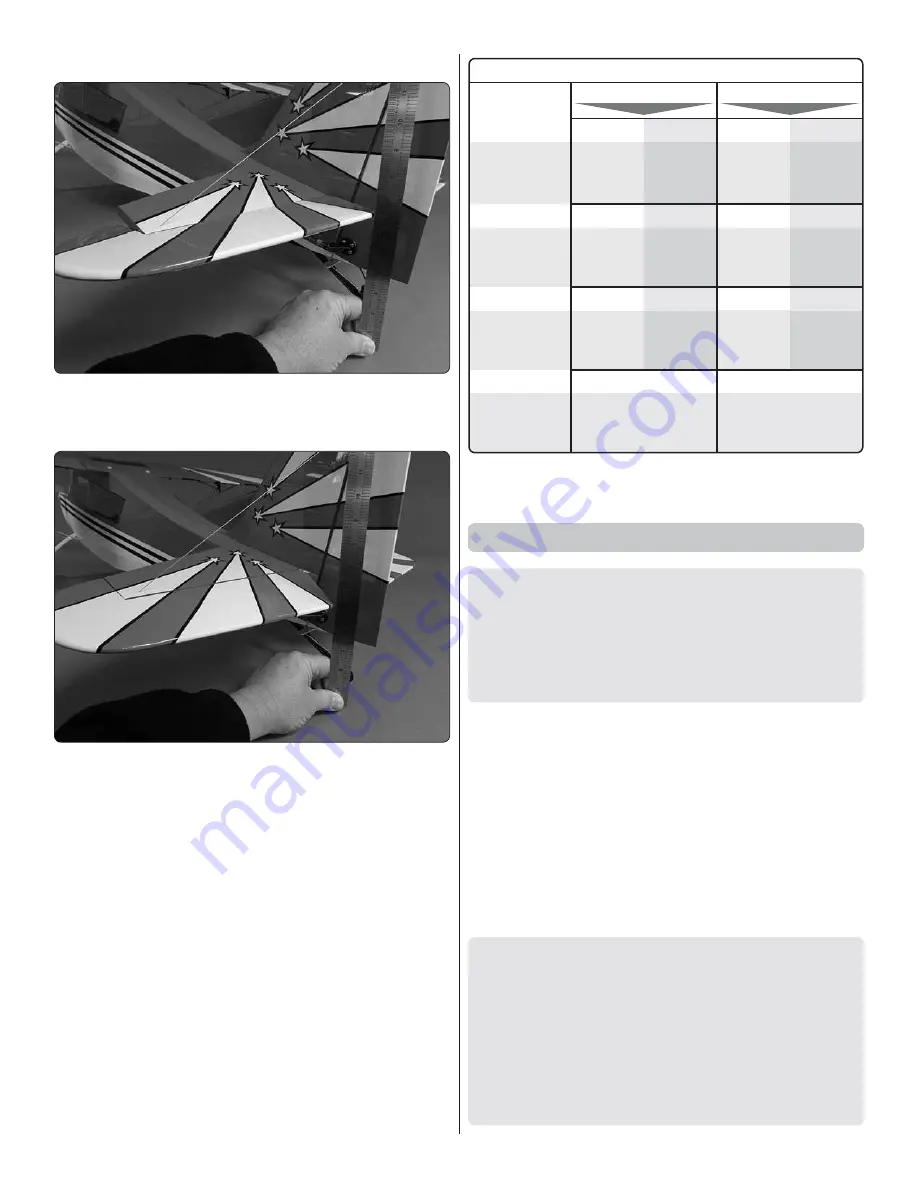
37
Measure the
high rate
elevator throw first…
❏
2. Hold a ruler vertically on your workbench against the
widest part (front to back) of the trailing edge of the elevator.
Note the measurement on the ruler.
❏
3. Move the elevator up with your transmitter and move the
ruler forward so it will remain contacting the trailing edge. The
distance the elevator moves up from center is the “up” elevator
throw. Measure the down elevator throw the same way.
❏
4. If necessary, adjust the location of the pushrod on the
servo arm or on the elevator horn, or program the ATVs in
your transmitter to increase or decrease the throw according
to the measurements in the control throws chart.
❏
5. Measure and set the
low rate
elevator throws and the
high and low rate throws for the rest of the control surfaces
the same way.
Down
Up
Up
Down
These are the recommended control surface throws:
3/4"
[19mm]
11°
7/8"
[22mm]
11°
3/4"
[19mm]
11°
7/8"
[22mm]
11°
3/4"
[19mm]
13°
3/4"
[19mm]
13°
1-3/16"
[30mm]
17°
3/4"
[19mm]
37°
1-3/16"
[30mm]
17°
1-5/8"
[41mm]
23°
1-1/8"
[28mm]
20°
1-1/8"
[28mm]
20°
ELEVATOR
AILERON
LOW
HIGH
RUDDER
Down
Up
Up
Down
Left
Right
Left
Right
5/8"
[16mm]
11°
1"
[25mm]
18°
1-5/8"
[41mm]
23°
FLAPS
Down
Down
NOTE
: The throws are measured at the
widest part
of the
elevators, rudder and ailerons.
Balance the Model (C.G.)
More than any other factor, the C.G. (center of gravity/
balance point) can have the greatest effect on how a model
fl ies and could determine whether or not your fi rst fl ight will
be successful. If you value your model and wish to enjoy it
for many fl ights,
DO NOT OVERLOOK THIS IMPORTANT
PROCEDURE.
A model that is not properly balanced may
be unstable and possibly unfl yable.
At this stage the model should be in ready-to-fly condition with
all
of the components in place including the complete radio
system, engine, muffler, propeller, spinner and pilot. The fuel
tank should be empty.
❏
1. If using a Great Planes C.G. Machine, set the rulers to
3.5" [89mm]. If not using a C.G. Machine, use a fine-point felt
tip pen to mark lines on the top of wing on both sides of the
fuselage 3.5" [89mm] back from the leading edge measured
at the fuselage. Apply narrow (1/16" [2mm]) strips of tape
over the lines so you will be able to feel them when lifting the
model with your fingers.
This is where your model should balance for the fi rst
fl ights. Later, you may experiment by shifting the C.G. 3/16"
[4.8mm] forward or 3/16" [4.8mm] back to change the fl ying
characteristics. Moving the C.G. forward will improve the
smoothness and stability, but the model will then be less
aerobatic (which may be fi ne for less-experienced pilots).
Moving the C.G. aft makes the model more maneuverable
and aerobatic for experienced pilots. In any case,
start at
the recommended balance point
and do not at any time
balance the model outside the specifi ed range.