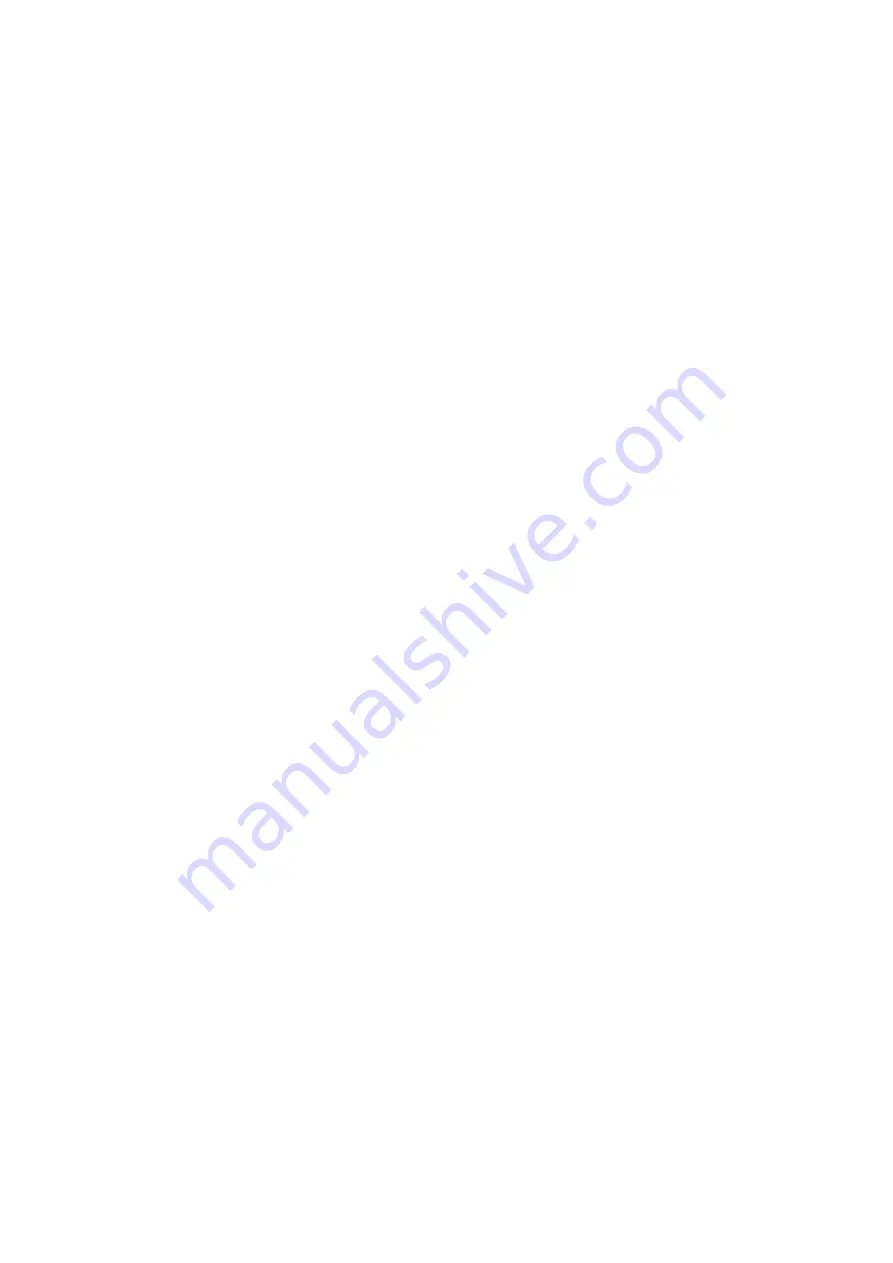
5
Check that there is no possibility of cross-contamination between the different refrigerants when using charging
equipment. Hoses or lines must be as short as possible to reduce the quantity of refrigerant contained therein.
Cylinders must be kept in an appropriate position, in accordance with the instructions.
Check that the cooling system is grounded before charging the system with refrigerant.
Label the system once charging is complete (if this is not already the case).
Pay close attention to not overfilling the cooling system.
Before recharging the system, carry out a pressure test using a suitable purge gas. The system must be examined to
make sure there are no leaks after the charging operation and before commissioning. A follow-up leak test must be carried
out before leaving the site.
Dismantling
Before dismantling, the technician must familiarise himself/herself with the equipment and its specifications. We highly
recommend carefully recovering all refrigerants. Before this, oil and refrigerant samples must be taken if analyses are to be
carried out before any other use of the recovered refrigerant. Check for the presence of a power supply before starting
work.
1. Familiarise yourself with the equipment and how it operates.
2. Electrically isolate the system.
3. Before starting work, check the following points:
- mechanical handling equipment is available if needed to handle the refrigerant cylinders;
- all personal protective equipment is available and used correctly;
- the recovery process is followed at all times by a cognizant person;
- the recovery cylinders and equipment comply with the relevant standards.
4. Drain the cooling system where possible.
5. If a vacuum cannot be created, install a manifold in order to be able to remove the refrigerant from various locations
within the system.
6. Make sure that the cylinder is located on the scales before starting recovery operations.
7. Start the recovery unit and operate as per its instructions.
8. Do not overfill the cylinders (no more than 80% of the volume must be filled with liquid).
9. Do not exceed the maximum working pressure of the cylinder, even temporarily.
10. When the cylinders have been filled correctly and the process is complete, check that the cylinders and the equipment
are quickly removed from the site and that the alternative shut-off valves on the equipment are closed.
11. The recovered refrigerant must not be charged in another cooling system, unless it has been cleaned and inspected.
TROUBLESHOOTING
All brazing must be carried out by qualified brazers.
Replacement pipes must always be made of copper in compliance with standard NF EN 12735-1.
Leak detection; pressure test:
- never use oxygen or dry air, risk of fire or explosion,
- use dry nitrogen or the mixture of nitrogen and refrigerant indicated on the information plate,
- the test pressure for both the high and low pressure circuits must not exceed 42 bar in cases where
the appliance is equipped with the optional pressure gauge.
The high pressure circuit pipes are made of copper and have a diameter equal to or greater than 1’’5/8. A certificate as
indicated in §2.1 in compliance with standard NF EN 10204 must be requested from the supplier and filed in the
installation’s technical file.
Technical data relative to the safety requirements of the various applicable directives are indicated on the information
plate. All this information must be recorded in the appliance’s installation manual, which must be kept in its technical file:
model, code, serial number, maximum and minimum OT, OP, year of manufacture, CE marking, manufacturer’s address,
refrigerant and weight, electrical parameters, thermo-dynamic and acoustic performance.
LABELLING
The equipment must be labelled so as to specify that it is out of order and that the refrigerant has been drained.
The label must be dated and signed.
For appliances containing a flammable refrigerant, check that labels are placed on the equipment stating that it contains
a flammable refrigerant.
RECOVERY
When draining the refrigerant for maintenance or decommissioning, best practices should be followed in order to safely
drain all of the refrigerant.
When transferring refrigerant to a cylinder, make sure that you use a recovery cylinder that is compatible with the
Summary of Contents for HPG25
Page 2: ......
Page 12: ...9 2 Dimension unit mm Model HPG25 Model HPG40 HPG50...
Page 20: ...17 Dry contact timer connection Timer Dry contact pump connection...
Page 21: ...18 5 Electrical Wiring 5 1 SWIMMING POOL HEAT PUMP WIRING DIAGRAM HPG25 HPG40 HPG50 HPG70...
Page 28: ...25 8 Exploded Diagram Model HPG25...
Page 30: ...27 Model HPG40 HPG50...
Page 32: ...29 Model HPG70...
Page 43: ...40 2 Dimensiones mm Modelos HPG25 Modelos HPG40 HPG50...
Page 60: ...57 8 Diagrama Explosionado Model HPG25...
Page 62: ...59 Model HPG40 HPG50...
Page 64: ...61 Model HPG70...
Page 76: ...73 2 Dimension mm Mod le HPG25 Mod les HPG40 HPG50...
Page 86: ...83 5 C blage Electrique 5 1 Sch ma de c blage de la pompe chaleur HPG25 HPG40 HPG50 HPG70...
Page 94: ...91 8 Sch ma Eclat Mod le HPG25...
Page 96: ...93 Mod le HPG40 HPG50...
Page 98: ...95 Mod le HPG70...
Page 110: ...107 2 Dimension mm Modell HPG25 Modell HPG40 HPG50...
Page 126: ...123 8 Explosionszeichnung Modell HPG25...
Page 128: ...125 Modell HPG40 HPG50...
Page 130: ...127 Modell HPG70...
Page 142: ...139 2 Dimensione mm Modelli HPG25 Modelli HPG40 HPG50...
Page 145: ...142 3 5 Disposizione tipica Nota Questa disposizione solo un esempio illustrativo...
Page 151: ...148 5 Cavi Elettrici 5 1 PISCINA POMPA DI CALORE SCHEMA HPG25 HPG40 HPG50 HPG70...
Page 159: ...156 8 Exploded Diagram Model HPG25...
Page 161: ...158 Model HPG40 HPG50...
Page 176: ...173 2 Dimensie mm Model HPG25 Model HPG40 HPG50...
Page 179: ...176 3 5 Typische set up Opmerking Deze set up is alleen een voorbeeld voor demonstratie...
Page 184: ...181 Dry contact timer verbinding Timer Dry contact pomp aansluiting...
Page 185: ...182 5 Elektrische bedrading 5 1 ZWEMBAD WARMTEPOMP BEDRADING SCHEMA HPG25 HPG40 HPG50 HPG70...
Page 192: ...189 8 Ge xplodeerd Diagram Modellen HPG25...
Page 194: ...191 Modellen HPG40 HPG50...
Page 196: ...193 Modellen HPG70...
Page 208: ...205 2 Dimens o mm Modelo HPG25 Modelo HPG40 HPG50...
Page 211: ...208 3 5 Disposi o t pica Nota Esta disposi o apenas um exemplo ilustrativo...
Page 216: ...213 Conex o do temporizador de contacto seco Cron metro Conex o da bomba de contacto seco...
Page 224: ...221 8 Diagrama Explodido Modelo HPG25...
Page 226: ...223 Modelo HPG40 HPG50...
Page 228: ...225 Modelo HPG70...
Page 240: ...237 2 Wymiary Model HPG25 jednostka mm Model HPG40 HPG50...
Page 251: ...248 Bezpotencja owe po czenie pompy 5 Okablowanie elektryczne HPG25 HPG40...
Page 263: ...260 8 Schemat budowy pompy Model HPG25...
Page 265: ...262...
Page 267: ...264 Model HPG70...
Page 278: ......