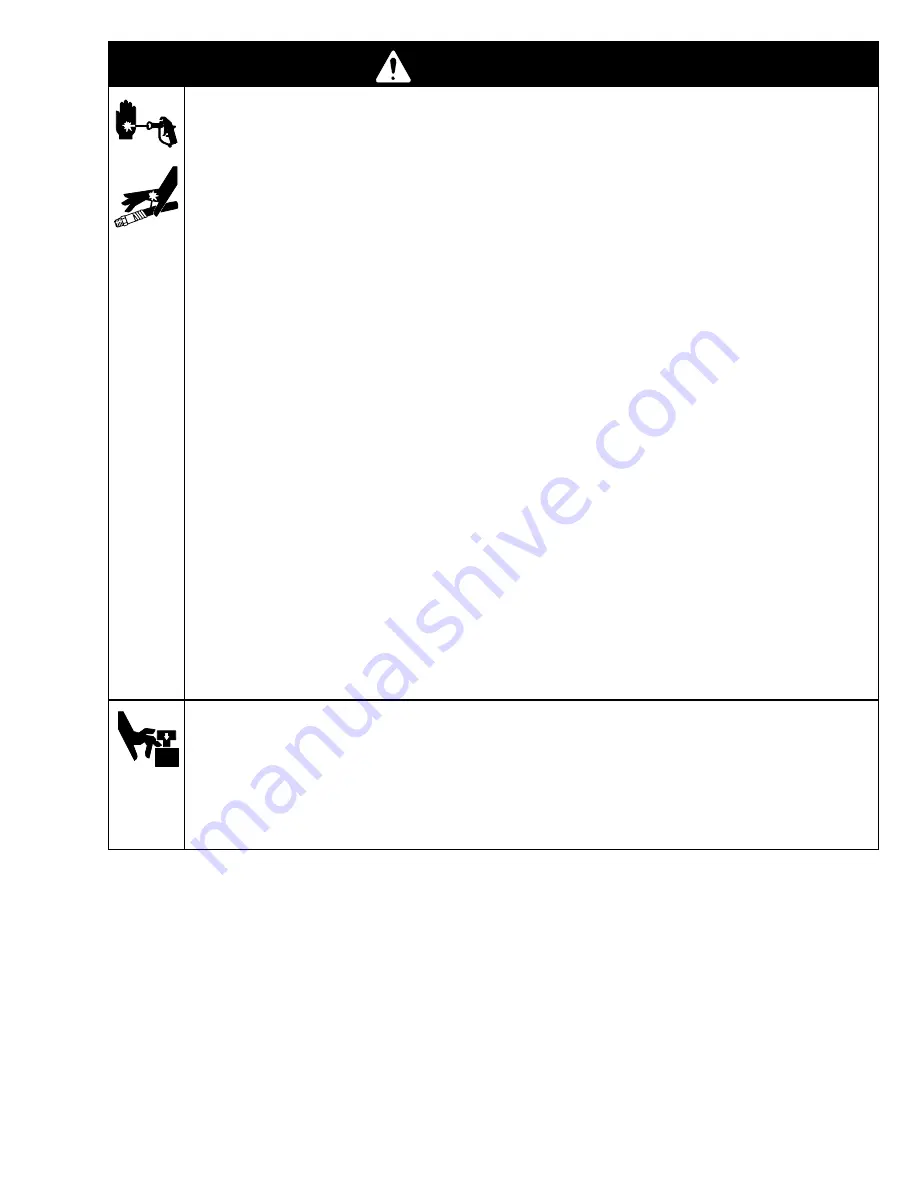
3
307622
WARNING
INJECTION HAZARD
Spray from the gun/valve, hose leaks, or ruptured components can inject fluid into your body and
cause extremely serious injury, including the need for amputation. Fluid splashed in the eyes or on the
skin can also cause serious injury.
D
Fluid injected into the skin might look like just a cut, but it is a serious injury.
Get immediate medi-
cal attention.
D
Do not point the gun/valve at anyone or at any part of the body.
D
Do not put your hand or fingers over the spray tip/nozzle.
D
Do not stop or deflect leaks with your hand, body, glove or rag.
D
Do not “blow back” fluid; this is not an air spray system.
D
Always have the tip guard and the trigger guard on the gun/valve when spraying.
D
Be sure the gun/valve trigger safety operates before spraying.
D
Lock the gun/valve trigger safety when you stop spraying.
D
Follow the
Pressure Relief Procedure
on page 8 whenever you: are instructed to relieve pres-
sure; stop spraying; clean, check, or service the equipment; and install or clean the spray tip/
nozzle.
D
Tighten all fluid connections before operating the equipment.
D
Check the hoses, tubes, and couplings daily. Replace worn, damaged, or loose parts immediately.
Permanently coupled hoses cannot be repaired; replace the entire hose.
D
Use only Graco approved hoses. Do not remove any spring guard that is used to help protect the
hose from rupture caused by kinks or bends near the couplings.
MOVING PARTS HAZARD
Moving parts, can pinch or amputate your fingers.
D
Keep clear of all moving parts when starting or operating the pump.
D
Before servicing the equipment, follow the
Pressure Relief Procedure
on page 8 to prevent the
equipment from starting unexpectedly.