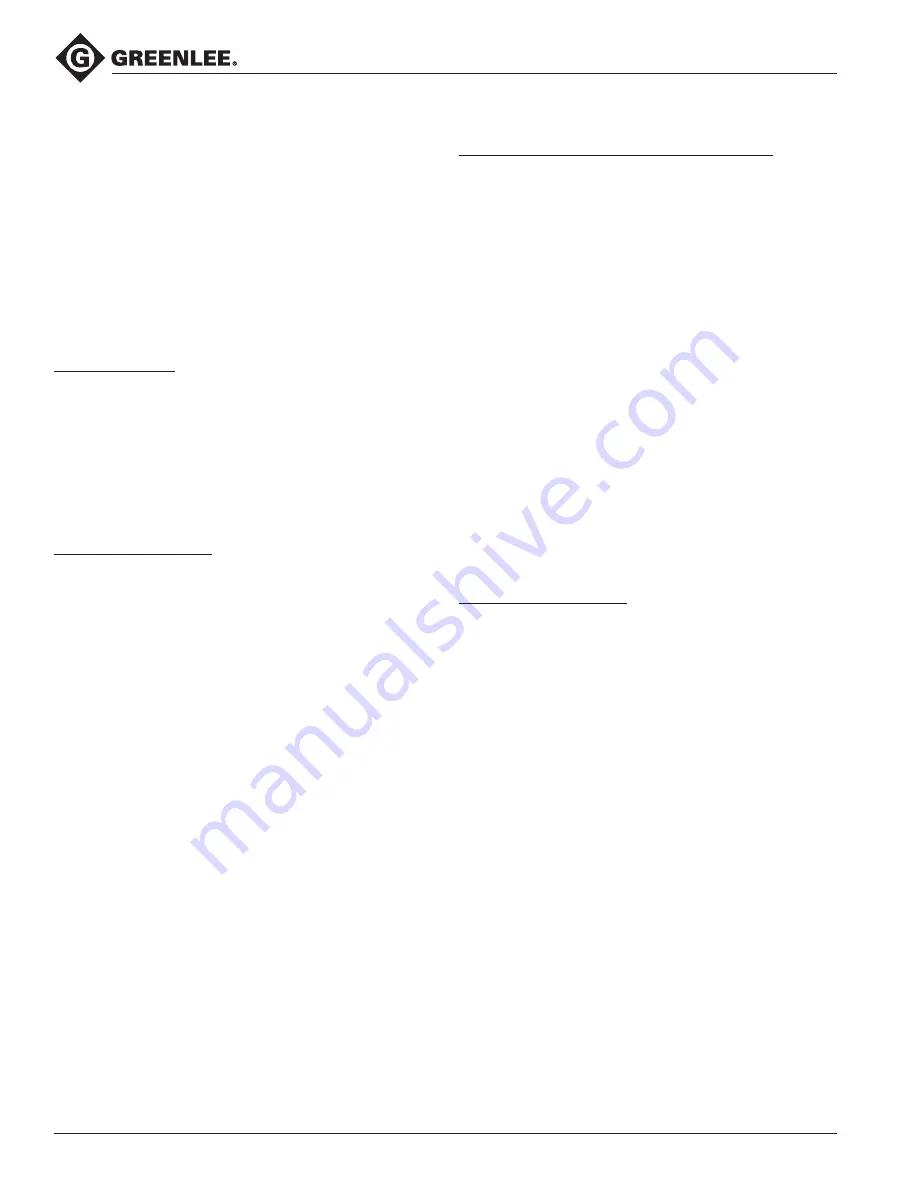
Ultra Tugger
®
Cable Puller and Pulling Packages
Greenlee / A Textron Company
4455 Boeing Dr. • Rockford, IL 61109-2988 USA • 815-397-7070
20
Cable Pulling Principles
(cont’d)
Tailing the Rope
The rope must be pulled off of the capstan as the pull
progresses. The rope that has left the capstan is the
“tail.” The process of pulling the rope off of the capstan
is called
tailing the rope
.
The resistance of the cable varies throughout the
duration of the cable pull. Changes in resistance are
due to characteristics of the rope, changes in conduit
direction, and changes in the amount of friction. The
“feel” of the rope provides this information about the
pull. This is called
tactile feedback
. Adjust the tailing
force as necessary to compensate for these changes.
Control of the Pull
Decreasing the tailing force will decrease the pulling
force, until the rope slips on the capstan and the pull
stops. This provides a high level of control over the
progress of the cable pull.
Do not allow the rope to slip on the capstan for more
than a few moments. If it becomes necessary to com-
pletely stop a pull, shut off the puller and maintain
enough tailing force to hold cable in place. Tie the rope
off to hold it in place.
Amount of Tailing Force
While the rope and cable are under tension, it is impor-
tant to maintain the proper amount of tailing force.
Too little
tailing force will allow the rope to slip on the
capstan. This will build up excessive heat and accelerate
rope wear, increasing the possibility of breaking the rope.
The proper amount of tailing force will stop the rope
from slipping on the capstan and produce a sufficient
amount of pulling force to pull in the rope and cable.
Too much
tailing force is any amount more than is
necessary to stop the rope from slipping on the
capstan. Excessive tailing force will not increase the
pulling force or pulling speed.
Number of Wraps of Rope Around the Capstan
An experienced operator should choose the number
times the rope is wrapped around the capstan.
The proper number of wraps allows the operator to
control the progress of the pull with a comfortable
amount of effort.
Using
too few
wraps requires a large tailing force to
accomplish the pull. Using too few wraps also makes
the rope more likely to slip on the capstan. This builds
up heat and accelerates rope wear.
Using
too many
wraps causes the rope to grab the
capstan tighter. This accelerates rope wear, wastes
power, and increases the possibility of a rope overlap.
Using too many wraps also reduces tactile feedback,
so you receive less information about the pull. You
cannot quickly relax the tailing force when there are too
many wraps.
If the rope becomes difficult to tail, add another wrap
of rope. Turn off the puller and release all of the tension
in the rope. Add a wrap and resume pulling. Be aware,
however, that some pulls will require tension to hold
the cables in place. In these cases, do not attempt to
release all of the tension and add a wrap of rope. You
will need to anticipate the number of wraps before
starting the pull.
Preventing Rope Overlap
Do not allow the rope to become overlapped on the
capstan during a pull.
A rope overlap will make it will impossible to continue
or back out of the pull.
If the rope becomes overlapped, you will lose control
of the pull—the rope will advance with no tailing force
and will not feed off of the capstan. The capstan will not
allow you to reverse the direction of the rope, so you
cannot back out of an overlap.
Set up the puller properly. The rope ramp and tapered
capstan are intended to prevent rope overlap. See the
instructions in the Operation section of this manual.
Every wrap of the rope must remain in direct contact
with the capstan. During the pull, take great care to
prevent the incoming rope from riding up and overlap-
ping the next wrap. If an overlap begins to develop,
immediately relax the tailing force on the rope so that
the rope can feed back toward the conduit or tray.
When the rope resumes its normal path, apply tailing
force and continue the pull.
There is no suggested remedy for a rope overlap.
Do not allow the rope to overlap!