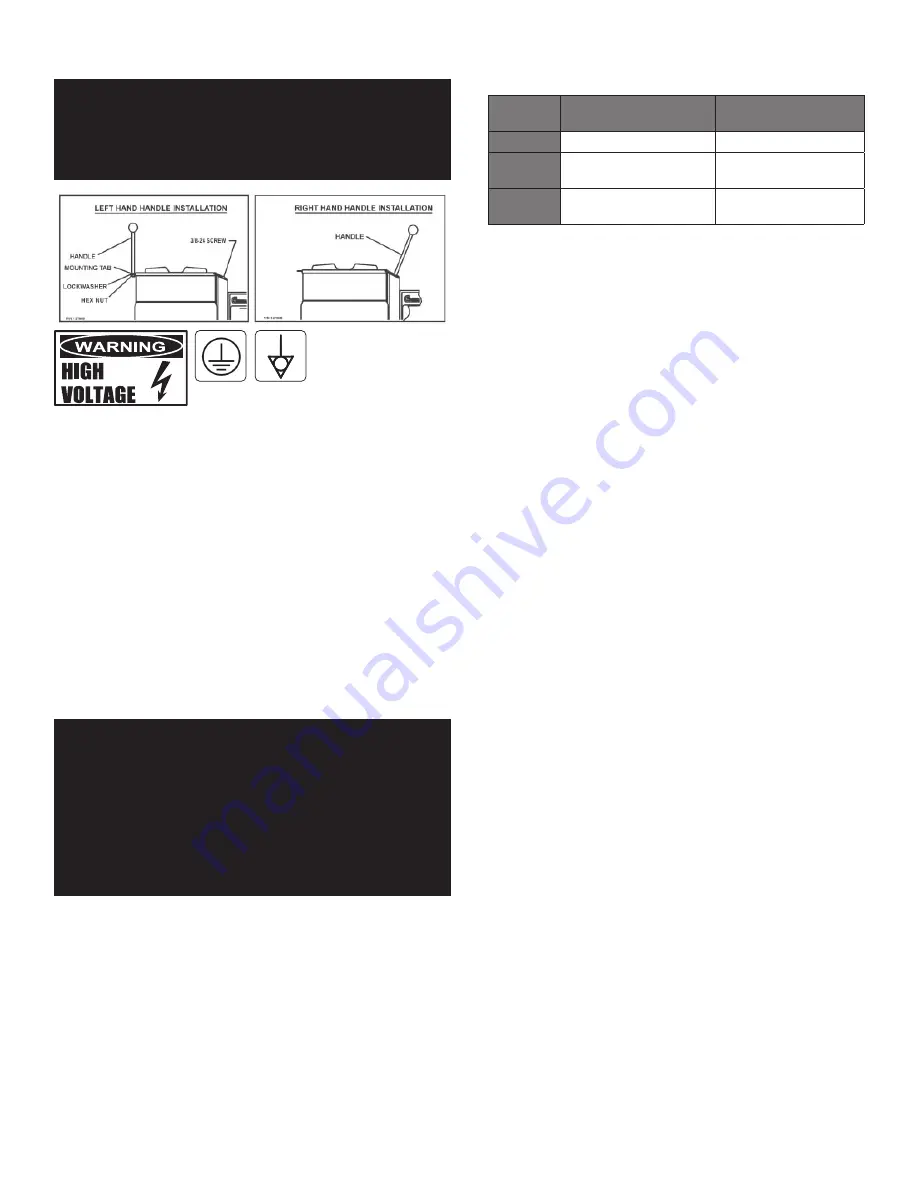
3
OM-TDH(C)-20/24/40/48 (C,A) (CE) INTERNATIONAL
INSPECTION & UNPACKING
CAUTION: SHIPPING STRAPS ARE UNDER TENSION AND CAN SNAP BACK WHEN CUT.
TAKE CARE TO AVOID PERSONAL INJURY OR DAMAGE TO THE UNIT BY
STAPLES LEFT IN THE WALLS OF THE CARTON.
CAUTION: THIS UNIT WEIGHS BETWEEN 214 AND 240 POUNDS (98 TO 109 KG)
DEPENDING ON SIZE. INSTALLER SHOULD USE PROPER EQUIPMENT TO
LIFT SAFELY.
Figure 2
Figure 1
The unit arrives completely assembled, except for the tilting handle on hand tilt
models which is shipped inside the kettle. The unit is strapped on a skid and in
a heavy carton. Inspect the carton carefully for damage. Open the container and
check the unit for hidden damage. Report shipping damage or shipment errors to
the delivery agent.
Write down the model number, serial number, and installation date for your unit at
the top of the Service Log at the end of this manual. Keep this manual with the unit.
To remove the kettle from the box, cut any straps from around the box. Detach the
box sides from the skid. Pull the box up off the unit, taking care to avoid damage
or injury from any staples left in the box walls. When installation is to begin, cut
the straps holding the kettle on the skid, and lift the kettle straight up off the skid.
Examine the packing materials to make sure no loose parts are discarded with the
materials. On hand tilt models, the tilting handle may be screwed into its socket.
Attach handle to the kettle on left side or right side as shown below.
INSTALLATION
WARNING: THE UNIT MUST BE INSTALLED BY PERSONNEL WHO ARE QUALIFIED TO
WORK WITH GAS, ELECTRICITY AND PLUMBING. IMPROPER INSTALLATION
CAN CAUSE INJURY TO PERSONNEL AND/OR DAMAGE TO THE EQUIPMENT.
THE UNIT MUST BE INSTALLED IN ACCORDANCE WITH APPLICABLE CODES.
THE UNIT MUST BE INSTALLED BY A LICENSED PLUMBER OR GAS FITTER
WHEN INSTALLED WITHIN THE COMMONWEALTH OF MASSACHUSETTS.
DANGER: ELECTRICALLY GROUND THE UNIT AT THE TERMINAL PROVIDED. FAILURE
TO GROUND UNIT COULD RESULT IN ELECTROCUTION AND DEATH.
WARNING: THIS UNIT IS FOR COMMERCIAL USE. DO NOT USE HOME OR RESIDENTIAL
GRADE GAS CONNECTIONS. THEY DO NOT MEET GAS CODES AND COULD
BE HAZARDOUS.
For efficient performance the kettle must be installed in a well-ventilated
area. Items which might restrict or obstruct the flow of air for combustion and
ventilation must be removed. The area directly around the appliance must be free
of combustible materials.
1. Installation can be on a combustible or noncombustible floor. Clearances
should be per table below.
MINIMUM CLEARANCE FROM
COMBUSTIBLE WALLS
RECOMMENDED
CLEARANCES
Left Side
1 in. (25 mm)
1 in. (25 mm)
Right Side
0 in. (0 mm)
12-16 in. (305-406 mm)
for servicing
Rear
1 in. (25 mm)
3 in. (76 mm)
for faucet bracket
2. We recommends installation of the unit under a vent hood. The base must be
fastened to a working surface or stand.
3. Complete the piping to the gas service main using ½ inch IPS (1/2” BSPT) pipe
or an approved equivalent.
4. Provide 230 VAC, 50 Hz, 1 Phase, 1 Amp or 40W electric service. The wiring
must be executed in accordance with regulations IEE Regulation For Electrical
Installations and Electricity at Work Regulations. AN ELECTRICAL GROUND
IS REQUIRED. Equipotential (Figure 2) and protective (Figure 1) earth ground
terminals are provided. The electrical schematic is located on the inside of the
service panel and in this manual.
5. Electrical connection to the unit must be water resistant sealtite conduit type
or equal and utilize the water resistant conduit fitting provided on the unit.
6. The installation must conform with local codes or in accordance to
recommendations are contained in the Institute of Gas Engineers publications
IGE/UP/1, IGE/UP/2, BS6173 & BS5440. The kettle should be installed in an
adequately ventilated room with provision for adequate air supply. The best
ventilation will employ a vent hood and exhaust fan with no direct connection
between the vent duct and the kettle flue. DO NOT obstruct the flue or vent
duct after installation.
7. PRESSURE TEST WARNING
a. Test pressure exceeding ½ PSIG (3.45 kPa). During pressure testing of
the gas supply piping system at pressures exceeding ½ PSIG (3.45), the
appliance and its individual shutoff valve must be disconnected from the
gas supply piping system.
b. Test pressure equal to or less than ½ PSIG (3.45 kPa). During pressure
testing of the gas supply piping system at pressures equal to or less than
½ PSIG, the kettle must be isolated from the gas supply piping system by
closing its individual manual shutoff valve.
8. Adequate space for proper servicing and operation is required. DO NOT block
any air intake spacings to the combustion chamber or obstruct air flow.
9. After the kettle has been connected to the gas supply, check all gas joints for
leaks. A soap solution or other suitable gas leak detector should be used. Do
not use flame when checking for leaks.
10. Once the unit is anchored to a mounting surface, apply a small bead of silicone
caulk around the perimeter of the kettle base and seal the joint.
11. Make sure the water level is correct in the jacket, by confirming that the
level is near the middle of the sight glass. If the water level is low, follow the
instructions in Jacket Filling and Water Treatment in the Maintenance section
of this manual.
12. Check to be sure that the open end of the elbow on the outlet of the pressure
relief valve is directed downward. Be sure to read and follow the instructions
on the attached pressure relief valve tag.