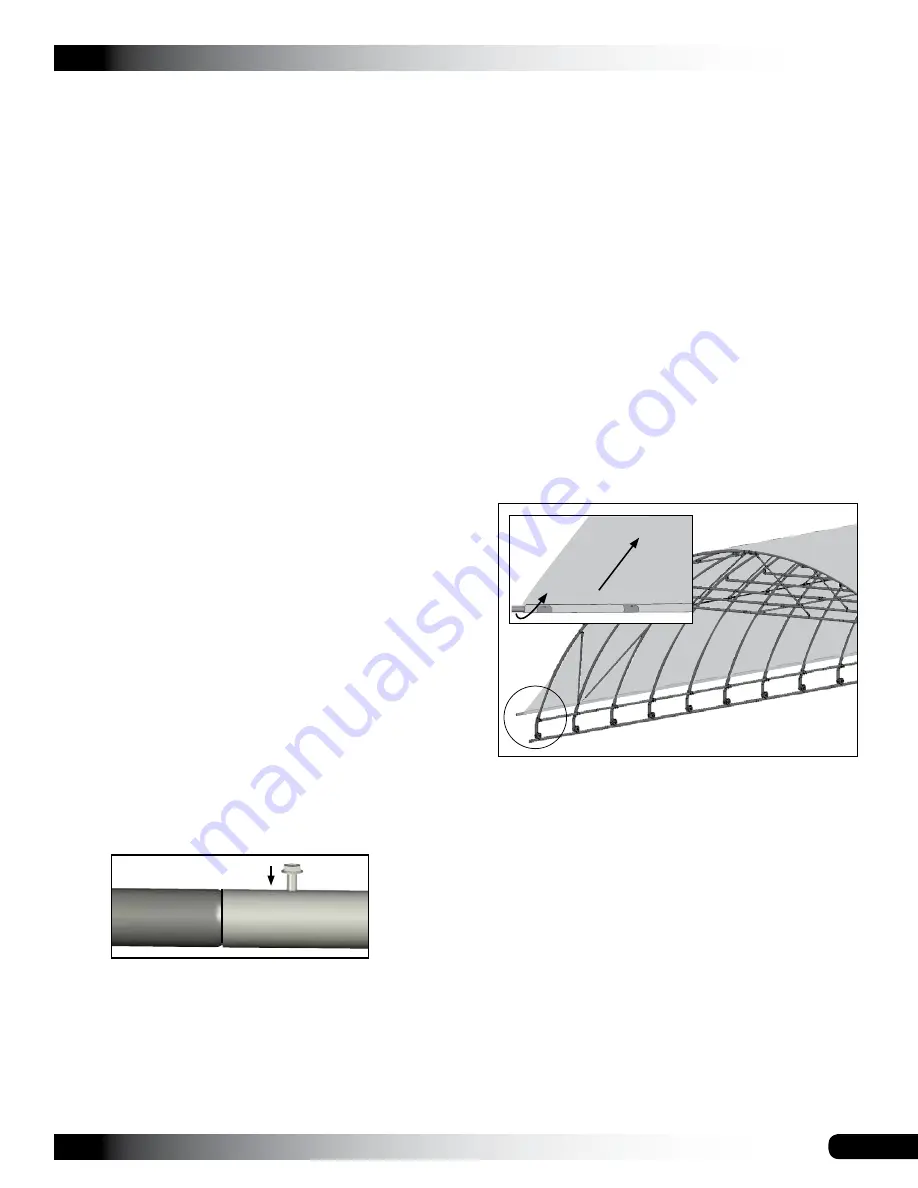
29
GROWSPAN
™
ROLLING PREMIUM HIGH TUNNELS
Revision date: 01.01.16
INSTALL THE ROLL-UP SIDE CONDUIT
Gather the parts:
• Pipe 1.315'' x 75'' Swaged 17 GA (#131S075)
• Pipe 1.315'' x 73.5'' Plain 17 GA (#131P0735)
• Tek Screws
The roll-up side conduit assembly is attached to the bottom
of the roll-up side cover material. This assembly runs the
length of the frame and serves as the center pipe that the
roll-up cover wraps around when it is opened to ventilate
the shelter.
This conduit is identical to the purlins that were
assembled and attached to the frame.
Complete these steps to assemble the roll-up side conduit.
1. Locate all sections of pipe needed to assemble the
cover conduit.
2. Insert the swaged end of each pipe into the plain end of
another pipe until the conduit is assembled.
3. Secure each pipe joint with a Tek screw.
INSTALL THE ROLL-UP SIDE ASSEMBLIES
The instructions below describe how to install a single
roll-up sidewall assembly for one side of the frame. The
procedure is repeated for the remaining side.
The procedures to install the roll-up side include the
following:
1. Assemble the roll-up side conduit.
2. Attach the roll-up conduit to the bottom of the cover
film.
3. Assemble the Twist-of-the-Wrist assembly and attach it
to the frame and the roll-up side.
4. Install the Anti-Billow Rope system.
5. Test the operation of the roll-up side.
4. Place the assembled conduit at the base of the side
where the end of the cover film is located.
NOTE:
Duct tape Tek screws to prevent damage to
cover film.
5. Continue with the procedure that follows to attach the
conduit to the cover film.
ATTACH CONDUIT TO COVER FILM ROLL-UP SIDE
Gather the parts:
• Assembled conduits
• Fabric Clips #CC6212 (Divide quantity in half.) Use
one clip at each rafter position along each side when
attaching the cover film to the roll-up conduit.
• FA4482B Tek screws
To this point, the cover film should be secured to the frame
and the excess cover along both sides should be hanging
down along the side of the frame.
1. Unfold the remaining portion of the cover film (if
needed) and evenly stretch it out on the ground along
the frame.
2. Working from the inside the frame
, roll the assembled
cover conduit onto the edge of the cover film.
3. Verify that the cover and conduit are evenly positioned
and tuck the cover edge under the conduit and rotate
the conduit 1-2 times to wrap the cover around it.
4. Secure the cover material to the conduit using Tek
screws and fabric clips evenly spaced along the
conduit—one clip at each rafter position.
5. Roll the conduit until the excess cover film is wound
around the conduit.
6. Continue with the
Twist-of-the-Wrist Assembly
procedure.
Inside View