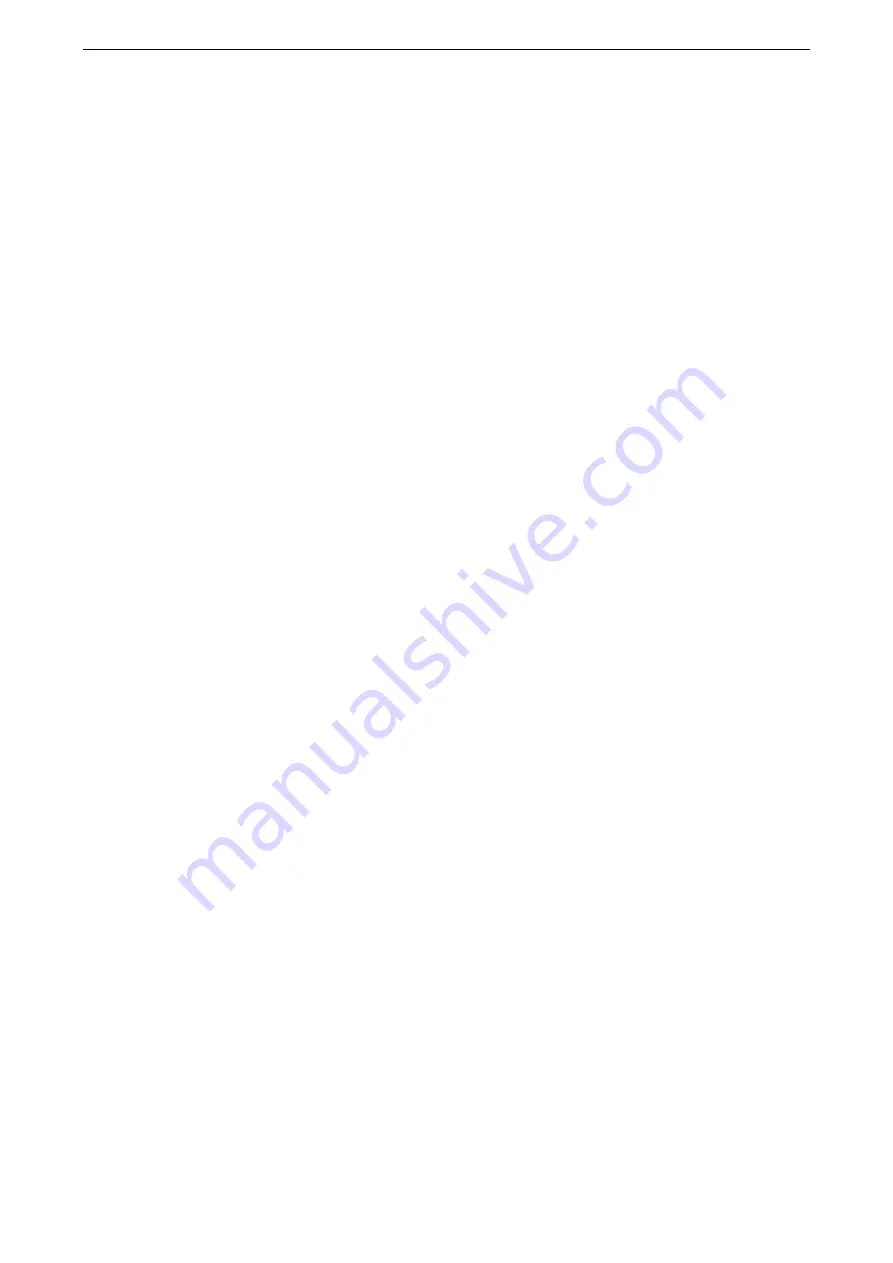
GREE GMV5E DC INVERTER VRF UNITS SERVICE MANUAL
50
6.1.2 Processing to Refrigerant Pipes
6.1.2.1 Cut-off and Burring
Use a special-purpose pipe cutter to cut copper pipes instead of using a hacksaw.
Cut the pipes gently to ensure that the copper pipe does not deform.
After cutting the pipes, use a slicker to grater bur the pipes with the pipe opening inclining downward
so that the copper scales do not fall into the pipe.
Allowable deviation: Skewness of the cross section cannot exceed 1% of the copper pipe caliber.
If the copper pipe is not used immediately after cut-off, cover it with a sealing cap or adhesive tape.
6.1.2.2 Pipe Cleaning
Cleaning with a piece of silk cloth: Wrap a thin steel wire with a piece of clean silk cloth. Crumple the
cloth into a lump with diameter larger than the pipe calibre. Apply several drops of chlorylene to the cloth.
Push the cloth in from one end of the pipe and pull out from the other end. Every time the cloth is pulled
out, remove the dust and sundries with chlorylene. Wash repeatedly until the pipe is clean. This method
applies to straight pipes.
Cleaning with nitrogen: Blow off all dust and sundries in the pipe with nitrogen. This method applies
to coils.
After cleaning, cover the both ends of the pipe with a sealing cap or adhesive tape.
6.1.2.3 Pipe Bending
Processing methods:
Manu
al bending: applies to thin copper pipes (Φ6.35 mm to Φ12.7 mm)
Mechanical bending: applicable range (Φ6.35mm to Φ54.1mm)
Requirements:
The radius of the bending pipe must exceed 3.5D. The ratio of the short diameter after bending to
the original diameter must exceed 2/3.
Precautions:
During bending, there must be no corrugation or deformation inside the pipe.
The welding point of the pipe should not be at the bending part. The distance between the nozzle
welding joint and the bending part should be less than 100 mm.
6.1.2.4 Pipe Expanding
Pipe expanding is used to provide a welding point for pipe connection. Requirements on pipe
expanding are as follows:
(1) All burrs and sundries inside the pipe must be cleared after cut-off.
(2) Before pipe expanding, apply appropriate amount of lubricant on the surface of the pipe. (The
lubricant must meet the refrigerant system’s requirements.)
(3) Pipe expanding length must be in accordance with the insertion depth of the caliber.
(4) To avoid leakage due to straight lines at the expanding point, turn round the copper pipe and
then make corrections.
(5) Apply appropriate force during pipe expanding to avoid crack.