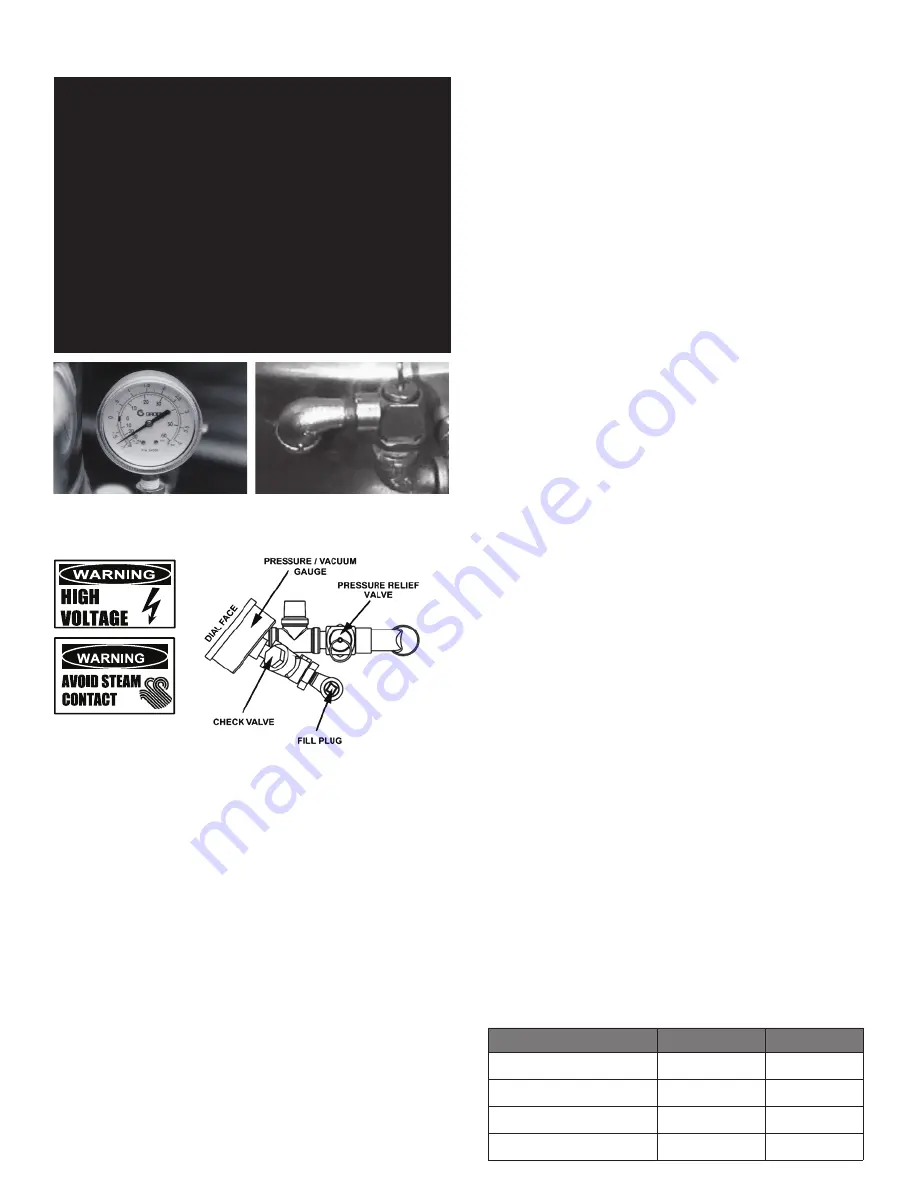
7
OM-TDH(C)-20/24/40/48 (C,A) (CE) INTERNATIONAL
MAINTENANCE
WARNING: AVOID ANY EXPOSURE TO THE STEAM BLOWING OUT OF THE PRESSURE
RELIEF VALVE. SEVERE BURNS CAN RESULT ON EXPOSED SKIN. FAILURE
TO CHECK PRESSURE RELIEF VALVE OPERATION PERIODICALLY COULD
RESULT IN PERSONAL INJURY AND/OR DAMAGE TO EQUIPMENT.
CAUTION: KEEP GREASE AWAY FROM ELECTRICAL PARTS LOCATED NEAR THE
GEARS.
WARNING: TO AVOID INJURY, READ AND FOLLOW ALL PRECAUTIONS STATED ON THE
LABEL OF THE WATER TREATMENT COMPOUND.
WARNING: USE OF ANY REPLACEMENT PARTS OTHER THAN THOSE SUPPLIED BY
THE MANUFACTURER OR THEIR AUTHORIZED DISTRIBUTORS CAN CAUSE
INJURY TO THE OPERATOR AND DAMAGE TO THE EQUIPMENT AND WILL
VOID ALL WARRANTIES.
CAUTION: INSURE ELECTRICAL POWER IS REMOVED AND THE GAS IS TURNED OFF AT
THE SHUTOFF VALVE PRIOR TO PERFORMING ANY MAINTENANCE ON THIS
KETTLE.
WARNING: THIS KETTLE IS DESIGNED TO BE WATER RESISTANT. FAILURE TO FOLLOW
PROPER MAINTENANCE PROCEDURES MAY VOID THE WARRANTY.
The pressure gauge should show a vacuum of -20
to -30 inches of mercury (Hg) vacuum or a range of
-0.7 to -1.0 Bar when the kettle is cold.
The open end of the pressure relief valve
elbow must face downward.
The pressure relief valve and fill plug are located directly
behind the pressure/vacuum gauge.
PERIODIC MAINTENANCE
NOTICE: Contact an authorized representative when repairs are required.
A Maintenance & Service Log is provided at the back of this manual. Each time
maintenance is performed on your kettle, enter the date on which the work was
done, what was done, and who did it. Keep this manual on file and available
for operators to use. Periodic inspection will minimize equipment down time and
increase the efficiency of operation. The following points should be checked:
JACKET VACUUM/REMOVING AIR FROM JACKET
When the kettle is cold, a positive pressure reading on the pressure/vacuum gauge
or a reading near 0 psi (0 kPa, 0 bar) indicates that there is air in the jacket. Air in
the jacket acts as an insulator, and slows kettle heating.
To remove air:
1. Start the unit. (Be sure there is water or product in the kettle when heating).
2. When the pressure/vacuum gauge reaches a positive pressure reading of 5 psi
(35 kPa, 0.34 bar), release the trapped air and steam by pulling up the safety
valve ring for about five seconds. Repeat this step three or four times. Then let
the pull ring snap back into the closed position.
3. If there is little discharge (mostly air), and the pressure gauge drops back to 0
psi (0 kPa, 0 bar), allow the pressure to build back to 5 psi (35 kPa, 0.34 bar)
and repeat the procedure.
4. Once steam has been vented from the jacket as described in b, above, remove
the hot water from the kettle and replace it with cold. This will condense steam
in the kettle jacket, and the pressure gauge should show -20 to -30 inches
of mercury (Hg) vacuum or a range of -0.7 to -1.0 Bar. If it does not, or if the
vacuum is leaking down, contact an authorized service agency to correct the
problem.
PRESSURE RELIEF VALVE
At least twice a month, test the pressure relief valve. Test the valve with the kettle
operating at 15 PSI (105 kPa, 1.1 bars), by holding the test ring for at least five
seconds. Then release the ring and permit the valve to snap shut. If the ring does
not activate, if there is no discharge, or if the valve leaks, stop using the kettle
immediately and contact a authorized service representative.
GREASE / LUBRICATION
1. Hand Tilt Models
At least twice a year, grease the two trunnion bearings. The bearings are
located within the kettle support housing. Remove the access panels from the
support housing with a screwdriver to gain access to the grease fittings. Use
a lithium-based, multi-purpose grease. When the access panels are removed,
the mounting bolts for the trunnion bearings and tilt switch can also be checked
for tightness. When finished, reassemble access panels to support housing.
2. Crank Tilt Models
The gear housing has been fitted for proper lubrication of moving parts.
Since the gears do not run in oil, periodic lubrication with grease is essential.
Frequency of lubrication depends on operating conditions, but should occur
at least once every six months. The use of a Number Two grade LGI lithium
grease is recommended. Add grease through the Zerk fittings on the gear
housing until grease flows out of the bearings around the trunnion shaft. Place
a liberal amount of grease on the gear to cover the arc that is in contact with
the worm gear.
JACKET FILLING AND WATER TREATMENT
The jacket was charged at the factory with the proper amount of treated water.
You may need to restore this water, either because it was lost as venting steam or
by draining. If you are replacing water lost as steam, use distilled water. If you are
replacing treated water that ran out of the jacket, prepare more treated water as
directed in “Water Treatment Procedure,” below.
1. If you are replacing water lost as steam, use distilled water. Do not use tap
water. If you are replacing treated water that was drained from the jacket,
prepare more treated water as directed below.
2. Allow the kettle to cool completely. Remove the pipe plug from the jacket fill
assembly. Pour in the distilled or treated water. Using a funnel will help you
in this process. Hold the pressure relief valve open while you pour, to let air
escape from the jacket. Continue adding water until the water level rises to the
center of the round sight glass.
3. Air that gets into the jacket during the filling operation must be removed, because
it will make heating less efficient. Follow the procedure in Jacket Vacuum/
Removing Air From Jacket above, to restore a negative pressure reading.
WATER TREATMENT PROCEDURE
1. Obtain water treatment compound and a pH test kit from your Groen Service Agent.
2. Fill a mixing container with the measured amount of water required. Use only
distilled water.
Model
Kettle Capacity
Jacket Capacity
TDH-20 (C,A), TDHC-20 (C,A)
5 gal (20 qt), 19 liter
6 quart, 5.7 liter
TDH-24 (C,A), TDHC-24 (C,A)
6 gal (24 qt ), 23 liter
6 quart, 5.7 liter
TDH-40 (C,A), TDHC-40 (C,A)
10 gal (40 qt), 38 liter 12 quart, 11.4 liter
TDH-48 (C,A), TDHC-48 (C,A)
12 gal (48 qt), 45 liter 12 quart, 11.4 liter