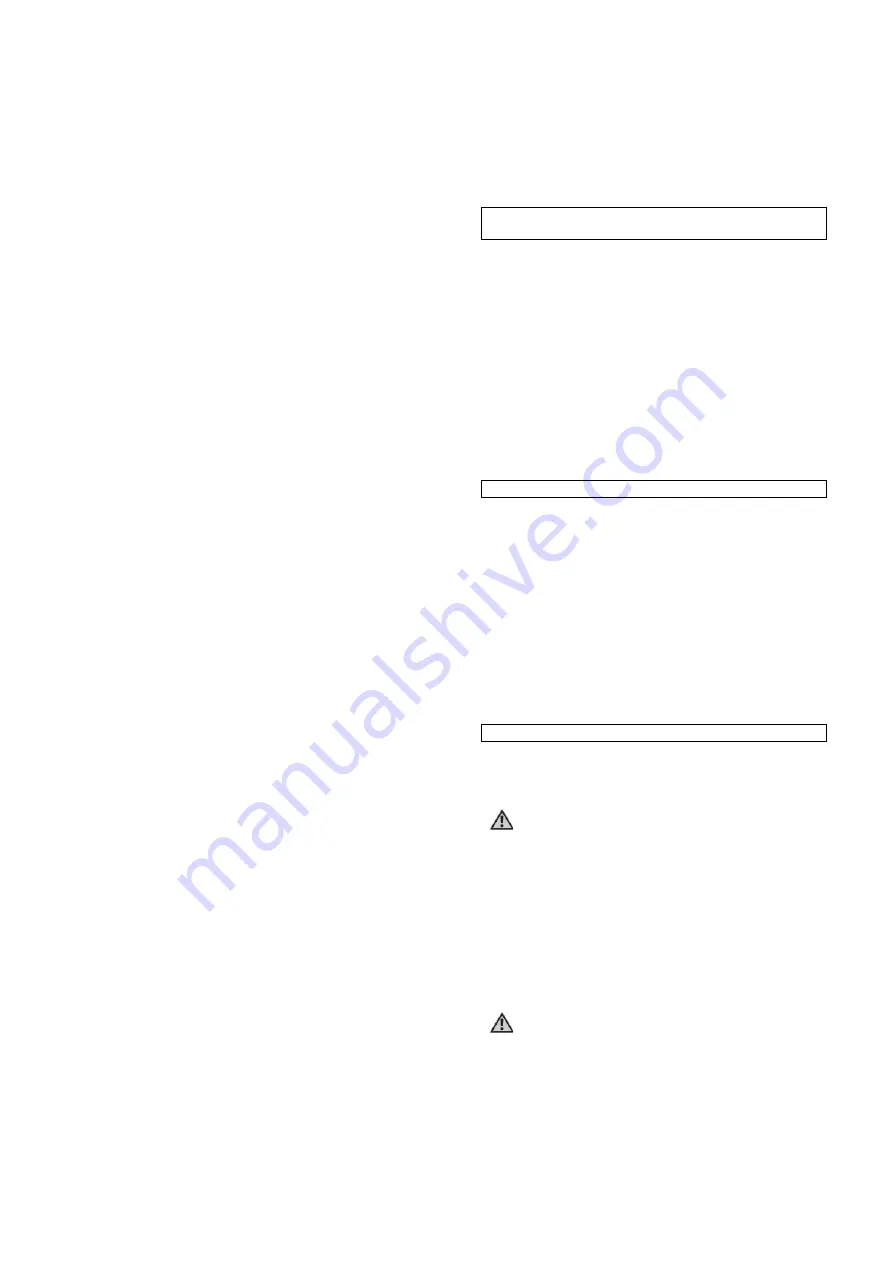
not be used under influence of alcohol, drugs or
medicaments that could cause fatigue.
•
Check the parts for faults or leaks
If any damage of protective equipment or other parts of
the compressor occurred, it is necessary to check it
before putting it into operation again and make sure that
its operation w ill be safe.
All damaged parts must be let repaired or replaced by a
customer service or replace them according to the
instructions specified in the guide for operators.
•
Proper use of the compressor
When operating the compressor observe all instructions
specified in this guide. Do not allow the compressor to
be operated by children or persons that are not
familiarized w ith the w ay of its operation.
•
Keep the ventilating grid clean
Keep the ventilating grid of the motor clean. Clean it in
periodic intervals if you use the compressor in heavily
dirty environment.
•
Use the compressor under the rated voltage
The compressor should be used under the voltage that
is specified at the label w ith electric data. If you operate
the compressor at the voltage higher than rated value,
motor overheating could happen.
•
Do not use the compressor when faulty
If the compressor at w ork produces strange sounds or
vibrates strongly or it seems to be faulty otherw ise, it is
necessary to stop it immediately; have the cause found
in the nearest customer service.
•
Do not clean plastic parts using solvents
Solvents like gasoline, diluters, diesel fuel or other
substances containing alcohol could damage plastic
parts of the compressor. Therefore do not clean plastic
parts using such substances but in case of necessity use
soap lye or suitable liquids.
•
Use original spare parts exclusively
When spare parts from other producers are used your
claims implying from the w arranty are void. Use of
foreign spare parts could result in faults in operation of
the compressor. Original spare parts are available from
our contractual resellers.
•
Do not perform changes at the compressor
Do not make any changes at the compressor. For every
repair contact the customer service. Unauthorized
change could affect the output of the compressor
negatively, but it could also cause serious injuries if
performed by a person not having sufficient technical
know ledge.
•
Do not touch hot parts of the compressor
Do not touch pipelines, motor and others hot parts of the
compressor, otherw ise you face the risk of burning.
•
in case of any maintenance or repairs of safety and
protective devices it is necessary to install them properly
immediately after finishing w orks.
•
It is unconditionally necessary to know the regulations
for accident prevention in force in the given location as
w ell as all others generally recognized safety
regulations.
•
Before the use of this machine you should check safety
devices unconditionally. Make sure w hether parts that
are from visual inspection only slightly damaged could
really operate properly.
•
Unless otherw ise specified in these instructions for use,
any damaged part or safety device must be repaired or
replaced by an authorized service centre.
•
Have damaged sw itches replaced in an authorized
service centre.
•
This machine conforms to all relevant safety regulations.
Repairs may be performed only by qualified electricians
in authorized service centres using original spare parts.
When failing this principle the risk of accidents arises.
•
In operation the number of sw itching cycles (sw itching
on/off) must be 3-10 per hour. The ratio of time of
compressor operation and standstill should be max.
60:40. Longer operation time results in the compressor
overloading.
•
At the end of working day it is necessary to
decommission the compressor properly. (switch it
off; unplug the plug from the socket; release the air
receiver)
•
Never leave the compressor connected in the mains
overnight!
Safety instructions for work with pressurized air and the
blow gun
•
Compressors and piping reach high temperature at
operation. Contact w ith them result in burns.
•
Gases and vapours sucked by the compressor must not
contain admixtures, they could cause fire or explosion
inside the compressor.
•
When releasing the hose coupling the coupling should
be held by a hand to avoid injury resulting from shooting
off the hose.
•
When w orking w ith blow ing gun w ear protective glasses.
Alien objects and blow n parts could cause minor injuries.
•
Do not blow w ith the blow ing gun on persons and do not
clean cloth on a body.
•
Never point to persons or animals w ith the air stream.
•
Never keep the air stream inside any bodily foramen, it
could result in deadly injuries!
Operation of pressure vessels
•
The operator of the pressure vessel must keep it in
proper state, use it properly, check it, perform
immediately the necessary maintenance and repairs,
and adapt necessary safety measures depending on
given circumstances.
•
The regulating authority may order appropriate control
measures in an individual case.
•
The pressure vessel should not be used w hen it exhibits
faults that could threaten members of staff or other
persons.
•
The pressure vessel must be periodically checked for
damage, e.g. corrosion.
•
If you observe any damage, please contact the customer
service w orkshop.
Assembly / first putting into operation
Installation of wheels:
Install the w heels and rubber foots on the machine using
enclosed screw s.
Never lay the compressor on the sidewall because
the oil could flow out.
Stand the compressor at a horizontal, flat and sufficiently
high working surface to avoid possible flowing off the
compressor oil.
Adjustment of the operating unit:
Loosen the w ing-nuts (5) and pull the operating unit forw ard.
Using w ing-nuts fix the operating unit w ith sufficient distance
from the set, so that damages resulting from vibrations are
avoided.
Oil stopper installation: (Fig. 2)
Before putting the compressor into operation the
transport stopper should be replaced with the oil stopper,
and also before each putting into operation the proper oil
level must be made sure.
Remove the transport oil stopper. If necessary fill the oil
up to the mark in the inspection sight. Then fasten the oil
stopper. “Oil replacement“ see “Inspections and
maintenance“.
Air filter assembly: (Fig. 3)
Summary of Contents for 50066
Page 2: ...1 1 14 12 1 10 15 13 8 7 16 6 5 2 3 4 9 2 3 ...
Page 3: ......
Page 66: ......
Page 67: ......