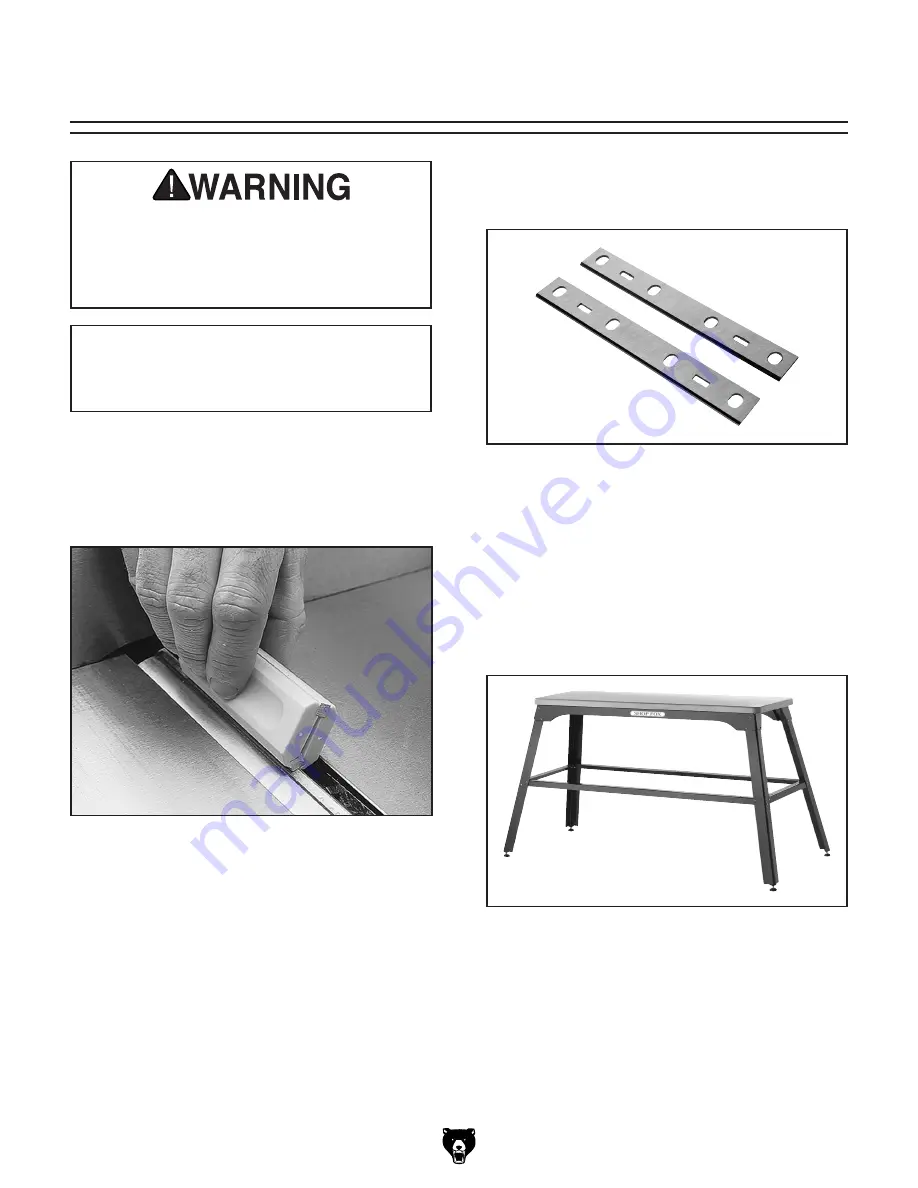
Model G0725 (Mfd. Since 02/20)
-29-
SECTION 5: ACCESSORIES
D1123—Jointer/Planer Knife Hone
Add a razor hone to your planer and jointer knives
with this hand-held sharpening device. The handy
tool sharpens flat and beveled surfaces quickly
and easily. Great for touch-ups.
Figure 39. D1123 Jointer/Planer Knife Hone.
Installing unapproved accessories may
cause machine to malfunction, resulting in
serious personal injury or machine damage.
To reduce this risk, only install accessories
recommended for this machine by Grizzly.
NOTICE
Refer to our website or latest catalog for
additional recommended accessories.
order online at
www.grizzly.com
or call
1-800-523-4777
Figure 40. H9837 Replacement Knives.
H9837—6" Jointer Knives (Set of 2)
Replacement jointer knives made specifically for
the G0725 Jointer.
D3640—Shop Fox Tool Table Plus
The Tool Table Plus was designed in response
to customer requests for a slightly wider and
taller table to accommodate small planers, wood
lathes, sanders and a variety of other benchtop
machines. The butcher block finish table is 1-1/4"
thick and measures 14" x 40". The total height of
the tool table is 33". When assembled properly,
the tool table has a 700 lb. maximum capacity.
Figure 41. D3640 Shop Fox Tool Table Plus.
Summary of Contents for G0725
Page 44: ......