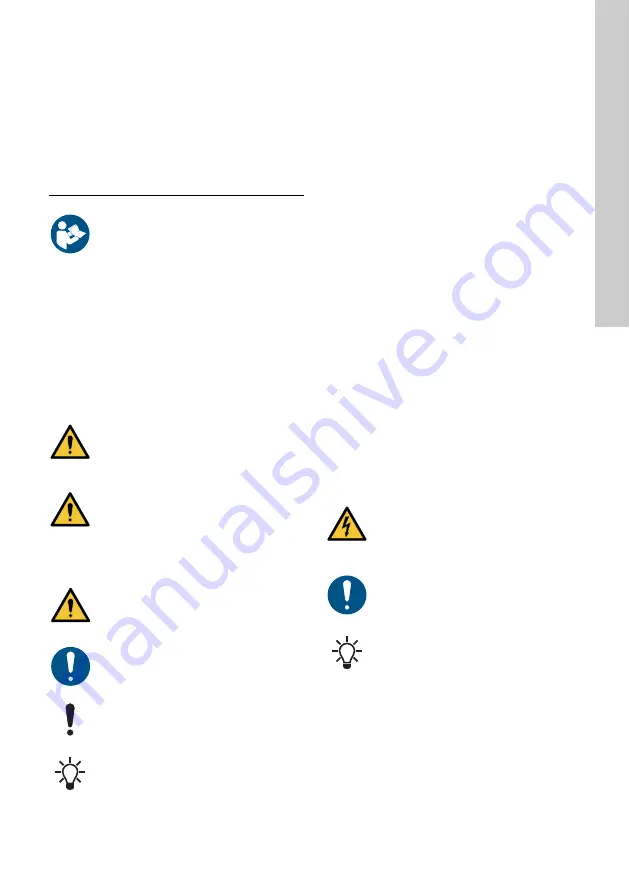
English (GB)
3
1. General information
These installation and operating instructions contain
general instructions that must be observed during
installation, operation and maintenance of the pump.
It must therefore be read by the installation engineer
and the relevant qualified operator prior to
installation and startup, and must be available at the
installation location at all times.
1.1 Symbols used in this document
The text accompanying the hazard symbols is
structured in the following way:
1.2 Qualification and training
The persons responsible for the installation,
operation and service must be appropriately
qualified for these tasks. Areas of responsibility,
levels of authority and the supervision of the persons
must be precisely defined by the operator. If
necessary, the persons must be trained
appropriately.
Risks of not observing the safety instructions
Non-observance of the safety instructions may have
dangerous consequences for persons, the
environment and the pump and may result in the loss
of any claims for damages.
It may lead to the following hazards:
•
Personal injury from exposure to electrical,
mechanical and chemical influences.
•
Damage to humans, animals and the
environment from leakage of harmful substances.
1.3 Safety instructions for the
operator/user
The safety instructions described in these
instructions, existing national regulations on health
protection, environmental protection and for accident
prevention and any internal working, operating and
safety regulations of the operator must be observed.
Information attached to the pump must be observed.
Leakages of dangerous substances must be
disposed of in a way that is not harmful to humans,
animals and the environment.
Damage caused by electrical energy must be
prevented, see the regulations of the local electricity
supply company.
Only original accessories and original spare parts
should be used.
Dismantling the dosing head, diaphragm
and valves in case of diaphragm leakage
Dosing liquid in the pump housing
Read this document before installing the
product. Installation and operation must
comply with local regulations and accepted
codes of good practice.
WARNING
Indicates a hazardous situation which, if
not avoided, could result in death or
serious personal injury.
CAUTION
Indicates a hazardous situation which, if
not avoided, could result in minor or
moderate personal injury.
SIGNAL WORD
Description of hazard
Consequence of ignoring the warning.
- Action to avoid the hazard.
A blue or grey circle with a white graphical
symbol indicates that an action must be
taken.
If these instructions are not observed, it
may result in malfunction or damage to the
equipment.
Tips and advice that make the work easier.
WARNING
Electric shock
Death or serious personal injury
- Keep liquids away from the power
supply and electrical components.
Before starting work on the pump, the
pump must be in the "Stop" operating state
or be disconnected from the power supply.
The system must be pressureless.
The mains plug is the separator separating
the pump from the mains.