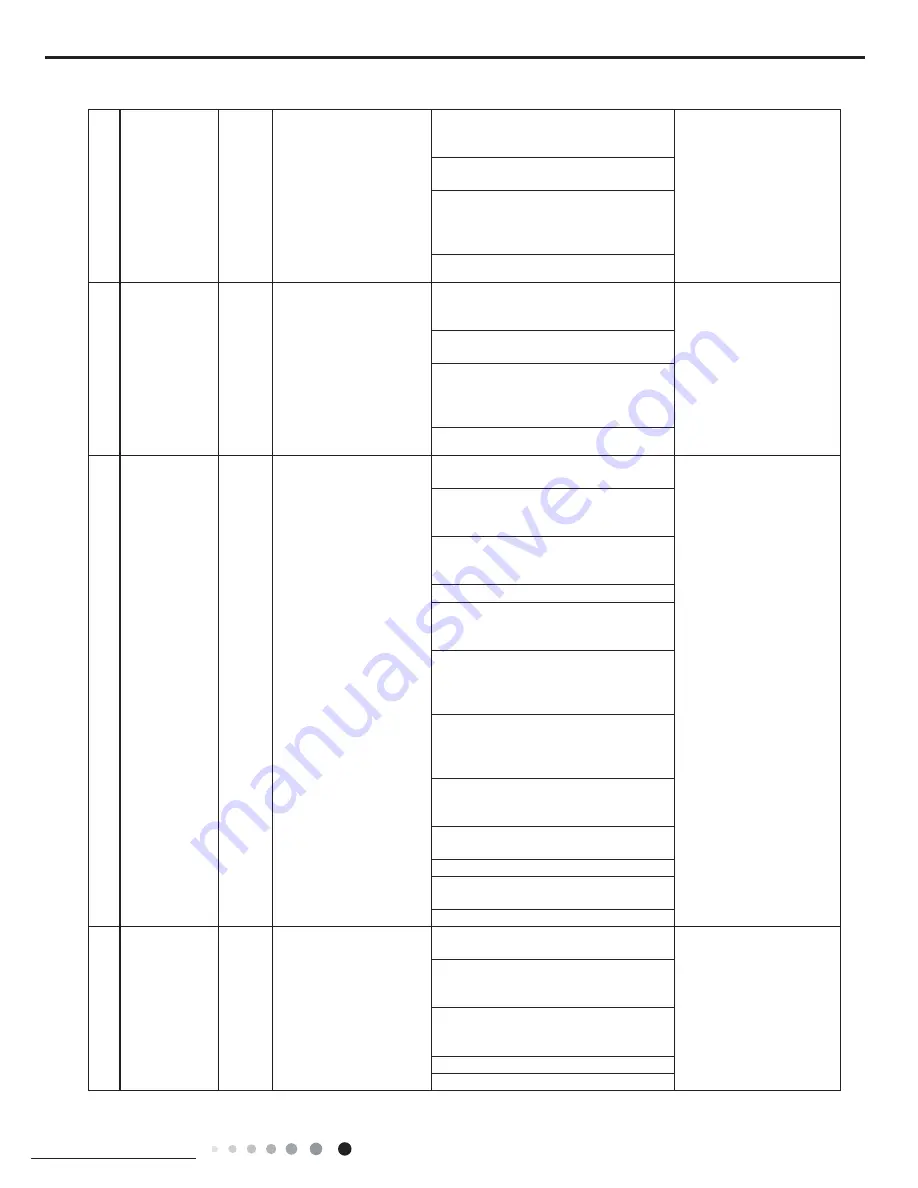
Service Manual
41
Installation and Maintenance
4
Outdoor
condenser
temperature
sensor is open/
short-circuited
F4
The unit will stop
operation as it reaches
the temperature point.
During cooling and drying
operation, the compressor
stops operation while IDU
fan motor operates; During
heating operation, the
heating fan motor operates
according to the conditions
of blowing residual heat.
1. The wiring terminal between outdoor
condenser temperature sensor and
maiboard is loosened or poorly contacted;
Refer to Malfunction
Detection Flowchart
2. There’s short circuit due to trip-over of
the parts on maiboard;
3. Outdoor condenser temperature sensor
is damaged (Please check it by referring
to the resistance table for temperature
sensor);
4. Mainboard is broken.
5
Outdoor
discharge
temperature
sensor is open/
short-circuited
F5
The unit will stop
operation as it reaches
the temperature point.
During cooling and drying
operation, the compressor
stops operation while IDU
fan motor operates; During
heating operation, the
heating fan motor operates
according to the conditions
of blowing residual heat.
1. The wiring terminal between outdoor
discharge temperature sensor and
maiboard is loosened or poorly contacted;
Refer to Malfunction
Detection Flowchart
2. There’s short circuit due to trip-over of
the parts on maiboard;
3. Outdoor discharge temperature sensor
is damaged (Please check it by referring
to the resistance table for temperature
sensor);
4. Mainboard is broken.
6
High pressure
protection
E1
During cooling and drying
operation, except IDU
fan motor operates, all
loads stop operation.
During heating operation,
the complete unit stops
and operation of remote
controller or buttons is
unavailable.
1. The mainboard and the display board
are not connected well;
Refer to Malfunction
Detection Flowchart
2. The OVC terminal on mainboard is not
connected well with the high pressure
switch on the complete unit;
3. The wiring terminal between high
pressure switch and maiboard is loosened
or the high pressure switch is broken;
4. Refrigerant is superabundant;
5. Poor heat exchange (including blocked
heat exchanger and bad radiating
environment );
6. Ambient temperature is too high; (if it is
3-phase unit, the high pressure protection
may be caused by overcurrent protection
due to this reason);
7. The supply voltage is abnormal (if it is
3-phase unit, the high pressure protection
may be caused by overcurrent protection
due to this reason);
8. The air intake and air discharge at
indoor / outdoor heat exchanger are not
smooth;
9. Filter and heat exchange fins of indoor/
outdoor units are blocked;
10. The pipeline is blocked;
11. The gas valve and liquid valve for
outdoor unit are not completely opened;
12. The OVC input is at high level.
7
Low pressure
protection of
compressor
E3
The complete unit stops.
1.The mainboard and display board are
not connected well;
Refer to Malfunction
Detection Flowchart
2. The LPP terminal on the mainboard is
not connected well with the high pressure
switch;
3. The wiring of high pressure switch
is loosened or high pressure switch is
damaged.
4. The refrigerant is insufficient;
5. The LPP input is at high level.