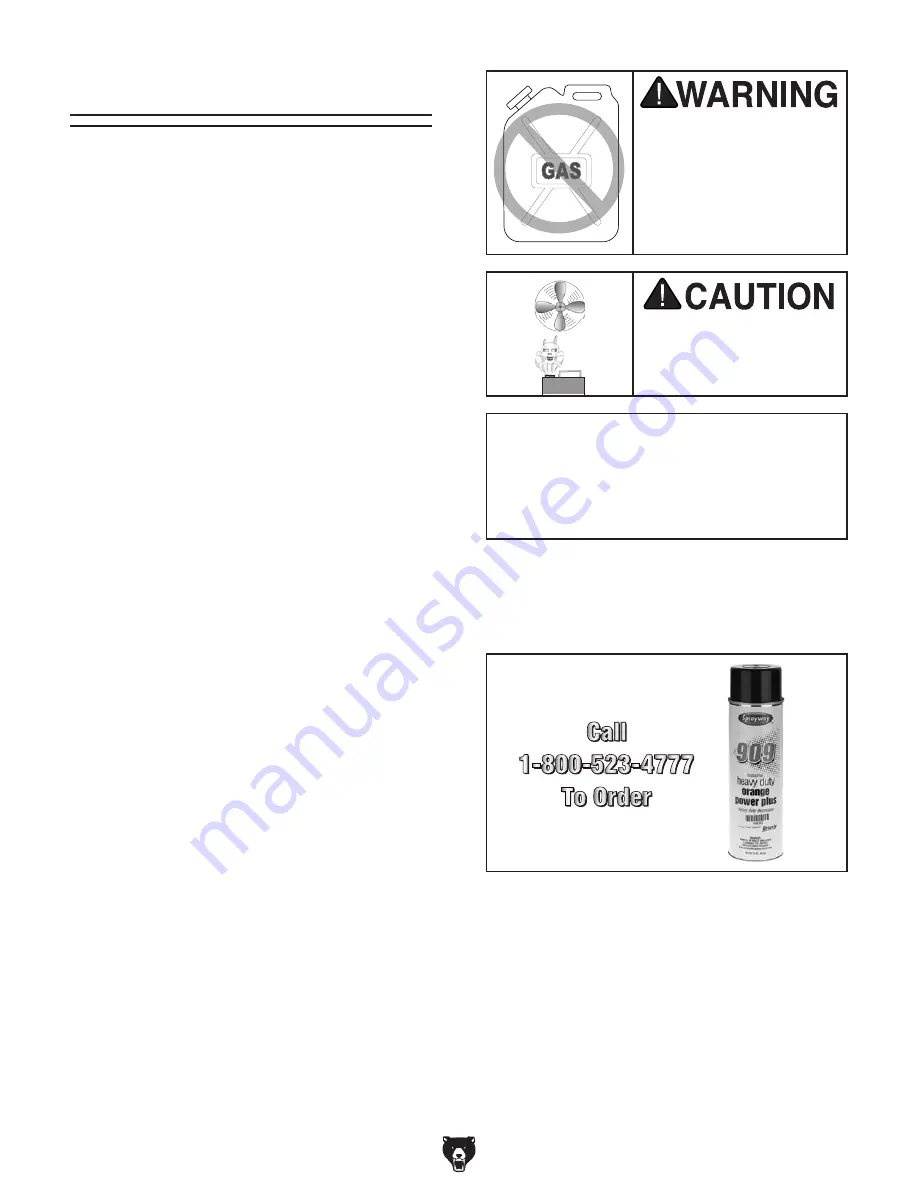
Model G0636X (Mfd. Since 09/18)
-15-
T23692—Orange Power Degreaser
A great product for removing the waxy ship-
ping grease from the
non-painted parts of the
machine during clean up.
The unpainted surfaces of your machine are
coated with a heavy-duty rust preventative that
prevents corrosion during shipment and storage.
This rust preventative works extremely well, but it
will take a little time to clean.
Be patient and do a thorough job cleaning your
machine. The time you spend doing this now will
give you a better appreciation for the proper care
of your machine's unpainted surfaces.
There are many ways to remove this rust preven-
tative, but the following steps work well in a wide
variety of situations. Always follow the manufac-
turer’s instructions with any cleaning product you
use and make sure you work in a well-ventilated
area to minimize exposure to toxic fumes.
Before cleaning, gather the following:
•
Disposable rags
•
Cleaner/degreaser (WD•40 works well)
•
Safety glasses & disposable gloves
•
Plastic paint scraper (optional)
Basic steps for removing rust preventative:
1. Put on safety glasses.
2. Coat the rust preventative with a liberal
amount of cleaner/degreaser, then let it soak
for 5–10 minutes.
3. Wipe off the surfaces. If your cleaner/degreas-
er is effective, the rust preventative will wipe
off easily. If you have a plastic paint scraper,
scrape off as much as you can first, then wipe
off the rest with the rag.
4. Repeat Steps 2–3 as necessary until clean,
then coat all unpainted surfaces with a quality
metal protectant to prevent rust.
Gasoline and petroleum
products have low flash
points and can explode
or cause fire if used to
clean machinery. Avoid
using these products
to clean machiner y.
Many cleaning solvents
are toxic if inhaled. Only
work in a well-ventilated
area.
NOTICE
Avoid harsh solvents like acetone or brake
parts cleaner that may damage painted sur-
faces. Always test on a small, inconspicu-
ous location first.
Cleanup
Cleanup
Figure 5. T23692 Orange Power Degreaser
Summary of Contents for G0636X
Page 15: ...Model G0636X Mfd Since 09 18 13 5mm Hardware Recognition Chart...
Page 68: ......