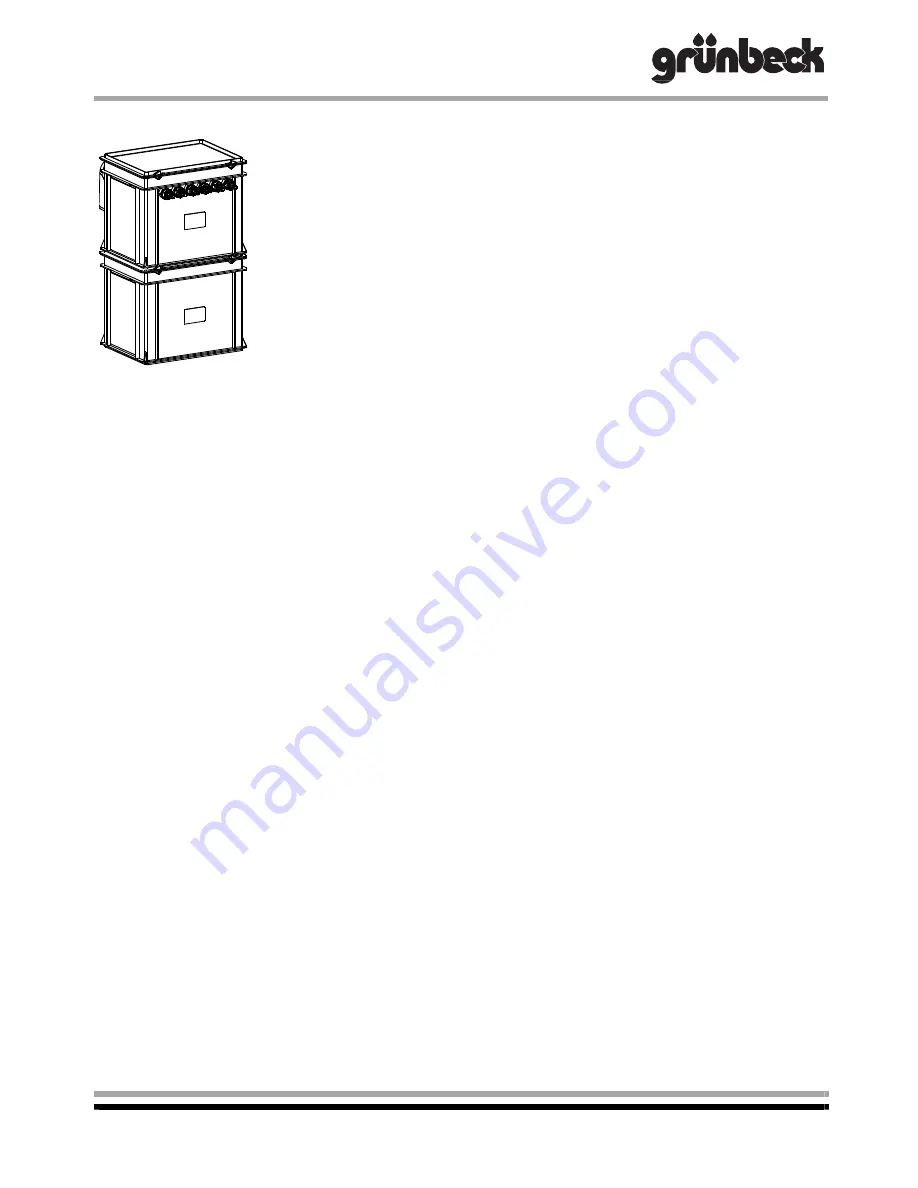
GENO
®
-flushing compressor 1988 K
Order no. 015 151 963-inter Created: KONS-gmei-mrie G:\BA-151963-INTER_GENO-SPUELKOMP-1988_K.DOC
26
Flushing water calming tank
When flushing though drinking water installations, the
flushing water calming tank serves to ensure steady
draining of the flushing water into a floor drain or toilet.
As per DVGW work sheet W 557 when flushing with a
mixture of air and water, the withdrawal points must be
fitted with the relevant equipment in order to separate
the air from the flushing water.
Up to 6 flushing tubes with max. 5 m³/h can be safely
attached to the flushing water calming tank. Thanks to
the integrated free outlet, safe separation of the drinking
water installation and the drain is ensured and back
suction is prevented. Individuals at the withdrawal points
are protected against aerosols and the water flows
steadily into the drain. The discharge of pollution and
clouding in the flushing water is visible. A substructure
box is included in the scope of supply for draining off
water, e.g., into a toilet. This box is also used to
transport various connection parts.
Flow
Qmax 5 m³/h
Inlet connection
6 x tube nozzles 13 mm
(cap nut 3/4")
Outlet connection HT pipe DN 100
Dimensions (without connections)
(B x T) 400 x 300 mm
Height (without/with substructure box)
340/660 mm.
Height outlet connection
(without/with substructure box) 175/498 mm
151 020