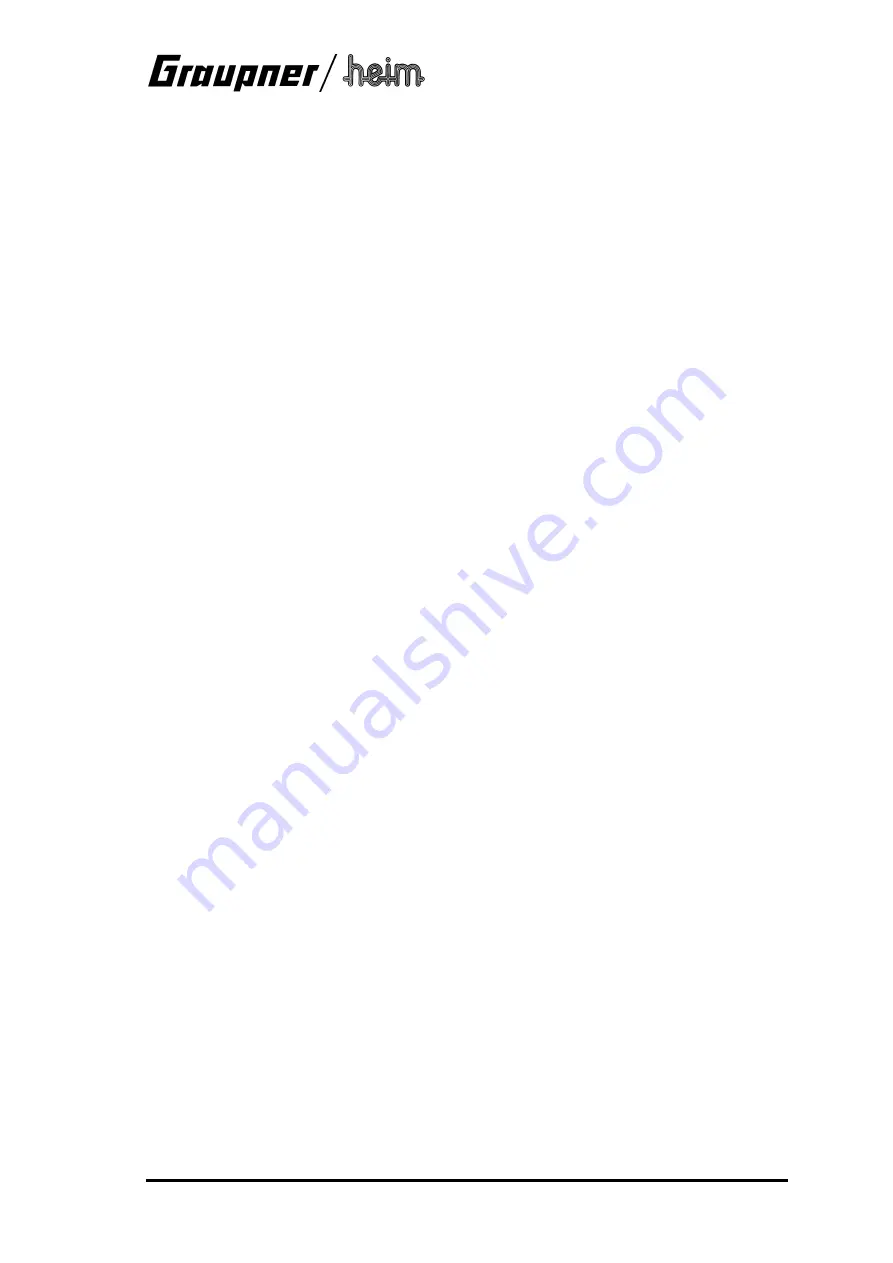
Micro Star 400 v2
13
The collective pitch servo should produce a range of blade pitch angles covering -8° to +9°,
with symmetrical travels; you may find it necessary to remove the servo output arm, move it
round by one spline and fit the retaining screw again. When the collective stick is at centre
(hover point), collective pitch should be about 3°, and the speed controller should be at the
"half-throttle" position.
Note:
The collective pitch and power curves can be adjusted later to meet your exact personal re-
quirements. However, if you have already set differential travels in the basic set-up proce-
dure, as shown in diagram "B" above, any fine adjustments required subsequently will be
more difficult!
6. Collective pitch and power curves
These adjustments are of fundamental importance to the flight performance of any model
helicopter. The aim of the procedure is to maintain a constant rotor speed when the model is
climbing and descending, i.e. regardless of load. This then represents a stable basis for fur-
ther fine-tuning, e.g. of the torque compensation system etc. (see also "Collective pitch and
throttle curves").
7. Static torque compensation
The tail rotor servo is coupled to the collective pitch function via a mixer in the transmitter in
order to compensate for changes in torque when you operate the collective pitch control. On
most transmitters the mixer input can be set separately for climb and descent. Recom-
mended values for the basic settings are: climb: 35%, descent: 15%.
8. Gyro adjustment
Gyro systems damp out unwanted rotational movements around the vertical (yaw) axis of the
model helicopter. They do this by detecting the unwanted motion and injecting a compensa-
tory signal into the tail rotor control system, and in order to achieve this effect the gyro elec-
tronics are connected between the tail rotor servo and the receiver.
The gyro systems recommended for the Micro Star 400 v2 either feature a gain adjustor,
which should initially be set to 50% gain, or alternatively the gyro gain can be adjusted from
the transmitter using a supplementary channel (see gyro system instructions).
Check that the direction of the gyro’s compensatory action is correct, i.e. that it responds to a
movement of the tail boom with a tail rotor movement in the opposite direction. If this is not
the case, any yaw movement of the model would be amplified by the gyro! If it works the
wrong way round, the solution is to operate the reverse switch on the gyro, or mount the gyro
inverted.
One factor which is common to all gyro systems is that flight testing is necessary in order to
establish the optimum settings, as so many different factors influence them.
The aim of the gyro adjustment process is to achieve as high a level of stabilisation as pos-
sible without the gyro causing the tail boom to oscillate.
3. Final checks before the first flight
When you have completed the model, please run through the final checks listed below before
the first flight:
•
Study the manual again and ensure that all the stages of assembly have been completed
correctly.
•
Check that all the screws in the ball-links and brackets are tightened fully after you have
adjusted gear meshing clearance.
•
Can all the servos move freely, without mechanical obstruction at any point? Do they all
rotate in the correct direction relative to the stick movements? Are the servo output arm
retaining screws in place and tight?
•
Check the direction of effect of the gyro system.
•
Ensure that the transmitter and flight batteries are fully charged.
Don’t attempt to fly the helicopter until you have successfully checked everything as described
above.
Summary of Contents for Micro Star 400
Page 28: ...Micro Star 400 v2 4 Notes...