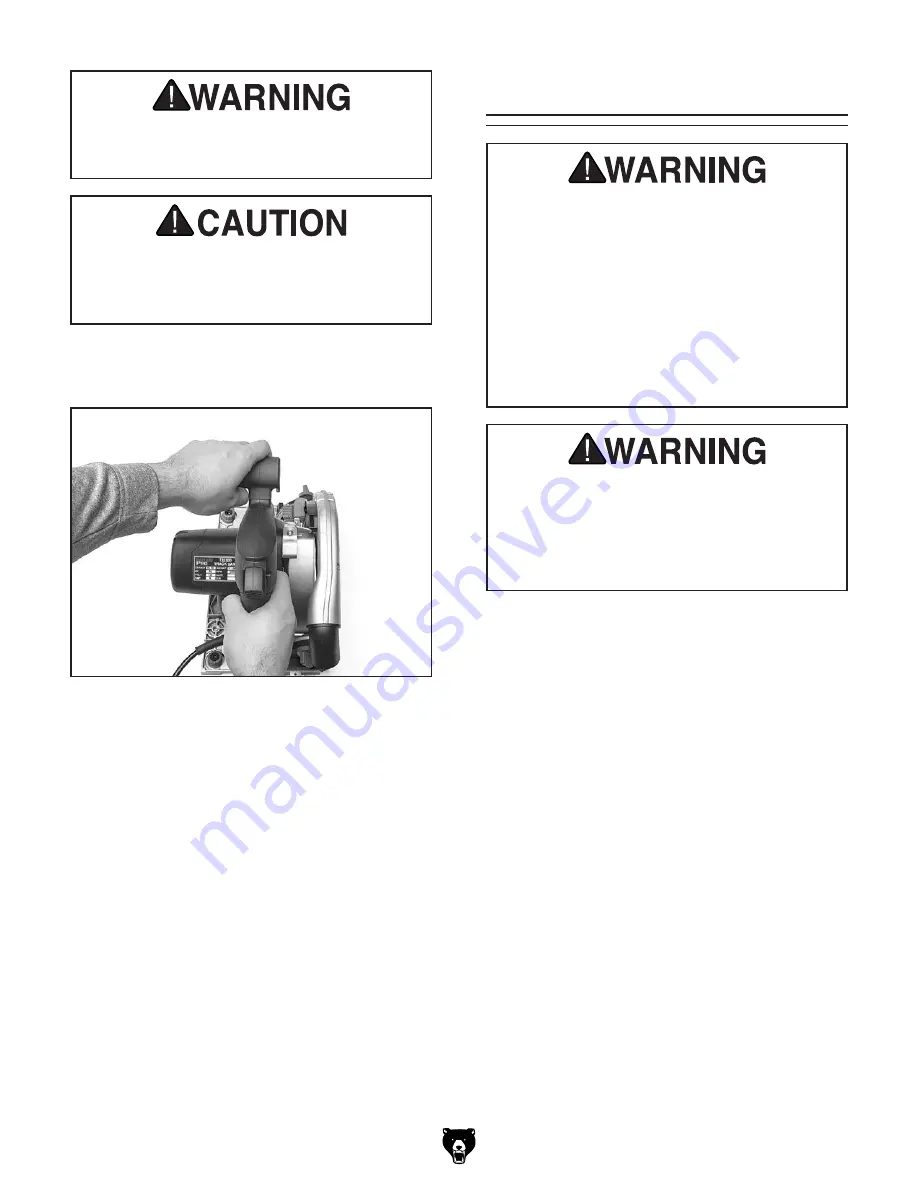
Let saw reach full speed before contacting
workpiece. Doing so will reduce risk of kick-
back, help provide cleanest cut, and reduce
stress on saw motor.
Keep fingers and hands away from saw
blade and out of blade path during opera-
tion. Use clamps to hold workpiece in place.
Making blind plunge cuts without check-
ing cutting path for unseen objects could
result in injury from kickback, electrocution,
building damage or fire, gas explosions,
or death. Whenever making a blind plunge
cut into a standing structure (like a wall),
always check cutting path for hidden wires,
nails, and other metal objects by thoroughly
scanning area with an electric stud finder or
similar device. NEVER risk a blind plunge
cut without first checking your cutting path.
Whenever operating saw in vicinity of live
wires, always wear insulated gloves. Avoid
unintentionally grounding yourself when
operating saw by being in contact with elec-
trically-conductive materials (metal pipes,
appliances, etc.).
Figure 15. Proper hand positions.
Model T33300 (Mfd. Since 04/22)
-21-
3. Hold saw firmly with one hand on each
handle (see
Figure 15).
Plunge cuts are made by positioning the saw on
the workpiece so that the blade begins cutting as
soon as it is lowered. Plunge cuts work well for
removing an area within the workpiece without
sawing through the outer perimeter.
To make plunge cuts:
1. Mark desired start and stop cut-points on
workpiece.
2. Set depth of cut (see Setting Cutting Depth
on
Page 19).
4. Engage plunge release and extend blade.
Activate saw by pulling power trigger while
holding plunge release.
Note: Holding ON/OFF trigger alone will not
activate saw. For power to be activated, both
plunge release and ON/OFF trigger must be
pressed. After power has been activated,
plunge release can be disengaged.
5. Move saw forward over workpiece in an
even, steady motion.
6. When finished, release ON/OFF trigger and
allow blade to come to a complete stop.
Return saw to an upright position by lifting up
on handle and allowing blade to retract and
lock in place.
Making Plunge Cuts
Summary of Contents for T33300
Page 36: ......