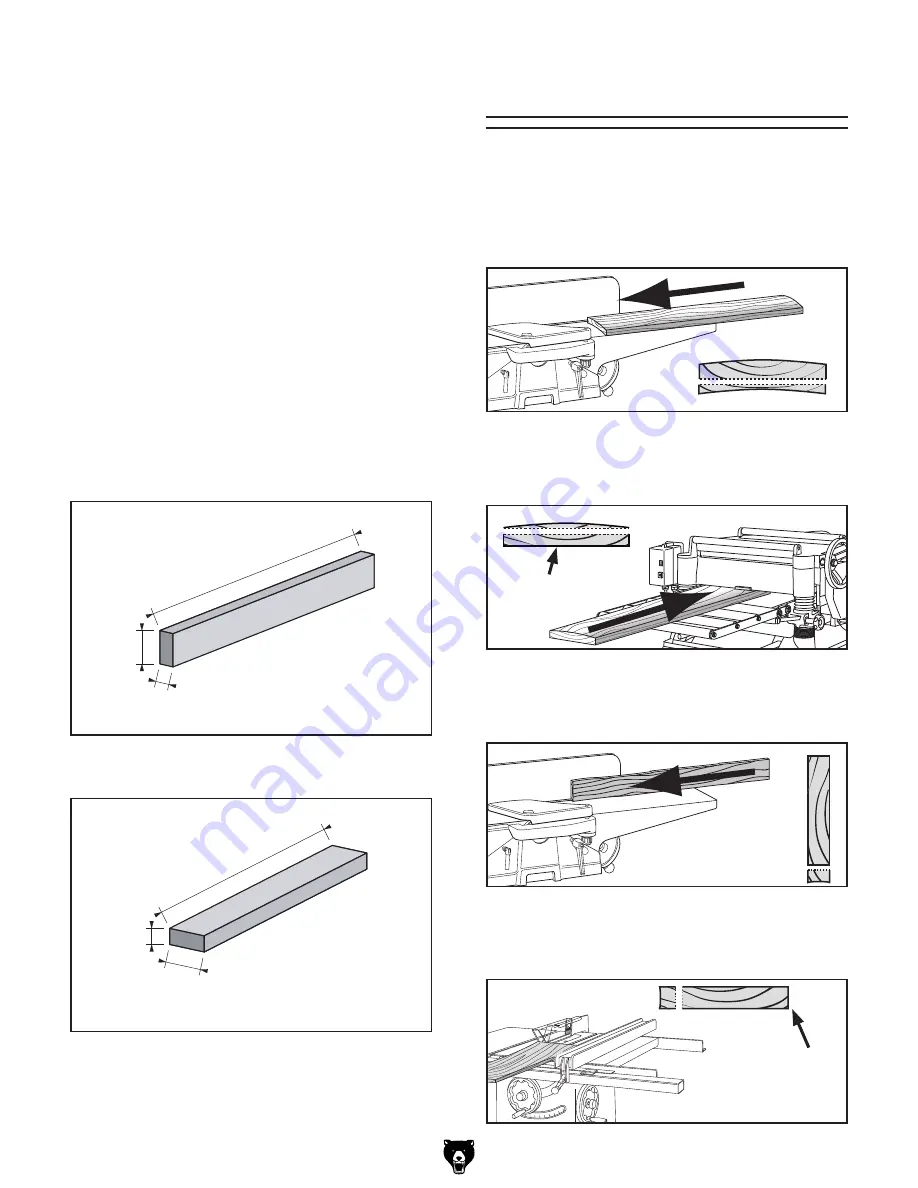
G0604 6" X 56" Jointer
-23-
•
Remove foreign objects from the stock.
Make sure that any stock you process with
the jointer is clean and free of any dirt,
nails, staples, tiny rocks or any other foreign
objects that may damage the jointer blades.
•
Only process natural wood fiber through
your jointer.
Never joint MDF, particle board,
plywood, laminates or other synthetically
made materials.
•
Make sure all stock is sufficiently dried
before jointing.
Wood with a moisture con-
tent over 20% will cause unnecessary wear
on the knives and poor cutting results.
•
Make sure your workpiece exceeds
the minimum dimension requirements
(Figures 26 & 27) before edge jointing or
surface planing, or it may break or kick
back during the operation!
Figure 26.
Minimum dimensions for edge
jointing.
Figure 27.
Minimum dimensions for surface
planing.
1
⁄
2
" Min.
1
⁄
2
" Min.
1" Min.
1" Min.
10" Min.
10" Min.
��
��
��
Squaring stock involves four steps performed
in the order below:
1. Surface Plane On The Jointer
—The con-
cave face of the workpiece is surface planed flat
with the jointer.
Previously
Jointed Edge
Previously
Surface
Planed Face
2.
Surface Plane On a Thickness Planer
—The
opposite face of the workpiece is surface planed
flat with a thickness planer.
3. Edge Joint On The Jointer
—The concave
edge of the workpiece is jointed flat with the
jointer.
4. Rip Cut On A Table Saw
—The jointed edge
of the workpiece is placed against a table saw
fence and the opposite edge cut off.
Squaring Stock
Summary of Contents for G0604
Page 2: ......
Page 14: ...12 G0604 6 X 56 Jointer Hardware Recognition Chart...
Page 45: ...G0604 6 X 56 Jointer 43 Jointer Parts Breakdown...
Page 48: ...46 G0604 6 X 56 Jointer Stand Motor Parts Breakdown...
Page 52: ...50 G0604 6 X 56 Jointer...
Page 55: ......