−
resistant shield should be used to protect the wall surface. The
shield should be constructed using wood, sheet metal or other suitable material. All seams, joints, cracks,
etc. in affected area, should be sealed using an appropriate sealant.
Per: Saskatchewan Code of Practice