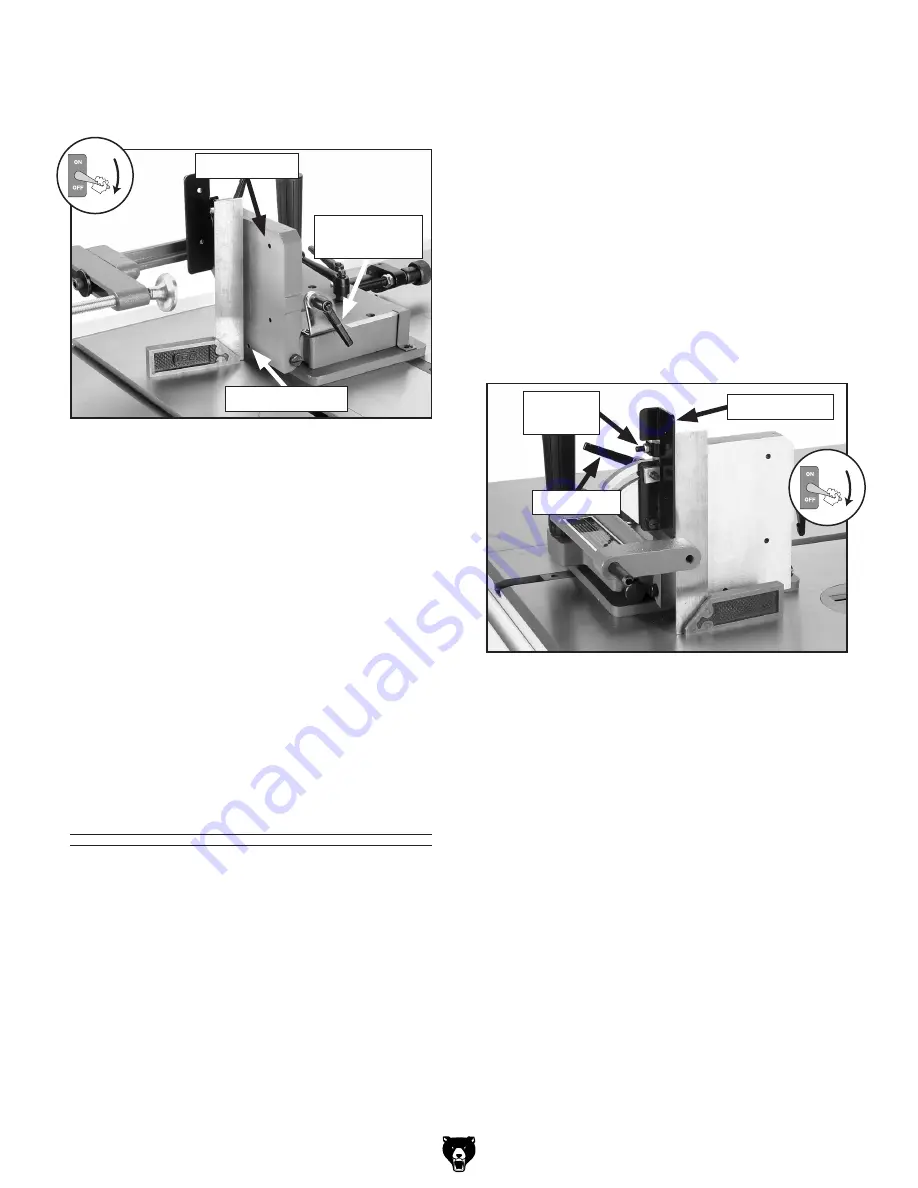
h7583 tenoning Jig
-13-
5. thread the positive stop set screw far enough
away from the side support so that it will not
interfere with the next step (see
figure 14).
6. position the machinist's square flat on the
table and up against the jig side support.
7. loosen the support lock lever, position the
side support flat against the machinist's
square, then, without moving the support, re-
tighten the lock lever.
8. remove the square and re-tighten the stop
set screw until it just meets resistance. the
90° positive stop is now set for quick perpen-
dicular positioning of the side support.
back Support
adjustment
To adjust the back support:
1. disConnECt tABlE sAW FroM
poWEr!
2. Completely lower the saw blade so that it will
not interfere with the measurements.
3. Clean away any debris from the table or jig
that could affect the measurements, then
insert the jig all the way into the miter slot.
4. loosen the jam nut on the positive set screw,
then back off the set screw to allow adjust-
ment to the back support (see
figure 15).
figure 14. Adjusting the side support
perpendicular to the saw table.
side support
side support
lock lever
stop set screw
in this procedure you will adjust the back support
perpendicular to the saw table, then set the 90°
positive stop so the back support can be returned
to the perpendicular position after an angle cut.
5. position the machinist's square flat on the
table and up against the back support of the
jig, as shown in
figure 15.
6. loosen the support lock lever, position the
back support flat against the machinist's
square, then, without moving the support, re-
tighten the lock lever.
7. remove the square and re-tighten the stop
set screw until it just meets resistance, then
re-tighten the jam nut to secure the setting.
the 90° positive stop is now set for quick per-
pendicular positioning of the back support.
figure 15. Adjusting the back support
perpendicular to the saw table.
Back support
stop set
screw
lock lever