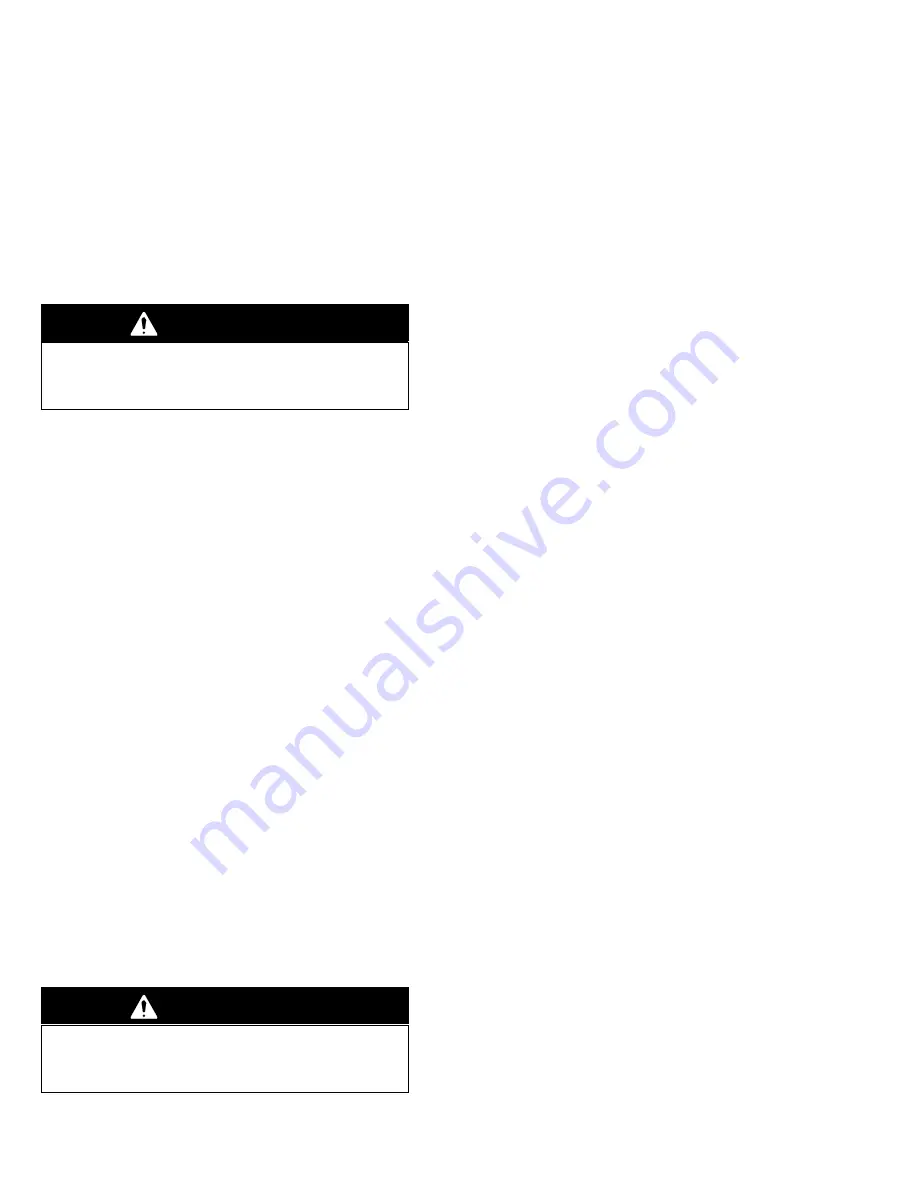
10ą307056K
Service
Displacement Pump Disassembly
NOTE: Repair Kit 218–741 is available. The parts
included in the kit are marked with an asterisk (for
example, 8*). See page 13. Use all the parts in the kit
for the best results.
1.
Remove the pump from the fluid container. Oper-
ate it until as much of the fluid has been pumped
out as possible.
WARNING
To reduce the risk of serious injury whenever you
are instructed to relieve pressure, always follow the
Pressure Relief Procedure on page 6.
2.
Relieve the pressure and remove the air and fluid
hoses from the pump.
3.
Remove the intake valve housing (18) by removing
the retaining pin (16) and the o-rings (20) and
pulling the valve out of the cylinder (2). Disas-
semble the valve. Clean and inspect the parts. See
Fig. 3.
4.
Release the clamp (7) holding the retainer housing
(22) to the air motor base. Slide the displacement
cylinder (2) down from the air motor and pull the
displacement rod (3) out of the connecting rod
(21). Inspect the connecting rod o-ring (28).
5.
Push the displacement rod out through the bottom
of the cylinder. Remove the piston housing (26) by
removing the retaining pin (25) and the o-ring (20)
and pulling the piston from the displacement rod.
Disassemble, clean and inspect the parts.
6.
Take the retainer housing (22) off of the cylinder
(2) and remove the packing housing (24), bearing
(17) and packing (8).
7.
Clean and inspect all the parts. Refer to the
Cleaning Procedure on page 7. Replace the
parts as necessary.
WARNING
Any damaged rubber parts
must be replaced as
they will harbor microorganisms that can contami-
nate the fluid.
Displacement Pump Assembly
NOTE: Lubricate the o-rings, throat packings, and
piston seals with waterproof approved sanitary lubri-
cant when reassembling.
1.
Install the u-cup packing (8*) and throat bearing
(17*) in the throat packing housing (24). The lips of
the u-cup must face down into the housing, and
the lip of the bearing must face up. Install the
o-ring (13*) on the outside of the housing. See
Detail A of Fig. 3.
2.
Place the throat packing housing (24) on the top of
the cylinder (2). Make sure the gasket (12*) is in
place on the top of the cylinder (2). Install the
retainer housing (22) on the cylinder so the hole
(A) in the housing is slanting downward toward the
cylinder. Secure with the clamp (7).
3.
Install the piston seal (19*) on the piston housing
(26). Place the ball (9) on the seat of the housing.
Install the piston housing in the displacement rod
(3) so the holes in both parts align. Secure with the
retaining pin (25) and one o-ring (20*). See Detail
B.
4.
Lubricate the connecting rod o-ring (28) with
sanitary lubricant. See the parts drawing, page 12.
5.
Slide the displacement rod (3) up through the
cylinder (2) so it protrudes from the retainer hous-
ing (22). Install the gasket (12*) on the top of the
retainer housing. Make sure the drip shield (11) is
in place on the connecting rod (21), then reconnect
the displacement rod to the connecting rod.
6.
Slide the retainer housing (22) and cylinder (2) up
to the base of the air motor (1), and secure with
the clamp (7). Make sure the drip shield (14) is in
place on the cylinder.
7.
Install the o-ring (13*) on the intake valve housing
(18). Place the ball (10) on the seat of the housing
(18), and install the ball stop pin (23) in the top
holes of the housing. See Detail C.
8.
Slide the intake valve housing (18) up into the
cylinder (2) until the bottom holes of the housing
align with the holes in the cylinder. Secure using
the retaining pin (16) and two o-rings (20*).
9.
Install the gasket (15*) and clamp (5) when recon-
necting the fluid line to the pump fluid outlet.
10. Reconnect the ground wire if it was disconnected
during service.
Summary of Contents for Monark 207550
Page 8: ...8 307056K Notes...